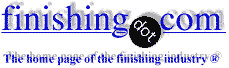
-----
Ultrathin anodizing
Quickstart:
Readers who are not yet familiar with anodizing and its terminology may wish to start with our Aluminum Anodizing (Anodic Oxidation of Aluminium): Intro & FAQs
Q. I am dealing with a 6061 aluminum application that runs in contact with fibrous materials which develop black color I assume from the natural aluminum oxide being wiped off. It is not necessary to 100% eliminate this, but I would like to significantly reduce the black transfer onto the fibrous material. I am considering anodizing the aluminum to prevent this, but want to minimize anodize build up on the aluminum surface due to concerns of changes to surface tribology, flaking (contamination) and possible reducing heat absorption. Are there guidelines that may help specify this type of minimalist anodizing process?
TIA
Product Manager - Bellows Falls, Vermont
June 19, 2023
A. Hi Gregg.
One guideline is that anodizing at a temperature around the freezing point (Type 3 anodizing) will likely give you more abrasion resistance than anodizing at room temperature (Type 2).
Another thing you might want to consider is that "flaking" is less likely to occur if the geometric design is good (since anodizing grows from the surface, inside corners can cause clashing while outside corners can cause lack of coverage; flat or round surfaces are usually less susceptible to such problems.
Luck & Regards,
Ted Mooney, P.E. RET
Striving to live Aloha
(Ted can offer longterm or instant help)
finishing.com - Pine Beach, New Jersey
Q. I'm trying to develop some process control for an operation that is far older than tenure. We routinely anodize (Type III) very thin .002" - .003" ^ .004" - .006" aluminum sheets with the intention of using the anodized layer as a non-conductive barrier on the part.
The current technician was under the impression that when he needed to add electrolyte to the bath, he should be adding an acid/water solution exactly as the bath was originally made. The bath was tested (by a paid lab) before we moved the tank at over 600 g/L sulfuric acid.
He is used to running these parts at 1A@24v using a CC power supply, with a bath temp ~34-38 °F.
Now with the bath at a much lower concentration (I'm just setting up a titration station), he is telling us that the thicker parts are working, but not like they used to (has to increase amperage). And the thinner parts won't build any oxide unless he turns up the amperage, and at that point has burned the sheets.
What benefit does a higher acid concentration have when running these very fragile parts?
I've been thrown into the middle of this, and am doing everything I can to understand the chemistry, best practices, and past operation while trying to dial back in a documented procedure.
I'm reluctant to just add acid without understanding the effects this might have. Hope to have a good titration of the current bath by the end of the day.
Mfg. Engineer - Minneapolis, Minnesota
April 14, 2025
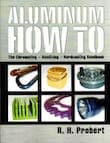
Aluminum How-To
"Chromating - Anodizing - Hardcoating"
by Robert Probert
Also available in Spanish
You'll love this book. Finishing.com has sold almost a thousand copies without a single return request :-)
A. Hi William.
To really get into this you need to know what alloy that you are anodizing, the surface area of the parts, and the target thickness of the anodizing. Knowing that the applied current is 1A isn't quite useful until you know its surface area so you can investigate the current density. Knowing the voltage isn't fully useful until you know the alloy.
You are applying the coating at ~34-38 °F, which is slightly high for Type 3 anodizing. Calling it "Type 3" when it's probably far thinner than the 0.001-0.002" typical thickness of Type 3, (which it probably is considering the thickness of the substrate), may be okay but could be misleading.
Please try to tell us the alloy, the current density (for example, amps/sq.in., amps/sq.ft, amps/sq.dm).
Luck & Regards,
Ted Mooney, P.E. RET
Striving to live Aloha
(Ted can offer longterm or instant help)
finishing.com - Pine Beach, New Jersey
Q. The material is 1145 alloy, with a finished surface area (according to CAD) of 47.5sq. inches. So, about .02A/sq in.
We are only trying to add about .001"-.0015" thickness to sheet.
