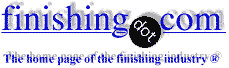
-----
Aluminum Pretreatment: 3-step Iron Phosphate vs. Chromate Conversion Coating
Q. Dear all,
We are designing a pre-treatment line prior to powder coating for some aluminium alloys.
The alloys are of series: 2XXX, 6XXX, 7XXX.
some are: 6082 & 7075.
We want to know the best treatment process for these alloys in order to maintain a high period in Salt spray test, above 1000 hours.
- Dubai UAE
March 4, 2021
A. Hi El. Chromate conversion coating is the only way to go, although you can use trivalent chromates per MIL-DTL-5541 [⇦ this spec on DLA] these days rather than hexavalent. You really ought to design for real-world corrosion resistance needs rather than designing to the test; and some parts depending on their shape may not resist 1000 hours with just powder coating due to possible difficulties in getting even coatings, but might need electrocoating first. It is difficult to detail the exact pretreatment parameters required for a wide range of different alloys of unknown size and shape, but the steps are clean, etch, desmut, chromate conversion coat with adequate rinsing between the steps.
Luck & Regards,
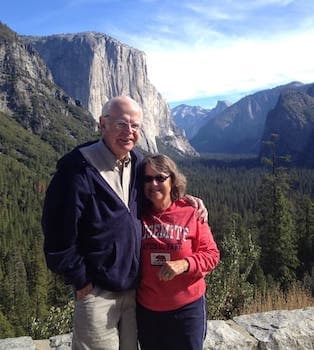
Ted Mooney, P.E. RET
Striving to live Aloha
(Ted can offer longterm or instant help)
finishing.com - Pine Beach, New Jersey
March 2021
⇩ Related postings, oldest first ⇩
Q. How well does Iron Phosphate rival Conversion Coatings (i.e., Alodine, Iridite) of aluminum either as a pre-paint treatment or for corrosion protection? I had always thought of iron phosphate as an excellent paint base for ferrous metals only. Do you think that IP offers good protection as well for aluminum, either painted or unpainted? What are advantages and disadvantages? Is iron phosphate always black in color?
Jimmy ValleoNLYNX SYSTEMS
1999
A. Dear Jimmy,
The Chromate Conversion Process is far superior over iron phosphate process for Aluminium. As a matter of fact the phosphate coating is a dull coating over Aluminium and I suggest you not use it (from my hard experience).
Iron phosphate is not always black; in most cases it's colorless to yellowish, reddish.
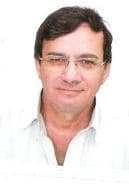
Yehuda Blau
YB Plating Engineering and Quality - Haifa Israel
1999
A. Phosphate is normally used on aluminum when you have steel fittings as well as the aluminum.
My experience has been that there is a very poor visual check for quality. If you go with phosphate, iron or zinc, it needs to be formulated primarily for aluminum. I would also require that a tech service person from that supplier come in for the actual startup.
Alodine or Iridite will be better, for most companies, than phosphate.
James Watts- Navarre, Florida
1999
A. This is a quick easy answer. Conversion coating processes (Alodine, Iridite) are light years better for corrosion protection. Iron Phosphate has many colors, but does not manifest itself on aluminum, because it does little but etch the surface of the aluminum, if it contains fluoride.
Zinc phosphate over aluminum is a difficult but effective pretreatment for painting and produces a uniform grey coating.
The reason you can't see iron phosphate on aluminum is that it does not actually lay down a coating. Remember that corrosion protection is not only dictated by the pretreatment, but also by judicious choice of the coating. Most powder coatings today can provide a substantial amount of corrosion protection to aluminum with an iron phosphate pretreatment. The patio furniture industry loves it.
Also there is the environmental impact of chrome to consider. Iron phosphate offers a more environmentally sound alternative to chrome conversions.
Iron phosphate will not provide any protection to unpainted parts. Zinc Phosphate may provide some protection, but nothing in the range of chrome.


Craig Burkart
- Naperville, Illinois
1999
Thanks Craig.
opinion! Not to be argumentative about 'environmental impact', but our landfills are drowning in crappy corroded patio furniture and outdoor metal stuff that now lasts only 2 or 3 years instead of the 15-20 years it used to last, should last, and could very easily last ... and the reason is pennywise pound-foolishness regarding environmental impact.
