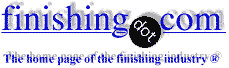
-----
Nickel recovery from wastewater
Q. Dear sir, is there any better method to recycle the Ni from the electroplating waste water? We used to use OH- to recipitate the Nickel, and use H2SO4 to dissolve it into sulphate form, but the purity was not high enough.
Thanks for your prompt reply.
Albert Johnsonmetal recovery - LA, California, USA
2003
A. As always it is a question of economics but if the Ni is worth recovering, then remove it from the waste stream by a cation ion exchanger and regenerate it off with sulfuric acid. Typically you can remove 50 g of Ni per litre of resin which in turn will uses 2 litre of 15 % sulfuric to regenerate it. You will be left with an acidic 25 g/l Ni solution which may be directly usable or you could evaporate it to a higher concentration.
Hamish McWillie- UK
2003
A. The simplest way to recover nickel is the use of a dragout rinse to replace evaporation. A single rinse can often recover over 50% of the nickel chemicals, and a double-dragout recovery rinse can often recover 70-90%.
Of course, you will also recover and concentrate impurities and brightener breakdown products. We recommend using RO or DI water to minimize salt build-up. Recovery at > 90% is further complicated by the significant difference between anode and cathode efficiencies. Nickel dissolves from the anodes more efficiently than it is plated out at the cathodes. This means that at > 90% recovery, the nickel concentration will rise to an unacceptable concentration, and you will have to dump some of the bath.
If you have limited space and cannot install enough rinses to use the dragout recovery method, Reverse Osmosis, Evaporation, and Ion Exchange have all been in use successfully for nickel recovery for many years.
Lyle Kirmanconsultant - Cleveland Heights, Ohio
2003
2003
A. Albert: the method you are using should produce good product if the following criteria are met. I would suggest first experimenting with a small amount of the original waste, from start to finish. Whatever works in the lab can then be duplicated on the whole lot. Make enough to make a little plating bath and run bent cathode panels or Hull Cell ⇦ huh? tests, to prove plating quality, before proceeding. If you can't get it clean enough in the lab, you may as well have it hauled off.
1- The NaOH and H2SO4 must be relatively pure. Not reagent grade but a very good industrial grade. Instead of NaOH, you could use Na2CO3. It's cheaper and cleaner. If you use NaOH, try the liquid variety.
2- Good filtering and rinsing of the nickel hydroxide or nickel carbonate is very important. You must get rid of the sodium sulphate that you've made, plus the other stuff in the original solution. The best filter I've used for this same purpose is one that produced a continuous cake about 3" thick by 24" wide, on a conveyor. Also, it could automatically be put through rinse cycles and produced a large volume. It's been 20 years and I don't remember the name. It was not very expensive.
3- Let us not forget why this material exists in the first place. Most likely, much of it was contaminated with metals, like copper, or organics and was no longer useable. This may be the main source of your problem. There are 2 old, but good, ways to remove these contaminants. In fact, many discarded solutions can be put back into service simply by using one or both treatments.
3a- "Dummying", properly done, can remove Zn, Cu, and Pb. You'll need a piece of sheet steel bent into an accordian-shape (/\/\/\/\)running up and down, to use as a cathode. This will give both high and low current areas. Make it about half as wide and half as tall as the vessel and hang it between nickel anodes. Run it about 2 ASF for a few hours, with agitation.
3b- "Carbon Treatment" removes organics. This can be done in several degrees of strength, depending on what's needed. The mildest is to circulate the solution through a carbon packed filter.
Better still is a 150 degree F Peroxide Carbon Treatment. Add about 2-4 ml of 30% H2O2 plus 10-12 grams of activated carbon, per gallon of solution Stir at 150 degrees for several hours. Allow to settle. Filter off the tops. Filter or discard the bottoms.
Best is the same as the above, except that, at the start, you adjust the pH to 5.2 with nickel carbonate. You then adjust it back after filtering. This will remove Al, trivalent chrome, and phosphate.
I like the nickel carbonate method. It's cheap, fast, and usually reliable.
Chris Owen- Houston, Texas
A. We have been recovering the dragout rinse for 13 years without problems. Use clean (<50 microsiemen) water at the evaporation rate. Save the rinse in a tank off to the side so you can have some stored for Monday morning. Send it through particulate and carbon filters back to the plating tank as needed. If you do not have room for more tanks in the line for counterflow, then consider spray rinsing (several rinses in the same tank). Plan to dummy periodically at low amps. And don't forget to add a membrane to remove any nickel that makes it to the chrome tank.
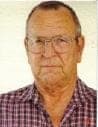
Paul Morkovsky
- Shiner, Texas, USA
2003
November 5, 2010
Dear Sir,
for me the better method to recycle the Ni from the electroplating waste water is the use of a dragout rinse to replace evaporation (natural evaporation of Ni bath is 0,79 gallons/h for 1,20 square yards).
With the recycle of the dragout rinse you can obtain reduced consumption of boric acid and Ni metal.
Before the nickel concentration will rise to an unacceptable concentration you can introduce insoluble anodes (one anode every ten titanium baskets) and you don't have to cut the bath.
- Polcenigo - ITALY
Q. I have a customer who is struggling to remove nickel via ion exchange.
The resin they are using is cationic non chelating resin
They regenerate with 16% NaOH and 12% H2SO4, both in 200 liter intervals.
They have also had a white precipitate form in the resin columns.
Can anyone help?
technical service - walsall uk
October 16, 2014
October 29, 2014
A. Cation exchange resins of the strong acid type are selective for calcium over nickel. The regeneration with 12% sulfuric acid will cause any calcium on the resin to precipitate as calcium sulphate. This is probably the white precipitate that you are seeing.
Using only fully softened water, and/or regeneration with hydrochloric acid will avoid this problem.
consultant - Cleveland Heights, Ohio
Q. Unfortunately the solution they are removing the nickel from is trivalent chrome and chlorides would destroy the anode so they cannot use HCl.
chris kirwan [returning]- walsall uk
October 29, 2014
Q, A, or Comment on THIS thread -or- Start a NEW Thread