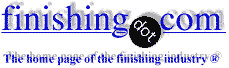
-----
Hydrogen de-embrittlement cycle for fasteners
Q. We buy fasteners of 10.9 & 12.9 class from our vendors. These fasteners are zinc plated. We are facing a problem of delayed failure of these bolts. Our vendors are following hydrogen de-embrittlement cycle as per IS1367 Part 11. In spite of this we are facing bolt failures problem. We would like to know whether any other standard or alternate process is available to overcome this problem of hydrogen de-embrittlement. We also would like to know whether there is any kind of testing/inspection available to test fasteners for hydrogen embrittlement relief treatment.
Regards,
V.GANESH- Bangalore, Karnataka, India
2003
A. Typical approach of platers that do not know the difference or do not care is to pickle the parts in acid for far too long because it makes their life easier. If 1 minute in the acid will not work, then they need to be precleaned better. This is supposed to be an activation step, not a pickle. Next is the common practice of waiting until you have a full load for the oven before baking. They need to get into the oven (with the heat on) as soon as possible. The bake cycle will remove a bit of the hydrogen, but can not really get to deep attack from setting around all day.You will have far less problems if they will do the above. When a current bake cycle does not work, extend the bake time. Also thermocouple the middle of the load in the oven. It can take hours for the middle to reach full temp. There is equipment for testing hydrogen embrittlement in a bolt, but it is very expensive and requires tender loving care in its operation. Notch bar testing will help a lot, if it is handled exactly the same as the bolts.
James Watts- Navarre, Florida
by Polyanskiy & Belyaev
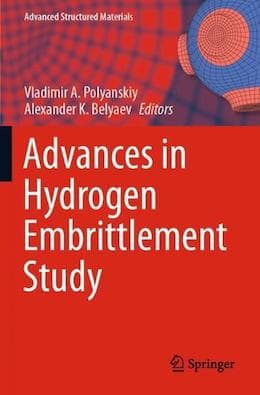
on eBay or Amazon
or AbeBooks
(affil link)
A. James Watts provided you with some excellent tips for better control of the plating process. I wanted to add that grade 12.9 fasteners are extremely susceptible to embrittlement and stress corrosion cracking, which is the reason that they are not used in the automotive industry. Also, there are a number of standards available on this subject-- how to reduce the susceptibility, embrittlement relief procedures, tests for embrittlement, etc. ASTM has a great publication with many of them compiled together with other industry standards. The publication is called Mechanical Hydrogen Embrittlement Methods for the EVALUATION and CONTROL of FASTENERS.
Toby Padfield- Michigan
A. You might want to look into having your fasteners Mechanically plated. This process is free from hydrogen embrittlement. Another advantage of mechanical plating is that you can vary the thickness of the coating, any where from 5 micron to 50 microns.
Simon Cook- Melbourne, Victoria, Australia
Q. The original question states that there is a problem with a delayed failure of these bolts. Is it one or two bolts in a 'batch' or is it the whole batch that fails after some time? If the first, How can one test for HE if it's only one or two, that are going to fail? Also, What are the distinctive features of a HE fracture?
Bob Howell- Toronto, Ontario, Canada
2004
Q. We need a simple test for checking the components are hydrogen de-ebrittlement has been carried out or not.
Please reply.
manufacturing of auto components - Coimbatore, TamilNadu, India
2005
A. Sustained load test as ASTM F606 is a good test to prove the proneness of hydrogen embrittlement failure at fastener level. Sample size to be determined based on the batch size undergoing the surface treatment. Also if the UTS is more than 1350 MPa it is better to go with vacuum deposition techniques rather that plating.
Thomas Kurian- Trivandrum
Q. Similar problem is being traced out at our end.
We are doing Zinc (Green) passivation on the Class 12.9 bolts.
2 of such cases are found during in-house assembly.
My question is how we can trace that the bolts are properly de embrittled or not?
What is the easy method for ensuring this.
- Pune, India
October 3, 2008
A. Dear Ganesh!
Hydrogen embrittlement chances in >10.9 grade fasteners are very high due to acid treatment while plating process.
You can reduce the hydrogen embrittlement severity by processing the fasteners at 200 °C. for 4 hrs within 1 hr of plating process completion.
You can test the components by dipping in liquid paraffin at 180 °C. Bubbles coming out from components shows No/ineffective hydrogen de-embrittlement.
- Hosur, Tamilnadu, India
June 23, 2012
Paraffin test for hydrogen embrittlement
Q. Dear Mr Amit, or all,
I am facing similar problem in 10.9 grade studs,
Paraffin test -- is it a proven one or is it said in any standards?
If so, is paraffin test to be done before plating, or after plating, or after passivation (adding brightness to the fastener?
Kindly explain.