This in turn keeps the mines, earth movers, smelters, fab shops, trucks, paint suppliers, applicators, packaging manufacturers, warehouses, retailers, and everyone else relentlessly & unsustainably polluting our environment, wastefully re-manufacturing yet another round of the same junk, and yet another and another. As you say, chromate conversion coating is light years better -- so worrying about the ounce of environmental impact from properly finishing metals to interrupt this pattern of unsustainable and environmentally criminal waste caused by improper finishing is wrong. Finish those millions of tons of patio furniture right once, and cheerfully accept the 1000:1 environmental benefit of applying the necessary grams of chrome to those tons of steel and aluminum :-)
Regards,
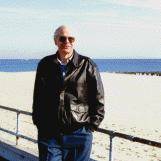
Ted Mooney, P.E.
Striving to live Aloha
(Ted can offer longterm or instant help)
finishing.com - Pine Beach, New Jersey
Multiple threads merged: please forgive chronology errors and repetition 🙂
2002
Q. Can iron phosphate be applied to aluminum? If yes, what are the limitations?
Donald Bradburyconsulting - Loves Park, Illinois, USA
A. It can be applied, it just doesn't do enough good :-)
Phosphatizing of aluminum is not as good as chromate conversion coating. But if it is applied, you probably want a special formulation with fluoride in it to at least etch the aluminum.
Handling aluminum parts along with steel parts in a phosphatizing solution is called "mixed metal phosphatizing".
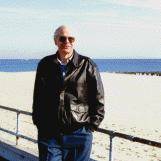
Ted Mooney, P.E.
Striving to live Aloha
(Ted can offer longterm or instant help)
finishing.com - Pine Beach, New Jersey
2002
2002
A. Iron Phosphate products in this context don't contain any iron, the source of iron in pre-paint applications comes from the substrate. What you get with Iron Phosphating over aluminum is an acid wash, and if fluoride is used you get a small amount of passivation by forming a fluoride/aluminum complex. This passivation works exactly like the stable oxide layer on stainless (or aluminum for that matter) but is less stable and thinner than chromate passivation.
Iron Phosphating of aluminum is widely done successfully, by using good reactive polymeric final rinses and getting the parts painted as quickly as possible. Your quality requirements and your ability to treat the waste you create will determine which of chromating or phosphating is best for you.
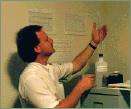
Jeff Watson
- Pearland, Texas
Q. We are considering forming an assembly then painting, rather than painting the individual parts then assembling. My question is: the assembly is made up of mild steel box section and aluminum castings; the castings will pretreated by anodizing or Alocroming as this is a readily available treatment in the area. Once assembled the assembly will pass through an iron phosphate spray tank prior to being painted. Am I asking for trouble spraying over the already pretreated aluminum?
Daniel Wallaker- Southend, Essex, UK
2002
Pre-treatment for aluminum furniture
Q. We have recently started making aluminum chairs and tables for a company in UK and they have asked us to supply the chairs with a epoxy zinc rich primer as a primary (alpha) coat. They will powder coat the chair in their facility in UK. I want to know whether zinc rich primers are required for aluminum items or not as an undercoat to powder coating?
The requirement also states that the epoxy zinc rich primer should not be air dried but should be oven baked to around 100 degrees for curing otherwise it will create problems to them when they powdercoat.
Please let me know if this is the correct process or not. If not, what would be the best way as an undercoat or primer for sand cast aluminum items.
Bhushan Salujamanufacturer of architectural products - Ahmedabad, Gujarat, India
2005
2005
Zinc in direct contact with aluminium gives strong galvanic corrosion and is to my opinion to be avoided.
Alternatively you can use a non-metallic epoxy primer. This can be a liquid or a powder coating. In case of liquid it should be resistant to temperatures up to 200 °C.
Prior to priming a chemical pretreatment of the aluminium is strongly recommended. This consists usually three steps: alkaline cleaning, deoxidizing and chromating (each step followed by thorough rinsing with clean water). As an environmentally safe alternative for chromating; a pretreatment based on zirconium-fluoride is suitable.
