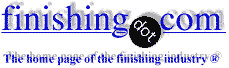
-----
Hardness values for hard anodize
Q. I am having trouble with the hard anodize being able to meet the Taber requirements for MIL-A-8625 / MIL-PRF-8625 [⇦ this spec on DLA] consistently. Specifically the 7075 material. I am getting the thickness without a problem (.002-.0021) but the weight per 10,000 cycles is like 2.4-2.4mg. Curiously, this is true for both the 2024 and the 7075 materials. I have tried increasing the amount of oxalic acid in the bath to the higher end of the required range, but this only had temporary benefits. I also bake the panels after processing to ensure a minimum of moisture is maintained within the pore structure of the panels. This again only seemed to have temporary benefits. My question is, is there any type of additive or trick to obtain a harder more Taber resistant surface? Any and all help in this situation is greatly appreciated
Steven van Raayjob shop - Downey, California
2003
A. Both of those alloys are very high copper which make it very difficult to get a great coating. It probably will require slightly cooler or better solution agitation and possibly higher amperage or both. Hard anodizers that have found a solution to the problem are normally reluctant to talk about the precise method they use. Also, you did not provide any information on your method/parameters, so how can any expert suggest any improvement-specifically rather than generalities.
James Watts- Navarre, Florida
A. The following answers also apply to this question.1) Temp must be consistent through out the bath ±1f (prefer 32f). 2) Air must be VIGOROUS and extremely even. 3) All contacts must be very secure (bolted/aluminum racks preferred). 4)Acid concentration should be close 200 grams per liter or higher and other parameters must be maintained within guidelines.5) Segregate alloys and don't mix batches.6) Use aluminum cathodes 6063T6 at a ratio of 3-1.7) Anodize by asf not voltage not at around 24 asf. 8) Use a quality additive! 9) Most important call a supplier that really knows todays anodizing from chemistry to equipment!
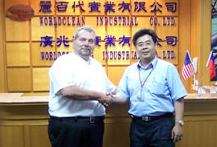
Drew Nosti, CEF
Anodize USA

Ladson, South Carolina
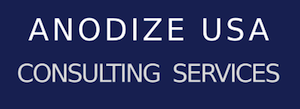
2003
A. Oxalic is on the way out. Glycolic/Glycerin has arrived as developed by Reynolds and sold as a proprietary by about 6 different companies.
On 7075 Reynolds got less Mg loss with 10 000 cycle, using the glycolic additive versus the oxalic additive. Their published data shows: 7075, 2.5 mils, 34.3 mg per 0.001, and 17.3 mg loss (test data from Frankford Arsenal). With the Martin and the Alumilite 226 (oxalic) they got a Taber loss of 21 and 29.2.
Use 4%/vol of a certain proprietary additive, 165 gm/L of acid, 32 F, 24 amps per square foot after a 15 minute ramp, and remember that half the thickness is under the original surface location.
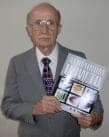
Robert H Probert
Robert H Probert Technical Services

Garner, North Carolina
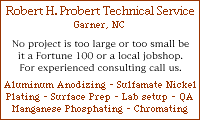
2003
The preceding responses have already commented on parameters such as agitation, temperature, acid concentration, etc. Are you using 12% sulfuric + 1.5% oxalic (wt%) or what?
Once the other parameters are optimized, you may have to empirically determine the correct voltage ramping rate (to maintain
36 ASF or whatever is proper for your electrolyte). Too slow ramping results in slower buildup and softer anodize, as the acid has more time to enlarge the pores. Too rapid ramping creates excessive heat and softer coatings.
Also, make sure that Type III test panels are at least 0.063Ä thick; I know of a case where 0.032Ä Type II panels were used.
You made two rather curious statements: 1) Increasing the oxalic acid concentration gives temporary benefit. Does the benefit last until the oxalic decreases? 2) Baking the panels after processing gives temporary benefits. I'm not sure what this means (how hot?) or whether your reasoning is correct, but such baking seems to violate the MIL-A-8625F requirements for unsealed Type III coatings in paragraphs 3.8.2 and 4.3.3.2. Baking certainly crazes hard anodize, which is detrimental for corrosion resistance.
- Goleta, California

Rest in peace, Ken. Thank you for your hard work which the finishing world, and we at finishing.com, continue to benefit from.
Q, A, or Comment on THIS thread -or- Start a NEW Thread