- Chennai, tamilandu, INDIA
August 17, 2014
September 9, 2014
A. Greetings! You would find the thread starting at letter 1216 on this great website to be instructive. Regarding the paraffin test, I know of no standardized procedure for this test. In my humble opinion, the reason that I have never seen one is that the test does not have any predictive value with respect to hydrogen embrittlement. There is a similarly undocumented test that consists of immersing the article in hot silicone. I don't think it works, either.
And why not? Because what you are seeing as outgassing does not and cannot embrittle the part. It's gone. Porous deposits such as mechanical plating and phosphating will outgas; that's why they are hydrogen-embrittlement-free.
Many experts in hydrogen embrittlement feel that it is monomolecular hydrogen and not hydrogen gas (as seen in the paraffin test) that causes hydrogen embrittlement by reacting with the alloy at the grain boundaries.
If you want a test that really works to see if the parts are embrittled, put a reasonable sized sample of parts under load (75% - 85%). If they break within 48 hours it is probably hydrogen embrittlement. To be sure, look at the fracture face under 500 - 800 x magnification; if the fracture face has a "rock candy" aspect it is certainly hydrogen embrittlement.
Keep in mind that ASTM B850-98 sets forth the position that baking reduces the risk of hydrogen embrittlement. Baking does not eliminate the risk. But this specification does have recommended baking schedules for those who are comfortable with the inherent risk.
If you want a process that will not embrittle the articles, you should be using phos and oil, or, if you need sacrificial protection, mechanical plating (as Simon Cook says), or (at a higher cost) dip-spin zinc-rich coatings, which these days are often applied over a base of dry zinc phosphate.
In my humble opinion, all fasteners with a Rockwell 'C' hardness above 32 should be finished with a hydrogen-embrittlement-free process. If you do plate and bake, for every point you go up in Rockwell, the risk goes up.
And if your articles are under 32 Rockwell 'C', you can stop worrying about hydrogen embrittlement.
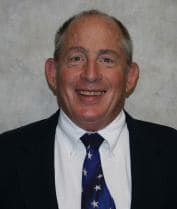
Tom Rochester
CTO - Jackson, Michigan, USA
Plating Systems & Technologies, Inc.

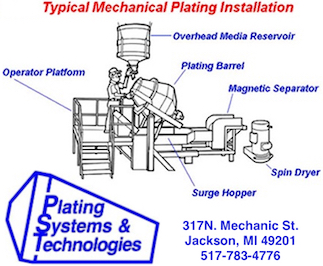
September 2014
Very informative Tom. Thanks.
Regards,
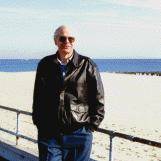
Ted Mooney, P.E.
Striving to live Aloha
(Ted can offer longterm or instant help)
finishing.com - Pine Beach, New Jersey
A. Hi Tom,
I disagree with your statement "if the fracture face has a 'rock candy' aspect it is certainly hydrogen embrittlement".
Tempered martensite embrittlement (TME) and stress corrosion cracking (SCC) will also show a brittle fracture surface.
A brittle fracture in combination with intergranular decohesion ("cavities") is generally believed to be caused by hydrogen. However, we have evidence of fracture surfaces which had never been exposed to any form of hydrogen and showed this same picture...
Best regards,
Jeroen
- Geldrop, The Netherlands
October 5, 2014
I am searching other option for hydrogen DE-embrittlement than heating. As we face problems with 10.9 and 12.9 fasteners for coating.
Each time heating is not possible.
- Pune, India
April 12, 2015
A. Hi Dhiren. How about using coating processes that don't cause hydrogen embrittlement, as suggested by Tom R?
Regards,
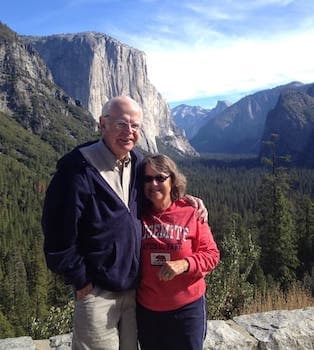
Ted Mooney, P.E. RET
Striving to live Aloha
(Ted can offer longterm or instant help)
finishing.com - Pine Beach, New Jersey
April 2015
Q. Hi Ted, first of all I love the new pic. Second, what is the best reaction if parts have passed the 4 hour window to start the hydrogen relief bake?
We started the 24 hour bake about 10 - 12 hours after plating had finished due to a malfunctioning oven controller. Can we extend the bake time? If we strip the parts for re plate am I just doubling the hydrogen?
The parts are quarantined for now but I can't find much literature that helps with my problem.