Barry Groeneveld- Nieuwkoop, The Netherlands
It sounds like they know what they want as they have given you some very good detail(more than you would usually get from a customer) as far as the pretreatment requirements. The best way to get into to trouble is to ignore their request or change it without letting them know. Typically aluminum is chromated, but the sandcasting has it's own set of problems like outgassing and rough surface. I would go with what they have requested unless they put a disclaimer in the contract that you can do the pretreat however you please (it doesn't sound to me like they did).
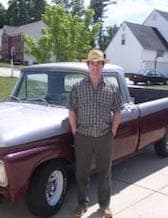
Sheldon Taylor
supply chain electronics
Wake Forest, North Carolina
2005
A. I'm with Sheldon. It sounds like the customer knows exactly what they want. Nothing compares to chromate for pretreatment of aluminum, but furniture may not require robust pretreatment.
Luck & Regards,
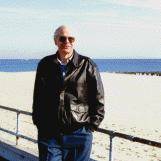
Ted Mooney, P.E.
Striving to live Aloha
(Ted can offer longterm or instant help)
finishing.com - Pine Beach, New Jersey
Q. I have a problem to phosphate the aluminum alloy AA4032. can anybody help me out that what procedure I should adopt?
Muhammad Kazim MahmoodStudent - Islamabad, Punjab, Pakistan
2006
A. You can phosphate aluminum. Its main use is paint prep. It is not a stand alone finish. I have seen it used in a special formulation of iron phosphate as a prep for paint on parts that were made of both iron and aluminum. P.S., EPI / Electrochemical Products Inc. [a finishing.com supporting advertiser] sells two formulations.
James Watts- Navarre, Florida
2006
Q. Sir,
I want to know if the 3 step phosphate process can be used on aluminium parts or not?
also what is the best way of having an effluent treatment plant? please suggest
Process engineer - Goa, India
2006
A. If you are using a multi-metal formula in your phosphate tank you can; check with your chemical supplier. If you are significantly changing the % of steel product to aluminum product you might have to change what you are presently using for something more compatible.
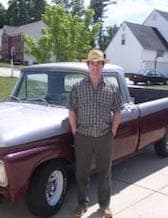
Sheldon Taylor
supply chain electronics
Wake Forest, North Carolina
2006
Aluminum Pretreatment for Aerospace
Q. I am trying to setup a powder coating equipment and trying to understand the best method of pretreating aluminum. Most of my parts are in good shape. I have read over 50 articles suggesting to use Chromate and Phosphate. I was suggested by my supplier to use acetone and a cloth to wipe parts. Then, I was told about Alodine.
Would it be best that I use pure acetone
⇦ on
eBay
or
Amazon
[affil link] Warning! Flammable!
?
Industrial Engineer - Tucson, Arizona, USA
2007
Acetone is a cleaner (of some things), but it is not a pretreatment. For practical reasons aluminum is sometimes phosphated in a "mixed metal" line, but the ideal pretreatment is chromate conversion coating. This can be done with Alodine, which is one brand of chromate conversion coating, but it contains hexavalent chrome and the thrust today is to try to move away from hex chrome. Henkel, the manufacturer of Alodine, offers a TCP (trivalent chrome process), as do other manufacturers.
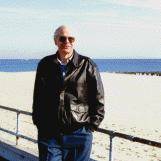
Ted Mooney, P.E.
Striving to live Aloha
(Ted can offer longterm or instant help)
finishing.com - Pine Beach, New Jersey
2007
What is "Tiger Juice" aluminum pretreatment?
Q. Any ideas on the formula of this aluminium pretreatment?
Barry GayIMF HSG - UK
January 24, 2008
A. I've seen that term onlt once in an article on plating of aluminum wheels and I think it has no specific meaning, and was just being used as slang and pejorative for extremely nasty acids like nitric-hydrofluoric.
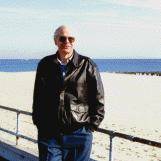
Ted Mooney, P.E.
Striving to live Aloha
(Ted can offer longterm or instant help)
finishing.com - Pine Beach, New Jersey
January 25, 2008
Q. Could a 3 in 1 solution be used as passivation for aluminium parts prior to powder coating?
ashokomaks industries - Mumbai, Maharashtra, India
March 10, 2013
A. Hi, Ashok. We appended your inquiry to a previous thread which answers the question: yes it can be done if the 3 in 1 solution has fluoride in it, but it won't be nearly as good as chromate conversion coating.
