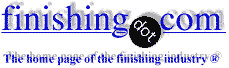
-----
Electroforming of Copper Foil
January 7, 2021
Q. Hello everyone
I am a chemistry student interested in electrochemistry, and I'm working on a hobby project of making electrodeposited copper foil.
To do so, I made a small machine with a rotating steel drum (304 s.s. ; about 10 cm diameter) partially submerged in acidic copper plating bath to electroplate copper on the drum, and peel off the electrodeposited foil (continuously) from the top side of the drum that is out of the bath.
I used a curved sheet of lead as the anode (as it must be dimensionally stable and MMO anodes were too expensive and hard to find for me).
The bath composition and conditions are as follow:
copper sulphate: 240 gr/lit
sulfuric acid: 80 gr/lit
current density: 40 mA/cm2 [4 A/dm2]
temperature: room
anode: lead
anode-cathode distance: 2 cm
agitation: the solution is continuously forced into the space between the anode sheet and cathode drum with a small pump
no additives are used because a matte surface is desirable.
I had my first run today, and the foil comes out perfectly fine in shape and thickness, but my problem is that the foil starts to tarnish (with a green/brownish tint) about a centimeter up the bath level as the drum rotates the foil out.
But it does not tarnish evenly and specific parts of the foil is tarnished more (its place is constant along the length of the foil, so the tarnished area looks like a strip on the foil).
Does anyone have any idea of the reason behind this?
- Illinois chicago
⇩ Related postings, oldest first ⇩
2003
Q. Electroforming At the risk of running long, I will do my best to explain my pursuit, that others may find adequate information, but also that others may see and learn from what we have done so far, in our effort. All of the processes mentioned here are done under safe conditions with proper equipment, and safety training. We do not have the option of going out of house and keep the multitude of R&D; well managed, near by. All references here are public domain. (Please prune the size here as you see fit).
Were building up a multiple layer, selectively plated substrate on a clear plastic backing.
The ultimate goal of the effort is beyond certainty at this point as we assume the result will be constrained by the limitations of the processes we can apply, but the basis is outdoor decorative artwork. We use a copper film substrate and "spray adhere" a clear coat to it, to form a dielectric (insulating) backing.
The copper can then be etched back selectively. The options of vacuum metallising were not found conducive to a "mirror" industry grade 8 reflective surface to build upon and "silvering" by formaldehyde was not within our facility to support. Tin/Chloride/Palladium yielded inadequate adhesion and clear PET film does not etch.
Cold rolled copper foil cannot be used, due to contamination in the copper from the mill rollers, which was revealed upon electropolishing in phosphoric acid.
This led us to attempt electroforming the copper foil.
We used a copper sulphate ⇦ on eBay or Amazon [affil link] bath with Sulfuric acid detailed in the Finishing handbook for semi-bright copper deposition and selected a 7 mil, 302 flat stainless as a mandrel stock, cut 6 inch by 8 inch, to form our part, which is primer and polyol coated on the back side to insulate from plating the back.
The bath is 32 oz./gal CuSO4 and 9 oz/gal concentrated sulfuric acid with electrical grade copper anodes at 2:1 anode to cathode surface area, bagged in polyester and the anode exposure is free standing, constrained behind barriers to avoid over-plating of the edges.
Distance of work to anode ~ 4 inches. Solution is filtered to 5 micron, then dummy plated before plating. We are using a low ripple, voltage regulated power supply, capable of 8 amps - 1.28 VDC - 12 VDC. Bath runs at room temperature at 30 ASF, for approximately 1.5 hours.
The color, leveling, ductility, grain structure and density of the resulting film are more than adequate for our application, so we felt we may be able to avoid chloride, phosphorized anodes, and other organic additives which would likely be beyond our management, given the variables and maintenance needed.
The problem is that the stainless does not maintain a bond with the copper, except around the peripheral where edge plating has mechanically bound the film to remain. I can cut away the outer edge and sacrifice the mandrel to release the film, but the film no longer represents the surface of the mandrel as acid etches the released surface during plating.
As well, skip or porous pin-hole tendencies occur in areas where current density moves from higher at the edges to lower at the center.
The stainless fails to coat after about 4 applications, assuming the surface is becoming passivated. I understand the process calls for passivating the stainless, prior to performing a Wood's nickel strike.
