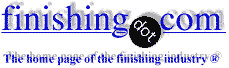
-----
Copper/Nickel Plating Delamination
Q. Hello to All,
We are a metal finishing job shop and I have a situation which has been giving me quite a headache. We have CRS steel(sheet metal) parts which require a copper/nickel finish. The problem is that from time to time the copper/nickel delaminates from the substrate.
Here are some of the specifics.
1) Parts are cleaned in alkaline soap cleaner.
2) Electro-cleaned (reverse current)
3) Multiple Di water rinses.
4) HCl activation (fresh 50%)
5) Multiple Di water rinses.
6) Non-Cyanide alkaline copper; approximately .00015"
7) Multiple Di water rinses.
8) Bright Ni; approximately .0002"
We have eliminated the possibility of copper immersion by using only stainless fixtures and fresh acid for activation. All of the chemistries are maintained by our lab and are well within operating standards. I don't believe it is a matter of preparation or cleanliness as a great amount of time and energy is spent insuring the parts are cleaned thoroughly.
Any suggestions would be greatly appreciated.
Metal Finishing - Santa Cruz, California
2003
A. My first thought is that you are getting an immersion deposit of copper on the CRS. The reason why cyanide copper is usually recommended for steel is exactly to prevent this happening. However, it can also be minimized by using pyrophosphate copper if you are careful. Other coppers are not as good and you will run the risk of immersion deposits. These too can be minimized by using live entry of the work piece into the copper bath, but it is no certainty it will stop the problem. To be on the safe side, I would suggest live entry with cyanide copper (assuming you are permitted to use cyanides). You may want to use a ramped current if your carrier is a bit slow and/or your sheets are large. It is also possible that you are developing localized rust spots on the steel after you have given it the extensive pretreatment and rinsings. This can occur of you leave the work piece too long to drain before going into the copper or if you have difficult to drain areas (I don't think you will have these on sheets!). Is it possible that the CRS has inclusions of tramp elements or impurities - check the spec for the sheets. If there are impurities, these could result in poor adhesion, especially in non-cyanide copper.
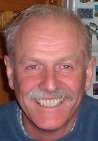
Trevor Crichton
R&D practical scientist
Chesham, Bucks, UK
2003
A. One thing you're not providing is information on the rinses between activation and Cu plate. It is entirely possible to deactivate the substrate during the rinse cycle.
If the problem seems to be sporadic, it may indicate problems with the DI water; you might want to check for a correlation between peeling and replace/regen of the DI system.
A final thing I have run against is seasonal changes in rinse water temperature, but I would doubt it in this case.
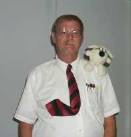
James Totter, CEF
- Tallahassee, Florida
2003
A. You don't mention it but the use of a dilute strike should be considered. If you are using a pyrophosphate bath you should analyze for excess of orthophosphite in the bath.
Also, organics, lead or chromium might affect adhesion. Other metallics are of less concern.
Good luck.
Monterrey, NL, Mexico
2003
Delamination between Copper and Nickel due to bath contamination?
November 28, 2013Q. Please to advise in this situation: I work in an automotive factory and recently we have had a big issue with delamination of chromed parts (plastic ABS). Main reason we received was that 'local delamination between the semi-bright nickel and the matt nickel layer.
The semi-bright nickel layer was locally passivated. On a passivated nickel layer, the next layer cannot be plated
in a proper way. There is no adhesion.
The cause of the passivation is an excessive contamination of the rinsing baths by carryover of process.
chemicals. The bubbles appear right after the galvanic process'. We also received as answer that this is a normal thing to appear in the galvanic process and something like this cannot be controlled.
Solution: The cleanliness of the rinsing bath is checked.
The maintenance cycle for the rinse is revised.
But I am not sure this is the right think to do. So can you please advice what can be done?
Many thanks!
Process Engineer - Germany
Q. Hello,
Can someone please advise if delamination between Cu and Ni in plastic plating can appear due passivation of Ni caused by an excessive contamination of the rinsing baths by carryover of process chemicals. The delamination appear right after the galvanic process? Can this situation and root cause have as solution: The cleanliness of the rinsing bath to be checked.The maintenance cycle for the rinse to be revised.
is delamination something normal to galvanic process?I mean is there no way to be able to control?
please advise what can be done in order to avoid? Or, can there be still another cause to passivation?
Many Thanks!
Erryca Strauss
- Germany
November 28, 2013
A. Erryca,
Yes, your idea makes sense. Another thing to look at is process control and be sure the parts aren't drying between nickel layers. It would be good to inspect the process and see how the rinsing is performed. If a lot of warm air or gasses are blown on the parts or if the rinsing is very slow or rastered or if the parts have to wait to be rinsed, that gives them a little time to slightly dry. As an extreme example: There was a company who was plating nickel in one building and then moving the parts to another building for a top layer and they had all kind of trouble due to the parts drying during the transportation, even though it was a very short distance. Once they stopped moving the parts about and processed them very quickly yet thoroughly, the problem went away. I think you're on the right track and will solve the problem!
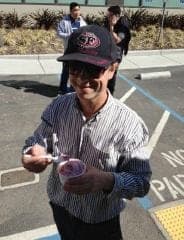
Blake Kneedler
Feather Hollow Eng. - Stockton, California
First of two simultaneous responses -- December 4, 2013
A. Hello Erryca,
First, I will address the first question you had with poor adhesion of the Matte Ni on semi bright Ni. The main rule of thumb is that you want to go into the final Ni plate as soon as possible, and go in with live current(within a minute after the first Ni plate). The biggest problem I have seen in Ni plating is that the plated surface is allowed to become passive. I am a firm believer in using a good Ni activator to keep that surface active. Dirty and inadequate rinsing can also cause you this problem. You also want to keep the surface of the Cu active as well and watch the cleanliness of your rinses.
- Malone, New York, USA
Second of two simultaneous responses -- December 5, 2013
Q, A, or Comment on THIS thread -or- Start a NEW Thread