Regards,
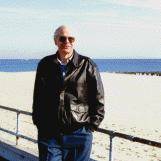
Ted Mooney, P.E.
Striving to live Aloha
(Ted can offer longterm or instant help)
finishing.com - Pine Beach, New Jersey
March 10, 2013
Powder coated aluminium castings bleeding green through coating
Q. Hi, we have received feedback that some of our powder coated castings have started to bleed green through the powder coating. The casted aluminum has been treated with iron phosphate prior to powder coating. Our two assumptions would be either the phosphate or the copper of the aluminum is causing this. The supplier has been instructed right from the start to use chromate conversion, but has ignored this until we found out a few deliveries into the project. Has anyone had similar experiences or knows what could've caused this and why?
Thanks
- Bremen, Germany
March 23, 2015
March 24, 2015
A. Why?:
Because you are using an incompetent coater!
Iron Phosphate pretreatment system on Aluminium may remove some contaminants (grease, oil etc) but that is all it could do and that only if it was a good system.
Your product is compromised.
Your Coater should be held responsible.
Hopefully, your Document trail is intact?
Regards,
Bill
Trainer - Newcastle, NSW Australia
Iron Phosphate vs Chromate pre-treatment Aluminum 6063
August 19, 2016Q. I am a financial consultant and have a client with a manufacturing issue related to powder coating aluminum 6063. I know very little about manufacturing or the pre-treatment process.
The issue this client has is the power coating flakes or bubbles from the edges and the seams after a year or two. This appears to be happening with about 1% of their products. They are using an iron phosphate to pre-treat the aluminum 6063 and received this pre-treatment recommendation from the powder coat paint provider.
There appear to be a great amount of research out there on the proper pre-treatments, but much of it is confusing or conflicting.
1. Will Iron Phosphate cause pitting on the edges and seams? Could this explain why they have bubbles and flaking.
2. Is a dichromate that much better and likely solution to the issue?
3. Any other recommendations or a link to resources that might be helpful?
I simply want to point the client in the right direction and bring in the right resources to help them. Appreciate any help or advice.
research - Orlando, Florida USA
A. Hi. Yes, chromate conversion coating is a much better pretreatment for aluminum than iron phosphate. Your client can use a RoHS-compatible MIL-DTL-5541 [⇦ this spec on DLA] chromate conversion coating.
The only reason the coating supplier would suggest using any phosphate process on aluminum is if they're also processing steel, so that's what they have -- it may be better than nothing.
I don't think the word "cause" quite belongs in the sentence about the powder coating failing at a 1% rate after one or two years. I think the way to look at it is that, to achieve corrosion resistance for 2+ years on 99%+ of the product requires a robust pretreatment and robust powder coating ... and iron phosphate is not a robust pretreatment for aluminum. But coating is complicated, and there's no telling from this distance and with so little data whether something else is being done poorly which even more strongly affects the quality than the lack of chromate conversion coating. Good luck.
Regards,
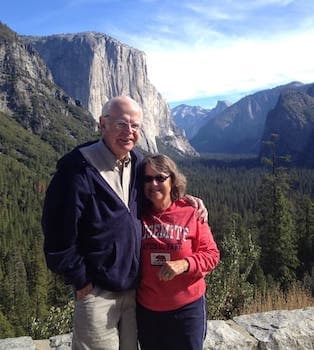
Ted Mooney, P.E. RET
Striving to live Aloha
(Ted can offer longterm or instant help)
finishing.com - Pine Beach, New Jersey
August 2016
A. Also Ted, let's remind him to put the chromate on very thin, down to just slightly iridescent, under heat cured powder coat. If the chromate gel is put down too heavy it will outgas, or explode, right through the powder while curing at high heat.
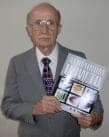
Robert H Probert
Robert H Probert Technical Services

Garner, North Carolina
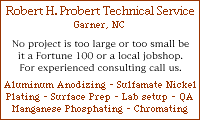
August 19, 2016
September 25, 2018
Q. We are a manufacturer of aluminum enclosures and assemblies. For years we have been using iron phosphate for pre-treatment prior to powder coat. Years ago we used to run cold roll steel products in the same line, but we are 99% aluminum now. I guess we forgot to change or did not know to change.
Is iron phosphate the best for pre-treating aluminum, or what do you recommend?
