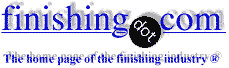
-----
Teflon coating on metal surface
I'm currently working on designing a automated roll-up machine for fiberglass wool. The mandrels we used are either aluminum or stainless steel. The tests that I have done managed to roll up onto the heated mandrel (stainless steel at approximately 310 °C). The problem is, we have been unable to remove the fiberglass wool from the mandrel. I require advice in regards to having an alternative surface such as using Teflon coating or different machine surface to remove the fiberglass wool from the mandrel after being cooked by the heated mandrel for 2 minutes. With the Teflon coating, I would be concerned that the low coefficient of friction might prevent the wool from rolling up. Please advise if there are any other alternative on the surface of the mandrel in order to remove the fiberglass wool.
Danny Tangas, combustion and design - Knoxfield, Victoria, Australia
2003
Hi Danny Tan,
At a temperature of 310 °C you will get big trouble due to decomposition of Teflon. (PTFE decomposition begins at
220°C and causes corrosion and toxic gases.)
I suggest you to try a hard chrome plated surface.
This should work. Chrome is not so much anti adhesive like Teflon, but it comes close to it. The surface energy of Teflon is between 10 and 20 mJ/m2, steel is about 100mJ/m2 (as I know) and Chromium-oxide is about 50 mJ/m2.
Best regards,
Michael HekliSwitzerland
2003
Should you decide to chrome plate your mandrel, it would help to texture or satinize it. Another possibility worth exploring would be coating the mandrel surface with thermosprayed stuff. Less conductivity that chrome but also good when anti-stick properties are seek. Chromium oxide or a blend of a carbide plus a cobalt binder seem to fit the purpose. Carbides and the different binders have better heat conductivity than ceramics. Highest quality of coating will be produced by plasma spray for ceramics or HVOF for the carbides. Surface can be left as sprayed for maximum grip or given a coarse ground for a better finish without compromising the grip.
Guillermo MarrufoMonterrey, NL, Mexico
2003
Q, A, or Comment on THIS thread -or- Start a NEW Thread