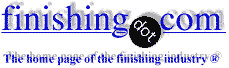
-----
Problems Electroless Nickel Plating B7 Alloy Bolts
Q. Am experiencing a problem where a local plater is having difficulty depositing electroless nickel on B7 alloy bolts (ASTM A193). The result is poor adhesion, with the plating flaking off in small pieces. I suspect the root cause of the problem to be related to a poor surface preparation/cleaning operation prior to plating? Can anyone tell me if the B7 alloy poses a problem for the electroless nickel process or should this material plate-up without issue?
Denis Moles- Foxboro, Massachusetts
2003
by Sha, Wu, & Keong
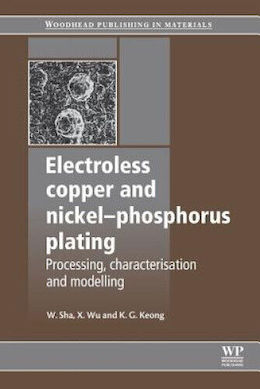
on eBay or Amazon
or AbeBooks
(affil link)
A. I have no clue as to what B7 is, but another possibility is that it is a metal that requires a strike plate before the EN.
James Watts- Navarre, Florida
2003
A. I don't know what a B7 alloy is. Assuming it is a hardened and or high strength steel it needs to be pretreated and plated under different conditions than would be acceptable for low carbon steel.
Todd Osmolski- Charlotte, North Carolina, USA
2003
A. B7 is a specification for high strength steel fasteners normally made up of 4140 or similar alloy heat treated steel. It should be given a Wood's nickel strike prior to EN and a post-bake to release hydrogen. Other preparatory steps per conventional procedures.
Guillermo MarrufoMonterrey, NL, Mexico
2003
March 5, 2014
Q. Did you ever find a solution to this problem?
I have a similar problem with plating Nickel onto ASTM A193 B7 fasteners. I believe it is due to the black coating that is on the parts following the heat treating of the 4140 steel to satisfy the B7 standard.
I remove the black material (unknown metal oxides?) with 10% HNO3 but it leaves quite a bit of smut. I assume this black smut to be elemental carbon, but 4140 is such a low-carbon alloy that I find this hard to believe as well.
4140:
Typical Chemistry
Carbon 0.42%
Silicon 0.30%
Molybdenum 0.20%
Manganese 1.00%
Chromium 1.00%
It has been suggested that the carbon smut is a result of the oil quenching process which can leave much carbon on the surface. However, I cannot verify this.
I would like to know if anyone has had a similar problem and a good solution?
My attempts were to use a HNO3 desmut and an HNO3/NH4F*HF desmut. Both worked *somewhat* but not fully (even at high concentration).
Any ideas?
- Seattle, Washington USA

Q, A, or Comment on THIS thread -or- Start a NEW Thread