I ask this not because we have quality, adhesion issues. We do have random aesthetic and adhesion issues, especially in the areas near or at the coast, but very few. I ask this because it is my understanding that aluminum should be pre-treated using a chem film product for optimum adhesion/performance results, especially in products that go into salty environments.
Which process is less costly to operate?
Does anyone know of a white paper that compares the two??
Thanks in advance,
Martin
QA - Anaheim, California USA
by Raj & Ali
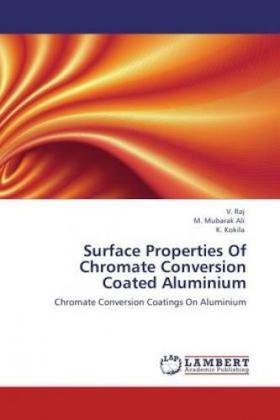
on eBay or Amazon
or AbeBooks
(affil link)
A. Hi Martin. Hopefully a reader will point you to such a white paper. In the meanwhile we appended your question to a thread which discusses the topic, and the fact that chromate conversion (which these days can be hex-chrome free) is greatly superior. Good luck.
Regards,
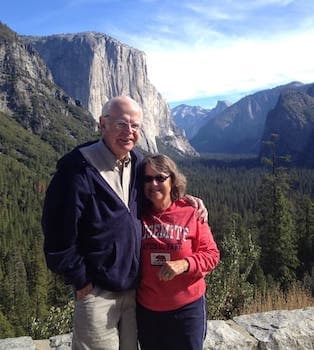
Ted Mooney, P.E. RET
Striving to live Aloha
(Ted can offer longterm or instant help)
finishing.com - Pine Beach, New Jersey
A. Hi Martin,
Iron Phosphate is not a suitable pre-treatment process for Aluminium. The only benefit would be a wash effect from the 1st stage, I have seen the effects of Iron Phosphate used as a pretreatment on architectural aluminium balustrading (erroneously recommended by a powder supplier): it resulted in complete failure and extremely expensive rectification. In Australia we use a Standard AS 3715 for architectural aluminium. It would be worth your while to read a copy.
Hope this helps.
Regards,
Bill
trainer - SALAMANDER BAY NSW Australia
October 3, 2018
![]() |
Q. Thank you for your responses Ted and Bill, I really appreciate it. Manufacturing - Anaheim, California USA October 4, 2018 ---- A. The best prep for powder coat is THIN yellow chromate, stop about slight iridescence; if too heavy the heat of powder coat curing will dehydrate the coating and the paint will peel. The second best, contrary to above letter, is moly based iron phosphate with a chromate seal. The third would be just plain moly base iron phosphate with no seal. ![]() Robert H Probert Robert H Probert Technical Services ![]() Garner, North Carolina ![]() October 5, 2018 |
A. Hi again,
The standard to which I refer is AS 3715 the Australian standard for powdercoating architectural aluminium.
I am sure your USA standards association will produce a similar document. AS 3715 describes a high quality process which satisfies powder manufacturers requirements for access to warranty grade powders. The process specified is a multi stage immersion system:
Stage 1: alkali wash
2: fresh water rinse (fwr)
3: acid etch (hydrofluoric)
4: fwr
5: chromate
6: fwr
7: deionized water rinse
8: halo deionized water rinse
The conductivity of the water running off the product after final rinse must be <25 micro siemens.
Some aluminium fabricators will often use beeswax based cutting lubricants these are largely impervious to alkali washes and if they are detected then some additional cleaning prior to stage 1 may be required -- vapour degrease or MEK wipe are usually effective.
The pretreated work pieces should be dried with warm air and definitely not full cure temperature exposure.
It is also important that clean gloves are used for any handling prior to coating.
Powder quality is another aspect to give some close attention to. Having given a first class preparation it would be a shame to use anything other than an architectural grade powder. These usually employ TGIC resin systems and are not as micro porous as your average run of the mill offering.
I hope this helps.
I would really not take the Iron Phosphate recommendation too seriously unless someone can explain how to grow amorphous Iron Phosphate crystals onto an oxidized Aluminium substrate. Rectifying peeling aluminium on high rise buildings is not cheap or for the faint hearted.
Regards,
Bill
trainer - SALAMANDER BAY NSW Australia
Q, A, or Comment on THIS thread -or- Start a NEW Thread