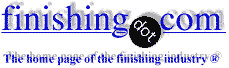
-----
High Mg 356 casting and aluminum anodizing
Aluminum clear anodizing of 356 casting. We had 1/3 of a load not anodize. We tried to anodize those parts by themselves - would not anodize - . It looked as though the casting was etching instead of anodizing. We had a good casting and a bad casting tested for alloy. The only difference was that the bad casting had a slightly higher percentage of Mg (good= .37 / bad = .41). The casting specification has a high limit of .45 for Mg. We believe the Mg was disolving faster than the aluminum would anodize. Have you heard of a problem like this before? Additional information: We attempted to lower the voltage - The amps jumped back and forth from high to zero. We attempted to Hard Coat anodize at 40 volts. Again the amps were jumping. At 1.5 thickness, we could still make electrical contact on the casting. At 2.8 we could not make electrical contact, but the casting smelled like sulfur.
Bob BramsonB&M Finishers / Prismatic Stainless Steel

Kenilworth, New Jersey
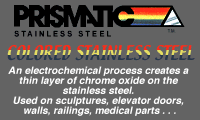
1998
Bob,
I do not think aluminum 356 casting is very hard to anodize. According to your description, it seems that current distribution is a problem. If you are using aluminum rack, fully stripping after each anodizing operation is very important. Otherwise you cannot get good contact. Also you need to check the contact of rack itself and the contact between flight bar and saddles as well as the contacts of cathodes. Is agitation in your tanks even? Deoxiding is a very important step in casting anodizing. You can contact Mr. Phil Johnson at Henkel to find out an adequate deoxidizer for castings.
Ling
Ling Hao- Grand Rapids, Michigan
1998
1998
Ling:
Thank you for your response. We have ruled out current distribution due to the fact that we took the casting that would not anodize and attempted to anodize it by itself with good electrical contact in a different anodize tank and also used the correct pre-treatment like you have suggested. We believe the alloying elements were not homogeneously cast throughout the casting (the Mg was 4.1% which is close to the upper end of the element limits for a 356). We believe the Mg was disolving quicker than the part was able to anodize. I look forward to your response.
Thanks,
Bob
B&M Finishers / Prismatic Stainless Steel

Kenilworth, New Jersey
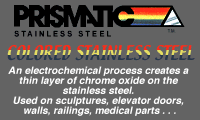
As Ling has said, 356 is normally a relatively easy alloy to anodize. Bob, I believe that you're correct in your guess that the high magnesium is linked to your problem, but from the description of your amperage readings, it sounds like the magnesium is not only high, which probably wouldn't hurt by itself, but there is segregated magnesium on the surface. It's the old adage from Physics class: electricity follows the path of least resistance. When you first turn on the rectifier the aluminum surface begins to anodize, but with just a slight bit of oxide present, the surface resistance rises rapidly, except in areas which are not oxidizing such as segregated magnesium. (Magnesium will anodize, but not at the same current densities or other conditions as aluminum). The current then concentrates in the areas with no anodize, converting Mg to Mg++, and generating oxygen, which is the gassing you see. As the magnesium burns away, you are left with bare aluminum, which may anodize, but which may also start to "burn" because it still has a lower resistance than the rest of the surface, and the current tends to concentrate there. All this would tend to make the ammeter fluctuate. This phenomenon occurs even with homogeneous alloys on a very small scale, and is the reason that hardcoat anodize is preceded by a ramp step. If your clear anodize is conventional type II, a 5' ramp up here may help.You didn't say anything about pits forming, which one would expect with the above situation, unless there is a lot of magnesium across the whole surface. A strong chrome/nitric/fluoride deoxidizer may help to leach the Mg from the surface, but that could cause problems with Silicon smut. The ultimate solution is for those responsible to improve casting practices.
Phil Johnson
- Madison Heights, Michigan
1998
Q, A, or Comment on THIS thread -or- Start a NEW Thread