Literature suggests this aids in "detachment". ( I'm detaching just fine, too well). We don't use cyanide strike as we are not adequately prepared to at this point and perhaps don't need to.
The other option calls for using aluminum as a mandrel and dissolving the Al in Sodium Hydroxide. The questions:
1 Will the nickel strike remain with the stainless?
2 Will I need yet another release layer between nickel and copper on a flat, flexible e-form?
3 Will the form parting likely require as drastic as liquid nitrogen to thermally shock them to release?
4 Is aluminum a more forgiving mandrel and does the formed part represent the original surface well?
5 Would aluminum require passivation / release layer first, as may the stainless?
6 Is there a forgiving alkaline strike, that would detach reliably, otherwise.
I'm glad to work my way to the result if others would kindly point me in the right direction. I'm not asking for complete formulations, the basis of the formulation among any critical points to watch for, would be most appreciated. Alternate methods would be an option as well. Sincerely and thank you for the site and the help that it provides.
Mike- Holland, Michigan, USA
2003
Q. I am updating the previous request, if you care to post the update behind the original, for the benefit of those learning.
The nickel strike method was attempted, however the nickel did not remain with the mandrel, assuming perhaps that the mandrel was not well passivated for one. We still seek confirmation as to this option.
The 302 stainless mandrel is now being alkaline cleaned, followed by a micro etch in Hydrochloric acid with Copper sulphate, then rinsed, dried and into the copper bath. The etch has given adequate attachment / seed to allow processing some for now. While the final copper surface is representative of the micro-etch on the mandrel, we are finding that we can polish the result adequately in ortho-phosphoric to produce a "fair", finish from the mandrel surface.
The temporary mandrel backing we use, benefits from the etch as well, which is gray primer, followed by spray polyol.
The bath side surface which forms has been slightly that of coral copper, but extremely fine. Without organic additives, we don't expect to find a great deal more benefit. Reducing the ASF from 30, to between 25-20 has refined this surface even further, to a point where the bath side can be sanded lightly with 1500 wet sandpaper, then electropolished as our "tooth" surface for our clear backing.
Beyond this, lies adjustments to the acid / copper sulphate ratio, anode to cathode ratio and distance between and parallel versus perpendicular variations. While these headaches would mostly be eliminated by a reliable supplier and proprietary bath supplements for leveling and grain refinement, we are not yet properly facilitated to monitor and maintain these constituents. Hence we are pushing the envelope, the hard way to a degree, so as not to generate wasted or exhausted baths and to avoid unnecessary waste management.
We still hunt for tips regarding chloride and phosphorised anodes, but understand this to be a brighter application specifically, not well understood and are uncertain as to grain refinement from either chloride or chloride with phos-anodes. If sulfur is adopted into the resultant film, this may be detrimental to electropolishing as well. We were successful at one time running just chloride at about 50 ppm, but it had a narrow window regarding ppm and the anodes became very fussy concerning polarization.
Mike- Holland, Michigan, USA
![]() |
A. If you are going to electroform, you have to know what your internal stress is. I didn't see any reference to your spiral contractometer. Internal stress is the property that requires most attention. Once you have gained experience, you may rely on cheap tricks or even your eyes for control, but at this point you absolutely need to measure stress. If high, lower the current and raise the acid. Guillermo MarrufoMonterrey, NL, Mexico 2003 A. For good electroforming I would suggest a filtration rate of about 8-10 tank turnovers per hour. Secondly, your copper bath appears to be little more than traditional, so I would not be concerned about that; however, you are using it at a slightly high current density; - I would recommend about 15-25ASF. Your higher cd could contribute to your adhesion problem. Thirdly, copper will not adhere to stainlesss teel because the stainless has a tenacious oxide film over it. This film makes it ideal for electroforming mandrels because it doesn't need any special pretreatments other than a good clean to remove any surface contamination. From your description, I would suggest your copper solution may be slightly tensile - this will jeopardise the interfacial contacts and result in a loss of definition. To make the copper compressive, just add some molasses or Thiourea ⇦ on eBay or Amazon [affil link] . These additives are well documented so there should not be any problem there. If you want to plate the stainless with a nickel strike, it will stick if you give it the correct pretreatment, but very few other nickels will adhere. That is not to say it will not fail with repeated use, so it is only really a temporary fix. Personally I would