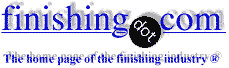
-----
Protective coatings for cast feet on postal boxes
I need some help with corrosion protective coatings for castings. The feet and a few other parts on the USPS standard blue collection box are currently cast (using ferritic malleable iron, i.a.w. ASTM A47
[affil. link], Grade 35018 or 32510, although we are likely going to switch to ductile iron) followed by electrodeposited zinc (IAW ASTM B633, SC3 Type II) before priming and painting. The feet are subject to more aggressive corrosion and occasional replacement, especially in northern climes, and I would like to make sure that we are properly specifying the most cost effective system.
1. We have previously specified electrodeposited zinc IAW ASTM B633, SC 2, Type II; however, we are trying to eliminate the requirement for heavy metals such as chromium. Do you know how well a Type IV finish (phosphate conversion coating) would work for the SC 2 service condition instead of the chromate conversion coatings recommended for Types II and III?
2. Also, are you familiar with ASTM B320, Standard Practice for Preparation of Iron Castings for Electroplating? If so, do people usually specify that parts are cleaned IAW this spec prior to zinc plating? Also, is there likely to be any need for a pre-plating strike prior to zinc electroplating, as described in paragraph 10.1? If so, what would you recommend for ductile iron castings?
Thanks,
United States Postal Service - Merrifield, Virginia
2003
2003
Sir,
The best route to consider:
1) Alkaline zinc - iron Plate to 25 - 30 microns after pre cleaning.
2) Rinse well.. ......continue wet to ED coating.....
3) Coat in ED paint to 20- 25 microns
4) Bake at 140 to 160 Centigrade for 25 to 30 minutes for full cross linking and cure. Cool at room temp.
This system should surpass 850 hours and touch 1000 hrs in a 5% neutral Salt spray test which should roughly translate to 5-7 years service life.Minimum.
Regards
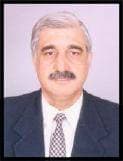
Asif Nurie [deceased]
- New Delhi, India
With deep regret we sadly advise that Asif passed away on Jan 24, 2016
What is the ED coating system you reference? Is this a dry powder formulation?
Ted BellingerUnited States Postal Service - Merrifield, Virginia
2003
While we await Mr. Nurie's return to the site to see your follow-up question, I believe 'ED' stands for 'electrodeposition', i.e., electrocoating, electropainting, electrophoretic, e-coat. The stuff the OEM's prime automobile bodies with.
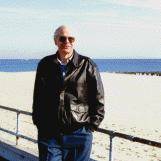
Ted Mooney, P.E.
Striving to live Aloha
(Ted is available for instant or longterm help)
finishing.com - Pine Beach, New Jersey
2003
Just a cautionary note..there is NO correlation between hours in a salt spray test and actual service life.
Cynthia L. Meade- Sylvania, Ohio, USA
2003
2003
Thanks to the previous responders. By way of background, I do understand all too well that tests like ASTM
ASTM B117, ASTM
ASTM G85,
SAE J1563,
SAE J1960,
SAE J1976,
SAE J2020, and others are simply crude approximations of actual service life performance. We conduct our own, in-house tests IAW ASTM B117 and SAE J19601960 as a means to provide some quantifiable and repeatable test of a vendor‹s compliance with our product specifications or manufacturing requirements. One thing we do not do is our own manufacturing. Our products are either "build to print" or "build to spec," so it is very important that we effectively and clearly communicate as much process detail as is required to let manufacturers meet our requirements.
What I really need help with are some specific questions regarding electrodeposited zinc on castings. Does anybody have the experience, as a specifier or as a coater, to answer the two questions I started with concerning phosphate conversion coatings on electrodeposited zinc and preparing iron castings for electrodeposited zinc coatings? Are there any castings people out there with experience specifying zinc coatings, especially on ductile iron? Are there any zinc coaters out there who can tell me how buyers have typically specified this work?
Thanks again very much to all who try to help.
United States Postal Service - Merrifield, Virginia
Dear Mr Nurie,
Have you known that CED can be done on zinc iron or did you want to phosphate over the zinc iron?
anxiously,
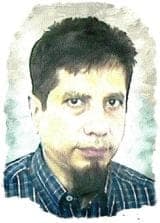
Khozem Vahaanwala
Saify Ind

Bengaluru, Karnataka, India
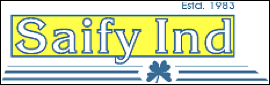
2003
Q, A, or Comment on THIS thread -or- Start a NEW Thread