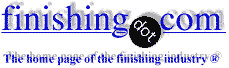
-----
WEAR PROBLEM WITH ALUMINUM VACUUM PLATES
Q. I HAVE ALUMINUM VACUUM PLATES THAT REQUIRE AN EXTREMELY HARD WEAR SURFACE. TRIED HARD COAT ANODIZE .003 THICK BUT IT FAILED IN 3 WEEKS. SURFACE IS SAND BLASTED FOR ROUGHNESS. PLEASE ADVISE OF ANY PLATING OR COATING PROCESS THAT WOULD SURVIVE THE HARSH CONDITIONS OF SHUFFLING CARDBOARD 24/7 MATERIAL IS 7075 T6.
JEFFREY A CUENIN- LANCASTER, NEW YORK, USA
2003
A. Electroless Nickel with a 60 RC hardness usually outlasts Hardcoat in sliding applications. Hardcoat is hard but it has terrible lubricity or sliding wear.Electroless nickel can also be stripped and replated on aluminum parts without damaging the aluminum.
Todd Osmolski- Charlotte, North Carolina, USA
2003
That 'stripped and replated' point is well taken, Todd. Thanks.
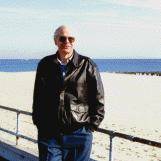
Ted Mooney, P.E.
Striving to live Aloha
(Ted can offer longterm or instant help)
finishing.com - Pine Beach, New Jersey
2003
![]() |
A. I would try 0.005 of hard chrome plate. There has to be some other factor besides abrasion to wear out 0.003 of hard coat in 3 weeks. I do not think that a coating of 0.0015 of EN would last any better than the hard coat. James Watts- Navarre, Florida 2003 A. Electroless nickel plating may be the coating of choice. I suggest low phosphorus type. hardness as plated can be 700 Knoop, 100 gm load. ![]() Don Baudrand Consultant - Poulsbo, Washington (Don is co-author of "Plating on Plastics" [on Amazon or AbeBooks affil links] and "Plating ABS Plastics" [on Amazon or eBay or AbeBooks affil links]) 2003 |
![]() |
A. After talking with you and neglecting to get your phone number I thought up some other trials. We talked about being sure the hard coat was done at about 32 °F for maximum hardness. We also discussed the fact that the crystal builds perpendicular to the surface and that on micro curved surfaces such as you would have with a rough sand blast, the crystals would build up to a certain thickness and then crash into and break off each other. You were going to try a smoother starting finish so that the crystals will build straight out and not crash. ![]() Robert H Probert Robert H Probert Technical Services ![]() Garner, North Carolina ![]() 2003 A. Jeffrey, did you anodize first and then sandblast for roughness? The anodize may have heartburn with sandblasting as the substrate may not support it- depends on the intensity. Does the plate have to be aluminum? Chromium plated steel works in a wide variety of wear applications. If you want a hard, rough surface, have you considered thermal spraying? An HVOF coating of tungsten carbide is everyday technology, readily available, and may do what you need. ![]() Lee Gearhart metallurgist - E. Aurora, New York 2003 |
Treatment &
Finishing of
Aluminium and
Its Alloys"
by Wernick, Pinner
& Sheasby
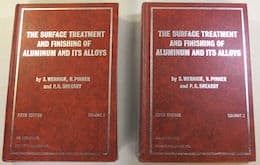
on eBay or Amazon
or AbeBooks
(affil link)
A. Thought I would put my two cents worth in this brainstorming session. EN is better than hardcoat for sliding wear. The best plated finish IMHO would be EN/codeposited silicon carbide. We did a plastic injection mold one time that had to be modified after plating was completed. The mold maker told me he had worn out diamond tooling trying to grind the finish.
Dan Weaver- Toccoa, Georgia
2003
A. This is routine procedure for us (we are a thermal spray company). Simply coat the affected area with tungsten carbide with either a cobalt or nickel matrix - typical hardness is around 70 Rc with extremely low coefficients of friction. However, I agree with one responder that something other than wear must be affecting the surface to achieve so quick a failure?
Bill Ferree- Houston, Texas
2003
Q, A, or Comment on THIS thread -or- Start a NEW Thread