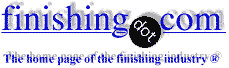
-----
How to Bright Polish Brass Castings
Q. I have a potential product that I am developing that requires a cast brass wheel. The wheel is approximately five inches in diameter and has spokes that are also part of the cast brass wheel. The wheel is in the style of an old wagon wheel. I need to know how to polish this wheel to a bright finish. Some have suggested to vacuum impregnate the wheel and then dip plate the wheel. After the wheel is plated we could hand polish it to the desired finish. I'm not sure that this would be the correct process, but if it is,
I need potential suppliers.
Thank you,
Todd C. Obbie- Rochester, New York, USA
2003
A. If you have any reasonable volume, the least expensive method would be burnish the parts using a mass finishing system.

AF Kenton
retired business owner - Hatboro, Pennsylvania
2003
A. The best way to start is tumbling or vibratory finish in a heavy cutting ceramic media, to level the surface and blend. A sand cast part may require more time in cutting than an investment casting. When the surface is smooth and level, the part should then be run in a fine plastic media to refine the surface and remove scratches. The final finish operation is dependent on how good the bright finish has to be. An industrial bright finish can be achieved by burnishing in steel shot. To achieve a high cosmetic finish such as jewelry, you will have to hand buff for this stage.
Todd Leonardis- Piscataway, New Jersey
2003
A. For a large run, more than fifty units, a two part steel die will give you consistently perfect castings. The dies should be perfectly fitted as two halves, preferably tested using liquid plaster of paris as an indicator of symmetry or leakage. Dowel pin locaters should be fitted to the corners. When in use, this die should be preheated before pouring in the molten metal, to avoid a broken shrink. Also, a one thousandth coat of hard chrome plating will allow for easier casting removal once the die is reopened; it also will protect the smooth finish of the die. Pieces cast thusly are very easily polished with a sisal buff and brown tripoli buffing compound ⇦ on eBay or Amazon [affil link] . Hope this sets you in the right direction.
Mark Gunn- Australia
2003
A. Okay, so first it's brass, very soft. You know what a dynafile is? Find out then use it. It will be able to get to all the hard reach spots. Now abrasive ... I'd start with say 120 grit WITH GREASE ON THE BELT always. Then go to say a red {med} scotchbrite belt with grease; then a blue s/b belt with grease; then it's buff time. First, hold on very tight; do not put fingers in the spokes. Okay, buffing compound 1 red or brown, hard buff, then green, fine soft slow buff. Have a good time; scott out
scott regenauer18 years metal finishing - st paul Minnesota
2003
A. All the suggestions mentioned above are good, but volume and the desired surface finish relates to $ per man hour. We still don't have a quantity.

AF Kenton
retired business owner - Hatboro, Pennsylvania
2003
Q. We need to find the best set of steps to polish to a very high shine our brass jewellery .... so as to come out from cast we would like just to cut off and file just where the sprue was ... and straight to vibrating using various media and compounds ... please inform us best possible way.
SILVIO VASSALLOmanufacturer - BANGKOK THAILAND
October 23, 2012
Q, A, or Comment on THIS thread -or- Start a NEW Thread