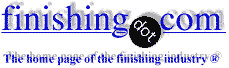
-----
Nickel hardness problem - too hard! (sulphamate type)
How can I reduce/control HV values obtained from a nickel sulphamate plating solution?
The solution is less than 6 months old, and HV values have steadily increased from 220 to 280. We are aiming for a maximum hardness of
300. Tank filtration and temperature control appears to be working as designed.
The solution has required very little chemical additions to maintain it within specified composition limits, but this is probably due to the limited amount of work the tank has had to do.
Any ideas/suggestions would be greatly appreciated.
Regards Chris
Chris perrettAerospace - Cardiff, Wales, UK
2003
First of two simultaneous responses --
Give operating conditions and bath makeup.
Russell Richter- Danbury, Connecticut, USA
2003
Second of two simultaneous responses --
Dummy plating (electrolytic purification) is recommended to remove and keep metallic impurities, that can cause increased hardness, out of the solution. 5 Amps/sqf. using a corrugated anode is usual. the corrugations (90 degrees 3") cause a gradation of current density from about 2 to 10 ASF,thus covering the CD for removal of most metals)Carbon treatment or continuous carbon filtration will keep organic contamination from building. A very important consideration is that there is a sufficiently large anode area of sulphuyr-depolarized anodes is available. Polarized anodes)due to excess anode current density results in divalent sulfur entering the solution causing hardness increases. It is difficult to impossible to remove sulfur from the solution.
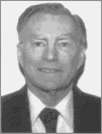
Don Baudrand
Consultant - Poulsbo, Washington
(Don is co-author of "Plating on Plastics" [on Amazon or AbeBooks affil links]
and "Plating ABS Plastics" [on Amazon or eBay or AbeBooks affil links])
2003
Chris,
All the answer is right, but if you plate with a low current density also the nickel deposit being harder in vickers value.
Regards,
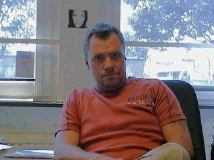
Anders Sundman
4th Generation Surface Engineering
Consultant - Arvika,
Sweden
2003
Removing organic contaminants, and keeping metallic impurities such as iron, copper, lead, etc., to a minimum should able to control your tensile stress value of your bath.
Monitoring stress value within the specified limit provided by your customer/manufacturer should give you better handle on hardness of deposit.
- Miami, Florida
2003
Your first job must be to find out why the hardness is increasing. This can be caused by a build up of impurities or contamination. Make sure that all your rinsing is as good as possible, eliminating any drag-in. Secondly make sure nothing is falling into the tank. Thirdly, check your anodes - make sure they are sulfur depolarised and are dissolving correctly. Check the electrolyte by a Hull Cell ⇦ huh? and check for impurities. Once you have identified and sorted out the causes of increased hardness, you have the option of dumping the tank and starting again, or trying to recover it - your best route will depend on the impurities. The advice above is good for much of the possible impurity, but if it is an organic problem you will have to do things like carbon treat the tank, oxidise the organic with hydrogen peroxide etc. Not all organics, including NTS, can be removed from the bath - if you have used NTS, you must dump the tank and start again. Check the temperature and make sure the sulphamate bath does not exceed 70 C, otherwise the sulphamate will break down to sulphate and ammonium ions, causing all sorts of problems.
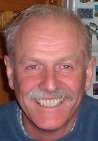
Trevor Crichton
R&D practical scientist
Chesham, Bucks, UK
2003
Q, A, or Comment on THIS thread -or- Start a NEW Thread