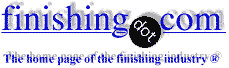
-----
Lasermarking is coming off after passivation
Q. We are laser marking 410SS parts on our YAG [yttrium aluminium garnet] laser machine. The biggest majority of our parts get passivated in a 20% nitric acid, 3% sodium dichromate solution. We do large amount of lasering & passivating different stainless steels. We have one product line that we are having a problem with the lasermarking coming off after passivation. they are run on the same lasermarker & passivated in the same bath as everything else we make. However we not have this problem with ANY other product. I'm wondering if anyone else has ever had this problem,or if you can give me any insight to solving this mystery!
Our production/engineering staff and myself have tried a number of things with no conclusive results. Any input or resources you or your readers can provide will be greatly appreciated.
Tim Connorsorthopaedic instruments - Warsaw, Indiana, USA
2003
A. From our experience in laser-marking of medical instruments we think that passivation in HNO3+CrO3 in some cases cause significant steel etching, especially in the laser marking area. This can happen due to low concentration of sodium dichromate in the solution; too high temperature; depletion of chromium in locations of laser marking.
adv.
There is passivation technology for laser-marked steel 400 series instruments in chromium-free solution that does not etch laser marks.
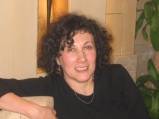
Anna Berkovich
Russamer Lab

Pittsburgh, Pennsylvania
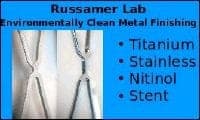
2003
2003
A. When you say that you have one product line that gives this problem, what is unique about this line of products? Alloy source? size (heat generation/dissipation), shape, heat treat, etc. If all of the parts are made from the same grade and source, something else is different in the process. What ever the difference is could be the culprit.
adv.
We have lots of history with passivation of laser marked 410SS with citric acid formulations which give significantly better corrosion resistance than the nitric acid formulations without removal of the mark.
Lee Kremer
Stellar Solutions, Inc.
McHenry, Illinois
A. Tim, stop shooting yourself in the foot. Get rid of that type II bath and switch to type VIII, or citric acid . We switched to type VIII several years ago, got rid of a bunch of testing hassles, and the etching problems on 303, 410, and 416 went away. I've seen some of Lee K's info on citric acid passivation, and it looks very interesting- I'd suggest you at least consider it.

Lee Gearhart
metallurgist - E. Aurora, New York
2003
Laser Mark Settings That Will Withstand Passivation for 465SS
Q. I'm having a hard time trying to figure out settings that will withstand the passivation process on 465SS. I use ASTM A967 nitric 4. Does anyone know of laser marking settings that will work with this passivation process while not making my mark disappear.
Alison Schofieldmetal finisher - woodstock Connecticut
March 26, 2015
Alison,
Yes, that's a large problem throughout the industry. First of all, switching to citric acid passivation will help, but even in citric most laser marks won't hold up for the full amount of time usually recommended for passivation. One way around that is to passivate the part prior to marking, then do a shorter passivation cycle after marking, stopping short of the point where the laser mark starts to be ruined.
Some have told me that running the laser with a tightly focused, high powered beam for multiple quick passes gives the best results. The idea here being to reduce the heating experienced by the metal surface.
There are some other things out there, like using the laser to bond a ceramic powder stuff to the surface rather than the traditional burning the mark into the surface itself. I don't know how well that sort of thing holds up, but I suspect it has potential.
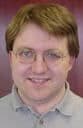
Ray Kremer
Stellar Solutions, Inc.

McHenry, Illinois
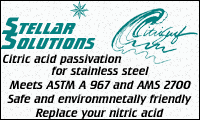
March 31, 2015
Q, A, or Comment on THIS thread -or- Start a NEW Thread