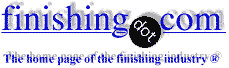
-----
German salt spray results are different / not comparable to Asian results
Q. We are the second largest supplier of bicycle components in the world. In our factory, we produce internal gears hubs. We are trying to replace expensive parts from European suppliers with parts from Asia. My problem is, that the results from the salt spray tests made at our facility differ very much from those of our suppliers. We all work according to the ISO 9227.
Zinc plated parts, that reach 96 hours without red rust in our Asian factory are rusty after 24 hours in our test chamber.
What can I do to compare the different tests properly? How can I adjust the two machines, so that I get comparable results?
Regards,
Oliver Klamann-Rodegrobicycle parts mfgr. - Schweinfurt, Bayern, Germany
2003
A. Sometimes we may read into a poem a theme that the poet didn't put there, so I apologize that I find your letter funny in a way that you don't, Oliver. Sorry!
Those Asian salt spray cabinets which can deliver a 96-hour salt spray rating to parts that are unable to muster even 24 hours in a European chamber ought to sell like hotcakes! Dozens of readers of this letter will want to buy one this week alone :-)
Seriously, the only option seems to be to send an American or European cabinet, salt solution, specs, installation technician, and test team to Asia and see if the parts still last 96 hours under those conditions. Fat chance. Because the fact is, these Asian parts are unsatisfactory, and you mustn't allow yourself be talked into thinking otherwise! The last thing in the world you want to do is make an "adjustment" to your salt spray chamber so it will pass unsatisfactory parts because the purpose of the testing is to detect if something has gone south in your zinc plating process cycle -- and it has.
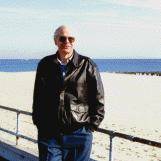
Ted Mooney, P.E.
Striving to live Aloha
(Ted can offer longterm or instant help)
finishing.com - Pine Beach, New Jersey
2003
A. Hi Oliver,
It is not easy to correlate the results between different salt spray cabinets. I am assuming that you have checked the records for both cabinets and they are within spec. Your best bet is to run some kind of standard part whose salt spray performance has been verified.
Run the standard side-by-side with your test parts. You can run the same side-by-side test in both test cabinets and then compare the results. You should be able to figure out which cabinet is giving you reliable results.
- Naperville, Illinois
2003
A. Go to Asia. Sorry Ted I could not resist
Jon Quirt- Minneapolis, Minnesota
2003
A. ISO 9227 includes controls for verifying the conditions within the chamber. In addition to collection rates, pH, etc. you can use steel or zinc coupons to measure the corrosion rate. If the SAME type of samples are passing in one chamber and failing in another, it could be the chamber. If you are testing different suppliers, different materials, you will get different results.
Cynthia L. Meade- Sylvania, Ohio, USA
2003
In my earlier response I tried to imply something without actually saying it. Since some didn't pick up on it, and George and Cynthia read things differently, I guess I should say it outright: I think you should consider the possible need to check the veracity of the test records that showed no rust after 96 hours. Best of luck.
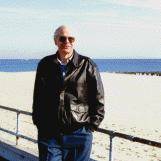
Ted Mooney, P.E.
Striving to live Aloha
(Ted can offer longterm or instant help)
finishing.com - Pine Beach, New Jersey
2003
Salt spray chamber isn't working: 240 hours has no effect on acid zinc plating
Q. Salt spray chamber does not give complete result from testing jobs. Acid zinc plating component after 240 hours, no effect, why? SST chamber all parameters are okay (sol'n concentration, pH, air pressure, fog collection, etc.)
Kiran Mahajan- Pune, Maharastra, India
July 23, 2014
A. Hi Kiran. I see only two possibilities: either the chamber is not working (perhaps no salt spray when the cover is closed and you're not looking), or the parts have a lacquer or clearcoat on them which is delivering good corrosion resistance.
Regards,
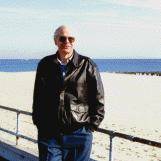
Ted Mooney, P.E.
Striving to live Aloha
(Ted can offer longterm or instant help)
finishing.com - Pine Beach, New Jersey
July 2014
Q, A, or Comment on THIS thread -or- Start a NEW Thread