- Los Angeles, California USA
May 19, 2015
(includes 7 papers / 34 pages on electroplating)
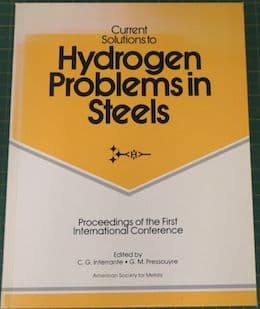
on eBay or Amazon
(affil link)
A. Hi Michael. Twenty years of running this site has made me the very definition of "jack of all trades, master of none". Although I have an acquaintance with hydrogen embrittlement, I am unable to offer the serious specialized help you need ... but I can say with reasonable confidence that stripping & replating will not help, and that nothing you do now will fix the problem.
Hydrogen embrittlement issues are truly complicated. Small variations in alloy materials affect them, different plating and metal finishing procedures affect them, the applied plating can seriously inhibit de-embrittlement (for example, some papers suggest applying a thin layer of plating, then baking, then going back for the rest of the plating). It is possible that there was no embrittlement in the first place, and it is possible that the baking would not have helped if there was, and it's possible that baking within 12 hours was good enough -- no clear answers on that stuff :-)
So I think the actual answer is that if there was a customer spec detailing a de-embrittlement regimen which you did not follow to the letter, the parts are defective, period. And if there was no clear de-embrittlement spec you were ordered to follow, only a testing regimen can determine if the parts are acceptable. Hopefully another reader with specific experience can be more helpful.
Regards,
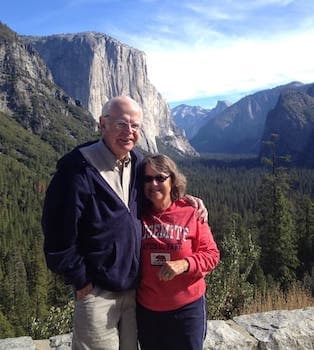
Ted Mooney, P.E. RET
Striving to live Aloha
(Ted can offer longterm or instant help)
finishing.com - Pine Beach, New Jersey
May 2015
A. Hi Michael,
Embrittlement relief is a pretty complex subject, depending on material strength or hardness, surface treatments (such as case hardening), finishing treatments etc.
Most OEMs have their own interpretation of what the maximum delay time allowed is. There is little chance that an OEM will accept any high strength or high hardness material that has not been de-embrittled within the delay time stated in their specification. Hydrogen embrittlement is time dependent, the delay times are usually set to where the OEM is comfortable that embrittlement has not started and will be very reluctant to move from that requirement.
End of the day you are going to have to go back to your customer, tell them what happened and ask what remedial actions are necessary (if any are possible).
The biggest problem with hydrogen embrittlement is that it is impossible to detect without destructive testing. There are no obvious signs of embrittlement on the surface, so you will not even be able to judge which parts may or may not be affected.
Aerospace - Yeovil, Somerset, UK
May 21, 2015
A. Several years ago there was a company in the USA that sold testing equipment for H2 embrittlement testing. As I remember it was a long high vacuum process. Measured the released H2 amount, not the effect.
It was not cheap.
- Navarre, Florida
May 21, 2015
Q. After plating screw, within 1 hr we did hydrogen de-embrittlement for 6 hrs at 190 °C. From this a few sample parts were tested for hydrogen de-embrittlement and found free from entrapped hydrogen.
And remaining parts we had plated for 20 mins and did passivation. But after testing it is found that entrapped hydrogen is not completely removed. What will be the reason? Please suggest.
Trupti P.- Pune, Maharashtra, India
April 14, 2019
A. Your letter prompts more questions than answers.
(1) What was the Rockwell hardness or tensile strength of the fasteners involved?
(2) How were the fasteners tested for entrapped hydrogen? (It is virtually impossible that they could have been totally free of entrapped hydrogen regardless of the length of the baking cycle or the tensile strength of the fasteners.)
(3) In your second paragraph, clearly if you do not bake you will have more hydrogen in the fasteners and not less; do you agree?
Regardless of the amount of hydrogen in the fasteners, if they are subjected to a load for 48 hours and do not fracture, there is very likely to be no issue; if they fail, regardless of the amount of hydrogen, there is an issue.
There are non-embrittling processes to provide sacrificial protection to fasteners, including zinc-rich paints (Yuken, Doerken, Magni, Geomet, Dacromet and others) and mechanical plating.
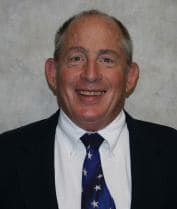
Tom Rochester
CTO - Jackson, Michigan, USA
Plating Systems & Technologies, Inc.

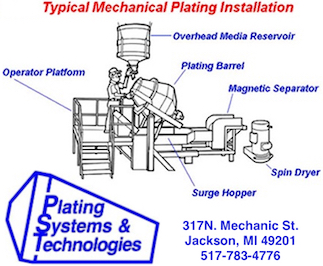
June 5, 2019

Q, A, or Comment on THIS thread -or- Start a NEW Thread