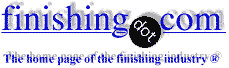
-----
Silver plating on copper plating
Q. Silver plated aluminum (probably 6061)parts with a copper underplate exhibit blistering after 4-5 years in hermetically sealed environment. Parts submitted to me for failure analysis. These are commercial off the shelf parts purchased by my company.
I have 21 years experience with metal finishing and associated problems. Visually, this looks like a classic cleaning/rinsing problem. The external surface of the silver appears fine. I have performed an analysis of the corrosion residues using Energy Dispersive X-ray. The analysis shows pretty much what I expected. Potassium, copper, carbon, oxygen, silver, magnesium, zinc, aluminum, and a trace of chlorine (probably as chloride). Question is why do I not see nitrogen from the cyanide, assuming a cyanide based silver or copper bath was used?
Jay Otts- Garland, Texas
2003
A. You did not mention where the blistering occurs: from the Al or from the Cu. If the blisters separate from Al, cleaning and preparation should be reviewed, however, even with good preparation, if the copper thickness is insufficient to prevent near complete diffusion into the silver, blistering will occur. My experience tells me that a minimum of 0.003" of copper is required if any heating process such as soldering etc. is used. If the blisters are from the silver separating from copper, the problem is likely in the silver strike. (too much silver, low cyanide, low amps. contaminated solutions or rinses) chemical replacement deposits of silver on cu have little adhesion. Parts should go into the copper with current on (contact prior to entering the tank.)
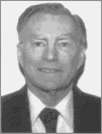
Don Baudrand
Consultant - Poulsbo, Washington
(Don is co-author of "Plating on Plastics" [on Amazon or AbeBooks affil links]
and "Plating ABS Plastics" [on Amazon or eBay or AbeBooks affil links])
2003
Multiple threads merged: please forgive chronology errors and repetition 🙂
Copper Plating Steel parts followed by Silver "Flash"
October 22, 2009Q. We are a telecommunications company and typically copper plate a lot of our components. However our current specifications seems a little odd
For STEEL AISI 1018 our current drawing calls out a copper strike before copper plate. Would we need this strike before copper plating? Isn't that redundant or does the copper strike allow for better adhesion for the copper plate? Can we just copper plate directly on this steel or is a strike such as Copper or Nickel required?
We may be adding a layer of Silver Flash over this Copper as well. So would this plating be sufficient:
1) COPPER STRIKE PER ASTM B734, 0.76 µm (.00003") MAX.
2) COPPER PLATE 5.0µm to 10.0 µm (.0002" to .0004") PER same spec
3) (FINISH PLATING) SILVER FLASH 1.0 µm TO 2.0 µm PER
ASTM B700
Thanks
Engineer - Columbus, Ohio
October 22, 2009
A. Hi, Rocky. Acid copper will not adhere to steel and must be preceded by a copper cyanide, copper pyrophosphate, or nickel strike. Good luck.
Regards,
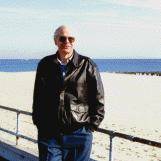
Ted Mooney, P.E.
Striving to live Aloha
(Ted can offer longterm or instant help)
finishing.com - Pine Beach, New Jersey
![]() |
October 23, 2009 Q. OK Thanks. I have corrected this plating requirement to be: - Columbus, Ohio A. The copper and silver will diffuse together and the corrode. You need a diffusion barrier like nickel. ![]() Robert H Probert Robert H Probert Technical Services ![]() Garner, North Carolina ![]() October 25, 2009 |
A. You should certainly use a copper cyanide strike when plating onto steel and even more so with Invar. You should also use a live entry to prevent any risk of an immersion deposit. Silver will diffuse into the copper, but the rate will be dependent on the operating temperature. In an ideal world, a barrier layer should be used and historically nickel has been the easiest option, but nowadays other ones, such as white bronze or palladium are also used. You can also use platinum, but this is very expensive at present. Although not relevant here, the use of nickel as a barrier layer is banned in anything that will come into contact with human skin for any prolonged period
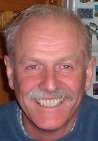
Trevor Crichton
R&D practical scientist
Chesham, Bucks, UK
October 27, 2009
October 31, 2009
A. Rocky
My first point is that it is impractical to advise on a plated finish without knowing what is its purpose.
Is it for corrosion resistance, solderability, a low friction surface? I will guess that you have a contact of some kind.
Ted is quite right, over steel you need a copper cyanide strike but it unusual to quote a thickness for this. It is followed immediately by copper plating and the spec thickness is the total. (It is not usual to quote the strike in the spec, the plater considers this part of the plating prep and may not be needed if the main plating bath is suitable). Remember, copper is soft. If you have a high pressure contact then steel/nickel/silver may be considered.
If a barrier layer is needed to prevent diffusion it will be nickel (forget the exotic suggestions in the real world)
If the part can be electroplated with copper then it can be nickel plated. Electroless nickel is an expensive option and offers no advantage here.
Silver is often used to give a solderable surface or as a "cheap" alternative to gold for connectors (but requires contact pressures to be increased)
Lastly, the term "Flash" is common in the jewelry trade and is taken to mean the minimum thickness which will give an acceptable cosmetic finish i.e., almost nothing! It should never be used in an engineering specification - just state the thickness.
If you use Invar, the question is why plate?
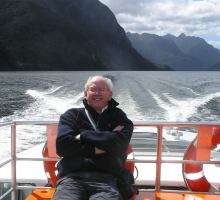
Geoff Smith
Hampshire, England
What is correct plating thickness of copper strike for silver plate?
Q. We are manufacturers of gears for aerospace applications. One gear in particular requires silver plate of .0003" max. The AMS2412 spec allows for up to .0005" of copper strike. This seems odd; it is not specified relative to plating thickness which of course is on any particular print. I have several questions regarding this: What would be the optimal amount of copper strike for this thickness of silver. What is the optimal copper strike for best adhesion? Can too much copper cause adhesion problems for the silver plate? Why doesn't the spec specify a maximum amount relative to the overall thickness?
Steve PykeQuality - Troy Michigan
February 12, 2016
A. Hi Steve. I assume that the purpose of the copper and silver plating is as a break-in coating, rather than as a heat-treating stop-off coating? If so, I doubt that the thickness matters (see Geoff Smith's response above), and that it should be held to a minimum (complete coverage and done). But we'll see if a more knowledgable reader can add anything.
Regards,
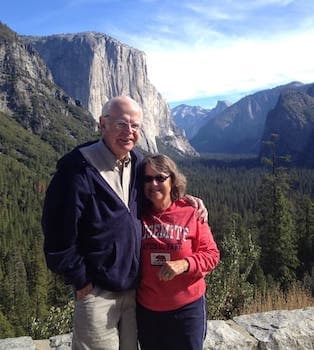
Ted Mooney, P.E. RET
Striving to live Aloha
(Ted can offer longterm or instant help)
finishing.com - Pine Beach, New Jersey
February 2016
Q. Hi Ted
Thank you for your response.
You are correct that this is a "break in" coating on a sun gear in a planetary system. The customer is finding an increased amount of silver and copper flakes/particulate in the filtration systems of the engines after X amount of engine hours. This may or may not be an adhesion problem. The only variable I have been able to determine on this most recent lot from many previous is the copper flash is thicker (.0001" ish) but well within specification.
Steve Pyke [returning]- Troy, Michigan
February 15, 2016
Q, A, or Comment on THIS thread -or- Start a NEW Thread