not use it. However, if you do, you will need to passivate the nickel; this can be done with dipping it in a 1-1.5M sodium metabisuphite bath, although I have also used dichromate with some great effect. This will help release the copper from the nickel. You will not need to use liquid nitrogen. You can use aluminium as a mandrel, as long as it is the correct type. Aluminium can be directly plated, but if you want the deposit to stick (which you don't!), you need a zincate pretreatment before applying a nickel layer. An aluminium mandrel would need very good surface preparation because it too forms a very tenacious metal oxide layer that can cause problems with continuous or fault-free plating. Aluminium mandrels are well known and there is a lot of information about them in the electroforming literature. As far as copper is concerned, you may want to try a pyrophosphate bath instead of the acid copper - this is supposed to be slightly better for electroforming than the acid bath, but I have little real "hands-on" experience of it, so I can only repeat what I have been told. Finally, I too have had problems with skip plating of acid copper and have not got the bottom of it. I do know it is not the bath composition (low acidity can cause this problem) and I suspect it is some sort of contamination, but have no idea what it is. I would be particularly interested in following this thread if anyone has any ideas on why skipping can occur and how to solve it. ![]() Trevor Crichton R&D practical scientist Chesham, Bucks, UK 2003 |
2003
Q. Thank you Gentlemen, for the replies and suggestions. I continue to post in the interest of benefiting those who care to follow this progress and in appreciation of those who have contributed suggestions so far.
The suggestion of pyro-phosphoric is interesting. I have an abundant supply or 75% Ortho-phosphoric and may look at trying to convert it, if it seems feasible. I'm unsure as to the process to convert but it may be high temperature.
We have moved away from the Watt's nickel approach for simplicity, opting to rely on electropolishing to finish the etched surface, representing the mandrel side, since micro-etching has given us traction.
The topic of filtration continues in the foreground here, as we have been batch filtering at 5 micron. I installed a 1 micron filter and the bath-side surface was considerably improved. We are now shopping for a small pump system for a 5 - 10 gallon tank, looking at magnetically coupled or thin film sealed pump, for 10 turns per hour and variable speed to adjust down, capable of 100 psi. A rather pricey effort, but batch filtering is simply not practical at any cost.
A carbon filtration cycle will be done in the next 10 days. I strongly feel that this was an oversight at the time of bath preparation. This is particularly suspect, given that this was only a 99% agricultural grade copper sulphate and the manufacturer could not specify the impurities.
I have no means of determining internal stresses, so trial and error are about the only means I have. I can suggest that the resulting material is slightly "tougher" than cold rolled 110 copper, in terms of scratch resistance, but proves to be very ductile, nonetheless. This may even come out of impurities in the copper buss bar anodes. The physical properties are adequate, but again, I have no way of determining internal stress. I do believe it would be a critical indicator however, likely played upon nucleation and a potential indicator to the seed forming domain, initially. The higher acid, lower ASF will be engaged comparatively, once filtration is on line. The higher acid should provide a more potent ion density among the cathode film, which would suggest better seeding to me and take some stress off of the anodes as well.
As a simple and cheap method of grain refinement, I have added 2.6 ml of 28% HCl to provide some chloride ion, suggesting that among a 4 gallon bath, this hopefully is near the 60 ppm mark, (I hope). Moderate improvement in grain refinement has been seen, however the "screen" or pinhole effect was not eliminated at low ASF and a nature to develop orange-peel appearance at bath-side surface, was seen, (again this may be contamination reacting with HCL). Anode to cathode ratio was increased to 3:1, respectively, to account for non-phos anodes and to lower the ASF distribution on the anodes. The anodes sit behind a single bag, in a shallow bucket to retain gross shed film and constrain lower edge plating.
This process continues to improve at higher ASF. The most recent being run at 90 ASF. I run this bath with a sparger so close to the mandrel, that 3/16 inch bubbles are occasionally seen, bumping the mandrel face and a nearly uniform blanket of bubbles rises directly in front of the flat mandrel. So far, minor grain improvements were seen, moving the cathode to 8 inches from anodes, but ion constraint was lost and edges over-plated, so the distance was returned to 4 inches, while we consider re-testing with a new constraint method. At 90 ASF, the anodes were invited to polarize and became insulative, if the current was raised too quickly, so 60 - 80 ASF is where most of the testing is now focused. Deposition rate has been slightly over a mill per hour.