My mistake on the initial sheet thickness. These "Thick" parts are .006", and the thin parts are .004".
Mfg. Engineer - Minneapolis, Minnesota
April 15, 2025
A. Hi William. I think there are additional typos. Probably it should be 10A rather than 1A, for a current density of 0.2 ASI (28.8 ASF) rather than .02 ASF?
According to the "720 rule" (time in minutes = 720 x mils / ASF), it should takes about 25 to 38 minutes to deposit .001" to .0015" at 28.8 ASF. Does that sound about right?
If thin pieces burn but thick one don't, it sounds like you have a racking/contact problem rather than, or in addition to, a solution concentration problem. But building up .001" to .0015" thickness with only a 24 volt rectifier, at 34-38 °F temperature sounds more like a job for a proprietary solution with glycolic acid or other additives than straight sulfuric acid. And 600 g/l of sulfuric acid is over 3X the conventional amount and seems extremely unlikely despite your analysis.
There just seem to be so many wrong numbers everywhere, that it might be more efficient to get an anodizing consultant in for a couple of days than to continue this struggle of trying to determine what reportedly used to work.
Luck & Regards,
Ted Mooney, P.E. RET
Striving to live Aloha
(Ted can offer longterm or instant help)
finishing.com - Pine Beach, New Jersey
Multiple threads merged: please forgive chronology errors and repetition 🙂
Q. Is it possible to anodize a thin film that has been deposited onto an insulator? For example, 5000 angstroms of Al on a quartz plate.
Troy Reichard1998
A. Troy,
Thin films of aluminum can be anodized using a barrier anodization technique where the thickness of the anodized layer is proportional to the applied voltage. It is very important that there not be any tramp chlorine ions in the electrolyte. This type of anodization is used to make thin film capacitors.
Donald M. MattoxSociety of Vacuum Coaters
Albuquerque, New Mexico
"Handbook of Physical Vapor Deposition (PVD) Processing" (2010) [on AbeBooks or eBay or Amazon affil links]
and "The Foundations of Vacuum Coating Technology" (2018) on AbeBooks or eBay or Amazon affil links]
Verifying very thin (1-2 microns) anodize layer
Q. I have some parts that have been clear anodized. The anodize coating (per anodizer) is very thin (~2 microns). It appears to still conduct electricity. Is there an alternate method to check for an oxide layer such as testing reaction to some chemical?
Based on prior issues I think the layer is too thin to resist penetration by ink. I work at a machine shop that has had issues with wear on parts that have been anodized and I want to verify the presence of clear anodize on 2024 aluminum. The appearance of the metal is identical before and after and it still conducts electricity.
Buyer - Engineer at a machine shop that anodizes aluminum. - Cincinnati, Ohio
2007
A. At the risk of slight simplification, it sounds like a supplier is claiming you have an "anodized coating" that is too thin to be visible, dyeable, provide wear resistance, or serious electrical insulation. Therefore the question of whether it's actually there may be moot depending on the application.
Most anodized coatings are about .0002"; coatings of .0001" are for interior use only and for very limited abrasion-- and yours are only half of that. But I would still expect it to be electrically resistive. If it's a serious contract dispute, a lab could take SEMs that would show you what you have.
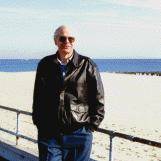
Ted Mooney, P.E.
Striving to live Aloha
(Ted can offer longterm or instant help)
finishing.com - Pine Beach, New Jersey
A. By far the easiest method of checking is electrical. However, a flat probe must be used (rather than a needle tip which punctures the coating). From Aluminium Federation Bulletin 39 data given on p. 1054 (6th edition) of The Surface Finishing of Aluminum and Its Alloys ⇨
2-3 microns of anodize on an alloy such as 2024 has a breakdown voltage of ~100 Volts.
- Goleta, California

Rest in peace, Ken. Thank you for your hard work which the finishing world, and we at finishing.com, continue to benefit from.

Q, A, or Comment on THIS thread -or- Start a NEW Thread