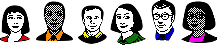
Metal finishing Q&As since 1989
-----
Color anodizing of diecast aluminum
Q. Does anyone have any experience, comments on decorative color anodizing or die-cast aluminum? Is an intermediate plating of zinc or chromate required (because of the high silicon content of the aluminum)?
Any suggestions, tips, references, samples would be most appreciated.
michael rose- Boxborough, Massachusetts
1998
A. Michael:
We are metal finishers specializing in aluminum anodizing and you picked a very difficult alloy to anodize, especially in colors. A few suggestions: Tumble the parts in a stainless steel media prior to anodizing. The colors you pick should be dark (Black, Blue, Red). You can not zinc plate or chromate finish prior to anodizing aluminum. If you need further assistance please feel free to E-Mail me.
Regards,
Bob BramsonB&M Finishers / Prismatic Stainless Steel

Kenilworth, New Jersey
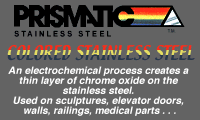
1998
1998
A. See the responses to Letter # 2053. Whether it's conventional or hard coat anodize, the coating still comes out grey, and it is difficult to have an aesthetically pleasing appearance with any dye with die cast. I wonder if anyone has ever IVD-coated a die cast part, then anodized the IVD aluminum. You can't remove the silicon, so maybe it can be covered up.
Phil Johnson
- Madison Heights, Michigan
"The Surface
Treatment &
Finishing of
Aluminium and
Its Alloys"
by Wernick, Pinner
& Sheasby
on
AbeBooks
or
eBay
or
Amazon
(affil links)
A. The high level of silicon in most aluminum diecastings makes sulfuric acid based anodizes turn an uneven dirty gray almost immediately. Color dyeing does not cover this up, in fact, it often highlights the problem. Several approaches are possible:
1)With proper pretreatment, fair cosmetics are possible with anodizing and the darker colored dyes.
2)Alloys without silicon, such as 518, produce much better results. However, they are difficult and expensive to diecast.
3)IVD coat(vacuum deposited aluminum)the part prior to anodize. We have done that here and it works very well. However, this is also expensive.
4)There is a new kind of coating becoming available, known as plasma or mircoarc anodizing. They are naturally off-white but some versions are available with an integral black color. Our high silicon diecastings have a very uniform satin black coating.
5)Chromate pretreat and paint the piece.
Chris Jurey, Past-President IHAALuke Engineering & Mfg. Co. Inc.

Wadsworth, Ohio
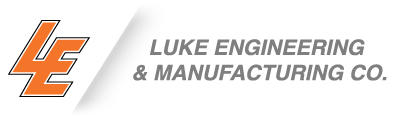
1998
A. Another solution is to die cast low-silicon alloys using a slurry die casting process. These low-silicon alloys can then be anodized to give nice colors.
The issue is how to die cast these low-silicon alloys with high quality and low production costs. These alloys tend to have hot tearing and die soldering problems. Slurry die casting may be used to solve these problems.
- Bangkok, Thailand
August 12, 2015
Q, A, or Comment on THIS thread -or- Start a NEW Thread