We have found, with 1500 grit pre-polishing, we are able to electropolish the bath-side surface to the grade #8 reflectivity we sought, other than the labor to manually polish and the impurities that will soon come off with filtration.
The final effort on this original germane bath, will be to try the higher acid ratio and step up the throwing power to see if any measure of leveling is affected. The summation of these efforts will be finally detailed here, following their implementations, for others to view and to comment on or make suggestions to. So long as interest remains, contribution will continue. I again express my appreciation to those who are helping. Your ideas are being tried as quickly as I can implement reasonable and reliable means.
Thank you again.
Mike WilsonDecorative copper - Holland, Michigan, USA
2003
Q. I wanted to address three items Trevor contributed:
1 Can you help define tensile as it applies to the bath or compressive as it applies to copper? I›m familiar with tensile mechanical properties, but as yet have not encountered this expression in bath related.
2 I acquired some Urea crystal and was interested in trying it. I will continue to look into this, having seen it before, but the documentation was brief and abstract, most times. Thank you for the reminder.
3 As far as skip plating has gone on this process, it has had more to do with preparing the mandrel and not damaging the surface in handling, prior to getting into the bath. Many times, cleaning becomes the bigger source of an issue here.
Since I'm presently a micro-etch, it has to do with surface conditions of creating an evenly prepared surface, for me. One thing that helped me was that my R&D; is in a clear glass tank, so I can examine the wetting and seed depositions easily. Otherwise, glass or Lexan windows can be installed, using Teflon gaskets and titanium fasteners, (verify all for reactivity first). It is a phenomenal benefit for troubleshooting.
The other option is to blast a part with low versus high ASF, momentarily and pull the part during seed and look at the seed propagation. This may point to preparation, drag in or ill activation tank preceding. For some reason and contrary to much of what I have read, higher ASF, 60-80, is giving me a more uniform seed deposit, which otherwise below 25 ASF, formed a back door screen, it was so prevalent. Once I had the etch in place, this problem seemed to go away above 25.
I have not attempted high ASF without the etch, which is one area being done tomorrow as well as a severely passivated mandrel without etch. I have the benefit of a perfectly flat, vertical surface, of course. This may change for me with higher acid, lower ASF, given throwing power, as you suggested.
My other references to skip plating have had to do with contamination of oils, lack of wetting and eddy flows occurring from part configurations where shelf testing can many times be an indicator of flow or solids. Horizontal versus vertical speaks of particles settling, etc.
Higher flow rates or bubblers, may cause blushing or other problems, but momentarily may teach something about the nature of the skip or loss of seed that occurs.
I literally cannot give enough sparge flow to the process I'm running.
Mike
Mike Wilsondecorative copper - Holland, MI US
2003
Q. Today's efforts began with the addition of Urea into the bath. Thiourea was not available in house and we wanted to try this effort, prior to the pending carbon filtration, as Urea has a significant difference from "Thiourea".
The chemical expression of Urea is stated as CH4N2O, noting that the compound introduces carbon into the bath as an "organic", something we had expressed avoiding initially, so as to test the limits of a simplistic, low maintenance bath. Thiourea, is also an organic compound.
THIOUREA, CS(NH2)2 (also called THIOCARBAMIDE) is the diamide of thiocarbonic acid that resembles urea but contains sulfur instead of oxygen. As a limited description of its leveling properties, the public domain notes that sulfur behaves in a manner to enhance leveling, which continues to be the direction we pursue on the bath-side of our electroform mandrel. It's exact behavior can be sought by typical web research, beyond this scope. Values to add are also available among research and are not stated here, regarding supplier's considerations otherwise.
Our question, was to seek any benefit of Uria itself, so as to provide a comparison later, with Thiouria.
Remaining at the 60 ASF mark to standardize our tests, we were surprised to see that a manner of leveling did in fact still occur. More surprising was finding that we deposited at 3.3 mil per hour which may be partially attributable to less roughness as we use thickness rather than weight, to measure.
Given the new results, we re-visited mandrel preparation by submitting the 302 stainless to a 2 hour soak in 30% v/v Nitric acid, to attain passivation, which was clearly evident in surface image, following. The approach was to test if mandrel adhesion would be attainable on a chromium enriched surface and if lower ASF would allow seeding and nucleation, among the recent changes to the bath. It did not. Neither low or high ASF was improved and interfacial attachment still failed, as before. We have parked the passivation approach, not wanting to proceed to pre-coating and live entry, or cyanide strike processes, relying on Chloride / CuSO4 etch only.
