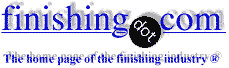
-----
Help needed on metal fillers
2003
Hi
I am a student in Australia making a chair out of 2 inch , 2mm wall thickness mild steel tubing. I have tig welded the pipes together and there are some puddles that need to be filled in. I will paint the whole chair after I have fixed up the puddles. Can any one tell me the wright product to use to fill these puddles (around 2mm max) and how I should go about finishing the job.
Thank you,
Jim C. [last name deleted for privacy by Editor]- Sydney, NSW, Australia
2003
It's a little late for this go 'round, but for next time what you should have done was have a draftsman make a projection of the intersection of these curved surfaces, and cut the end of the pipe to the correct shape to properly intersect the other pipe :-)
Drafting books like French's "Engineering Drawing" describe how to do this under the topic "Intersection of two cylinders".
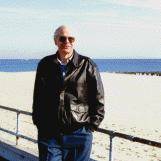
Ted Mooney, P.E.
Striving to live Aloha
(Ted can offer longterm or instant help)
finishing.com - Pine Beach, New Jersey
2003
Dear Jim,
Assuming you're still looking for an answer.... You stated that you used mild steel tubing and have already done TIG welding. I'm presuming that you used a filler wire for that. The gaps that you're talking about (puddles?) can be filled with the same material.
Typical fillers are ER70-S2 if I recall correctly. As Ted mentioned, it's better to have the joint properly prepared ahead of time. Another option to a fancy layout is to cut the tubing to approximately the right shape, then test-fit them together. Build up any gaps with TIG welding onto the ends of the tubing attachment
_before_ you start the assembly welding.
A proper weld will have the cross section of the weld (not the same as the diagonal face of the fillet) equal to the cross section of the members being joined. Piling on extra weld metal beyond this will only increase the frozen-in shrinkage stresses and make things weaker. A smooth transition between the tubing > weld > other tubing is also good for strength and endurance.
I hope that this helps.
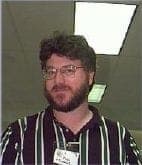
Paul Tibbals, P.E.
gas & electric
San Ramon, California, USA
(My opinions are not related to nor a statement of my employer's)
G'DAy,
Considering you have gotten this far without the help of one of the most informative texts of "Intersection of two Cylinders", I am sure that if you decided to replicate your metallic frame work, then this may be the way to standardize that. For now you have to be sure that the framework will actually be able to take human load bearing weight. The project you have undertaken appears to be one for the HSC. Am I correct?
TIG welding is a pretty adventurous visual display of welding...if the joints are to be seen. Assuming that the entire curved structure will be "hidden" by a powder coating finish or perhaps chromed finish as I think may be the case here, then particular attention has to be applied to finishing the welds as finely as possible. Chrome because it is a highly reflective surface, will magnify the surface it is applied too. The puddles you are experiencing are a pain in doing tubing and even 2mm wall sections are not easy. Did you counter purge the tubing internally as you progressively welded each join. You may have internal oxidation that tends to bubble to the surface. You may have gases trying to escape while actually tying to fill those pools....they look allot "like steel bubbles".
The only thing I can think of is to overfill the pools quickly when you start the weld pool and grind or file off the overfilled weld. Welding & finish...a good weld finish is down to mastering technique...do that and the result becomes second nature after applying the fabrication techniques of "Intersection of two Cylinders"....my technique is called "fish mouthing".
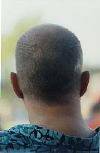
Michael Hein
- Sydney, NSW, Australia
2003
2003
Hi,
The problem when you put the pieces together you get a gap. How to solve that is a process called coping. You can buy a machine that will cope the ends of the pipe to fit the diameter perfectly, they use this process to build roll cages for cars.
Hence I use the process to build my product as well. This eliminates having to fill gaps, because there are none, wonderful hey, and your chairs will look better as well.
Good luck Shawn
Shawn Fortier- Edmonton, Alberta, Canada
Q, A, or Comment on THIS thread -or- Start a NEW Thread