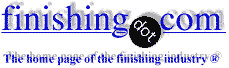
-----
Codeposition of Nickel and Silicon Carbide
Hi,
I developed a new process for codeposition of Ni-SiC. My particle size is now less than 0.5 microns. I still have some problems to stabilize the dispersion system. Does anyone has an idea for a better stabilizing? Right now I'm looking for some wetting agents and dispersive agents for stabilizing. Might someone can give me a tip.
Thanks,
Dominik [last name deleted for privacy by Editor]- Bern, Switzerland
2003
Dominik, co-deposition systems are still considered trade secrets and in many cases covered by patent. So you might start with a patent search to see what you can and can't do. If someone wants to refer you to published literature on these matters, though, they are welcome to.
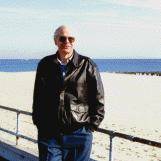
Ted Mooney, P.E.
Striving to live Aloha
(Ted is available for instant or longterm help)
finishing.com - Pine Beach, New Jersey
2003
You might want to look at the patent for Tribomet T104c which is chromium carbide in cobalt sulphate bath. It was patented over 20 years ago, so it should expire soon. It is a pumper plate with air agitation. Plating-quality wetting agents should work. Agitation is the only practical way of suspension. I think that pumping could work a lot easier than the pumper plate, but the pump and pipes would have to withstand a lot of abrasion. A note of warning, the carbide picks up a slime from the breakdown of the wetting agent and periodically requires a peroxide treatment to allow it to codeposit. This is a nasty process and you should really have two sets of treated carbide, so you are not under the gun for production. Another requirement is a very close quality control of the particle size. The smaller ones plate out faster and your particle % goes down quite fast after that because the larger ones are less prone to encapsulation.
James Watts- Navarre, Florida
2003
Q, A, or Comment on THIS thread -or- Start a NEW Thread