The effort did however reveal that air flow was involved in most of the pin hole formation we witnessed previously. Assumption was that larger, 3/16 inch diameter bubbles from a sparge bar, moved greater flow than fine bubbles. However, we continued to note that areas lacking bubble contact, even at the surface, were plating with a tendency to pin hole. We replaced the sparge with a fine polymer diffuser which created a walled torrent of very fine bubbles and positioned it to literally "scrub" the vertical surface during plating. The effects can only be given justice by seeing first hand. Pinholes during seeding were eliminated completely as either small particles or stubborn air bubbles, which can no longer remain attached, resulting from increased turbulence, (note that agitating the part during plate, did not offer this benefit). Even the solid particle ratio of contamination in the film was reduced by over 400% and the best description of the surface has gone to a very fine, smooth, satin.
Cycling twice through with light mechanical polish, followed by electropolish, resulted in a mirror surface with a golden / orange color, clarified well enough to depict even the smallest facial features at one foot distance, in typical room lighting. Chloride and Urea will be stepped up 10% each tomorrow, ASF lowered to 30 and an additional batch filter processed, to begin the first production parts to see if photo sensitive mask will adhere at this polish level. Higher acid level will be tested after these, to see if higher throw will benefit seed and nucleation, then this bath will run as a comparison to an identical bath with a typical commercial additives package, to look at long term total benefits of both and an accurate assessment of overall cost and quality impacts for either, given the particulars of this product. The end result will be decorative, high luster copper, with multiple plated coatings and possibly some applications in RF, high frequency applications.
Mike WilsonDecorative copper - Holland, Michigan, USA
A. Tensile stress will cause the depositing metal to "pull away" from the mandrel whilst compressive stress will make the depositing metal adhere to the mandrel. This is manifested by tensile deposits bending towards the anode and compressive away from it. Acid copper is usually assumed to have a tensile stress of between 100 and 1400 lb/in2, whilst the addition of Thiourea ⇦ on eBay or Amazon [affil link] and molasses with decrease that to a compressive stress of up to -4,000 to-15,000 lb/in2. Cyanide copper is tensile to the tune of 6,400-9,900 lb/in2. Fluoborate copper is supposed to be near neutral, but I have little experience of it. I recall reading somewhere that the addition of urea is not a good idea for copper baths and that the addition of saccharin to acid baths is definitely not a good move as it breaks down in the acid and makes the bath foam. However, other sulfur containing compounds such as thiourea do impart a semi-bright quality to the copper and help relieve the stress.
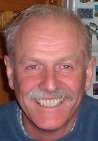
Trevor Crichton
R&D practical scientist
Chesham, Bucks, UK
2003
I really enjoyed reading this. good luck.
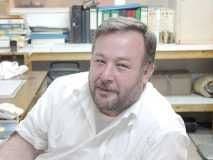
Khair Shishani
aircraft maintenance - Al Ain, UAE
2004
April 27, 2012
Q. Hello,
I want to plate copper on titanium but intentionally WITH BAD ADHESION.
Most of topics here deal with obtaining adhesive copper deposit but that is not my goal.
I want to be able to strip the copper off the cathode.
My cathode would be made of smooth titanium grade 1 and the electrorefining process will run at low current density (100 A/m). I use standard electrolyte, 45 g/L Cu, Thiourea
⇦ on
eBay
or
Amazon [affil link] , chloride ions, which I used successfully on copper cathode blank.
Copper deposition will happen? Will it be stripped off easily?
Thanks in advance,
Metalurgista - Bogota, Colombia
A. Hi Pedro.
We appended your inquiry to a thread which partially answers it. I think you will be better off plating onto stainless steel, which is very widely done, and if sticking occurs it can be prevented with a chromic acid dip or possibly egg albumin. A literature search will provide case histories I think.
Regards,
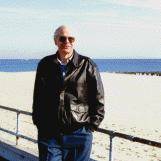
Ted Mooney, P.E.
Striving to live Aloha
(Ted is available for instant or longterm help)
finishing.com - Pine Beach, New Jersey
April 27, 2012
Q, A, or Comment on THIS thread -or- Start a NEW Thread