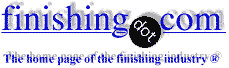
-----
Increasing plating speed with agitation, eductors, or non-aqueous baths
Q. A client is interested in increasing the speed of copper plating prior to buffing. Does anyone have experience with the use of educators for this purpose?
BERT SHERWOOD- LOS ANGELES, California, USA
2003
A. To a point, increasing solution agitation will clear away the "barrier zone" or "diffusion layer", the area that is a few millionths of an inch thick where all of the metal ions have plated out and the pH has changed slightly. Stronger agitation allows new metal ions to get to the substrate faster than by the diffusion process. Result - You can use a higher current density without burning. Look at the turbulence they use on high current density plating on wire or continuous coil plating. Educators will help to a point, but only to a point. The faster you plate, the more sensitive the operation gets because every piece must receive a given amount of agitation. Racking has to get very good for this. Can you gain a few percent in plate rate? Quite possibly. Will educators be enough ? Maybe.
James Watts- Navarre, Florida
2003
Conforming anodes and pumping through of electrolyte
Q. We are a nanotechnology R&D operation and apply plating techniques in some areas. Can anyone recall a process developed by General Motors Canada for the plating of what was then a complex shape Pontiac bumper bar. As I recall it was for the front bumper of the 1957 Pontiac (or Oldsmobile). The process was using conforming nickel anodes and enclosing the bumper bar in a cell shaped to the same configuration. The plating solution was pumped through the cell at a high rate. The main advantage was plating current densities of 700 amps/Ft2 , and plating time of 3 minutes.
The process was not used for any extended period, and as far as I know was never used again.
Does anyone have any knowledge of advantageous plating by pumping solution through or around articles while processing?
The application is for electroplating, not electroless.
- Carlsbad, California
2006
A. Hi Raymond. I'm not familiar with that Pontiac situation, but you will probably find something in the literature under "jet plating" or "impingement plating". Yes, very high plating rates are possible with strong impingement of plating solution onto the parts, and the reasons are twofold. First, you get plenty of fresh solution at the plating surface so you aren't working with ion-depleted solution (which happens fast at very high plating rates). Second, you greatly thin the boundary layer where the plating rate is diffusion dependent. This technique is used on reel-to-reel plating.
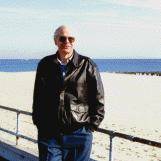
Ted Mooney, P.E.
Striving to live Aloha
(Ted can offer longterm or instant help)
finishing.com - Pine Beach, New Jersey
2006
Q. I am plating in a lab setting with a 250 ml beaker [beakers on
eBay
or
Amazon [affil link] of copper sulphate
⇦ on
eBay or
Amazon [affil link] and sulfuric acid.
I am reading in several articles that agitation of the beaker to increase the flow of ions to the diffusion barrier is important. To what extent (speed of the stir bar) is agitation effective. I always set it to about half the maximum speed on the stir plate. However, is there an optimal speed for agitation?
Thanks
- Wilmington, New York
June 4, 2013
A. Hi Luke. The short answer is that you can rarely have too much agitation, so I'd try turning it up :-)
The longer answer is that agitation does two basic things:
1. It assures general solution homogeneity, i.e., that the temperature and solution concentration is the same throughout. That's very important in deep tanks, or where the process generates a lot of heat like in hard anodizing, and for even plating thickness, and to prevent burning at high plating speeds, etc. Probably not important in your case.
2. As James notes above, agitation can thin the boundary layer. If you were able to actually microscopically see the dynamics going on in a plating cell, you'd see that once you are a very short distance from the anode, and until you get very close to the cathode, not much is happening. Ions are migrating through the solution from anode to cathode, but the solution is quite uniform, and that's about it. However, once you get really close to the cathode, the magic starts happening as ions are reduced to metal. As one ion is converted, another must get across the zone for the process to continue, the pH must correct itself, etc. I don't pretend to deeply understand the situation, but the trip across this zone is slow and difficult; so extreme agitation, such as jet plating on reel-to-reel electronic strip components, which provides turbulence all the way to the cathode, can greatly thin that boundary layer, allowing much higher plating speeds.
I doubt that you'll actually see any difference between mid-speed and high speed stirring in a beaker though.
Regards,
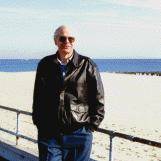
Ted Mooney, P.E.
Striving to live Aloha
(Ted can offer longterm or instant help)
finishing.com - Pine Beach, New Jersey
June 5, 2013
Increasing Electroplating Speed
Q. I am interested in learning more about electroplating. In my research, I can't seem to find the answer to a few questions involving the limitations of electroplating with respect to plating speed. Could someone please tell me why either or both of these methods would not be successful in increasing the speed of electroplating.
1. When plating a relatively small object, consider having two additional electrodes with much larger surface areas submerged in the plating solution. These electrodes could have a potential between them to constantly saturate the plating solution and allow for higher plating rates on the substrate. This could possibly be done by removing potential from the substrate to quickly recharge the solution with the large electrodes and then quickly discharge the solution's ions on the substrate. This could also potentially be done with carefully controlled potentials between the two electrodes and the substrate.
2. Are there non-aqueous solutions that would resist dissociation such as that that occurs with hydrogen atoms when using aqueous solutions? Would this allow for a faster plating rate that avoids "burning"? I'm thinking of a special oil formulation or perhaps some type of liquid metal solution using something like gallium? I realize there are external considerations such as environmental issues and sourcing issues but I'm primarily interested in physical limitations.
Any help in answering these questions is greatly appreciated.
