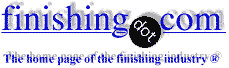
-----
Zn plate w/ tri-chrome passivation, temp at which delamination of plating will occur?
My situation is this: in our application, a stamped steel part is used as a heat shield and bracket. This part is plated with a Type2, ClassB electrodeposited Zinc plating with trivalent chrome passivation, 8 microns thick (average). In severe service environments, we have witnessed the plating peeling and flaking off the base steel part, leaving it exposed and unprotected from ensuing corrosion. This is due to it's location, which is quite close to an automotive exhaust manifold.
At what temperature can we expect the plating to peel in this fashion?
We know that tri-chrome platings degrade their corrosion performance with temperature and we also know hydrogen embrittlement baking is done up to 400F, so the plating must be robust to that temperature. No one we've spoken to has been able to give a maximum temperature limit however. Please help!
This information will guide us to one of the following options; ensure the current heat shield will not overheat in service, switch to a Zn-Ni plating (which has intrinsically higher temperature limits), switch to a stainless steel bracket and eliminate the concern with plating thermal delamination.
- Torrance, California, USA
2003
Todd,
I believe that the best solution for your problem is to apply a covering (plate) of Zn/Ni with trivalent passivate. Our tests of adhesion made with thermal shock of 1 hour to 180°C and later immersion in water, show to us that the adhesion of this Zn metal are not comparable in subjects of adhesion with the Zn/Ni plate. A process that I recommend to you is Reflectalloy ZNA and Rodip ZNX (Atotech). I feel my poor English.
A greeting,
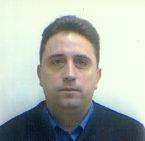
Miguel Angel Martín
surface finishing shop
Madrid, Spain
2003
Q, A, or Comment on THIS thread -or- Start a NEW Thread