Hobbyist - Indianapolis, Indiana USA
October 20, 2015
A. Hi Aaron. 1. I don't think the transport of ions from the general area of the anode to the general area of the cathode is any sort of limitation, so I'm not seeing what your additional proposed electrodes achieve. I think the biggest trick to increased plating speed is extreme agitation to thin the boundary layer adjacent to the cathode. This is where the magic happens and as it happens the boundary layer gets depleted, limiting the plating peed. I've heard of plating speeds generally about 10X the conventional limit on strip plating when a high pressure jet of plating solution is pumped against it.
2. Sorry, I don't personally know what limits apply when molten salts, ionic solutions, or organic electrolytes are employed instead of aqueous solutions.
Regards,
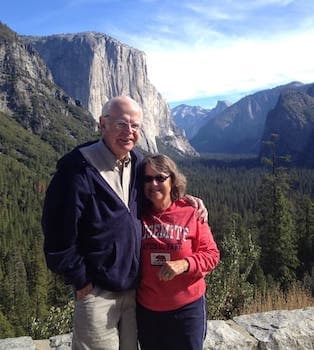
Ted Mooney, P.E. RET
Striving to live Aloha
(Ted can offer longterm or instant help)
finishing.com - Pine Beach, New Jersey
October 2015
Q. I am also very interested in the speed limitations for plating and would like to understand the theoretical route to achieving deposition rates of ~1 um/s. Aaron Tolly asked the same questions I had regarding non-aqueous electrolytes or methods to increase the concentration of ions near the boundary layer.
What is the best deposition rate you are aware of (in um/s) and can anyone speak to the theoretical and practical process limitations (or suggest an expert in the field I could contact)? My current understanding is that .1 um/s is very good and perhaps representative of the fluid impingement deposition method?
Thanks,
-Daniel
- Raleigh, North Carolina, USA
April 17, 2018
Q. I am copper plating thin film using two anodes, one on either side. I am using a magnetic stirrer directly beneath the thin film cathode. I found that stirring at relatively high RPM (600+) produces uneven coating thicknesses. The coating grows preferentially on the edge of one side and on the opposite edge for the other side. I realized that this is caused by centrifugal forces pushing the copper cations off to the opposite edge on both surfaces. A reduced stirring rate (200 RPM) eliminated this effect. In summary, increasing the agitation for faster plating can have adverse effects on throwing power.
If anyone has established settings for copper plating relatively thick (200 µ) dense coatings please reply. Many Thanks, Paul
Paul MoroneyMetallurgy - Limerick, Ireland
July 31, 2019
A. Hi Paul. I don't have the data you seek, but I do observe that if magnetic stirrers in beakers create this downside which you speak of, they probably aren't the right approach when trying to optimize the process :-)
Regards,
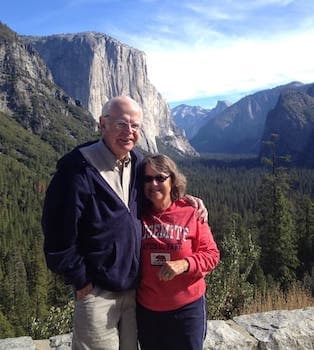
Ted Mooney, P.E. RET
Striving to live Aloha
(Ted can offer longterm or instant help)
finishing.com - Pine Beach, New Jersey
December 12, 2019
Q. I am working on an idea that involves increasing the speed of the water agitation.
A common approach to a better plating surface involves agitation, using air bubbles to move the solution around the plating surface.
Another is using a magnetic stirring device or moving the model to get a better-plated surface.
Are there any examples out there that force just water(no air) across the anode where the water stream then impacts the item being plated?
Imagine a race track where water enters the tube and keeps circling around. Water blows past the anode heading directly at the item. Water that moves past the item circles back to the anode to flow past the anode again.
Kind of an electroplating spray gun.
Secondary question considering the above-could higher currents allow faster plating while maintaining surface quality?
I can't find anything out there so I would like to hear what you think.
Hobbyist - Visalia, California
A. Hi JB. We added your inquiry to a related thread. I understand what you are saying about "speed of the water", but search instead for "jet plating" or "impingement plating" and I think you'll find the info you are looking for. It's "sort of" the speed of the water, but more precisely it's probably "the force of the impingement" that is of interest.
The solution will have plenty of ions and they will move to the general vicinity of the cathode easy enough. The actual limit (usually) is that the ions can diffuse through the boundary layer only so fast. So when the plating solution impinges strongly on the cathode, it significantly thins that quiescent boundary layer and its slow diffusion, and allows much faster plating speeds. It's relatively easy to do for strip plating, but probably much trickier for odd shaped individual parts.
Regards,
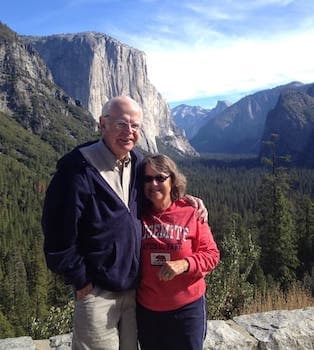
Ted Mooney, P.E. RET
Striving to live Aloha
(Ted can offer longterm or instant help)
finishing.com - Pine Beach, New Jersey
December 2019
Thank you, Ted.
The terminology you used is now on my shortlist to Google.
The thread above looked promising to my inquiry and your input even more so.
It's a rare moment to not fail on the launch pad.
Thanks for the reply ... I'm off to research.
jbc
- Visalia, California
December 13, 2019
Why in electrical double layer the thickness of diffusion layer is decreased by increasing temperature?
Q. MY NAME IS Pedram and I am a Ph.D student at IUT.
Pedram vg- Isfahan, iran
February 25, 2020
Q, A, or Comment on THIS thread -or- Start a NEW Thread