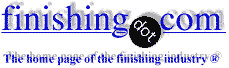
-----
Black anodizing problem
I run a small machine shop and am currently working with 6061 alloy aluminum. The problem part is a lathe turned disc one tenth thick and three inches in diameter, with several threw holes and counterbores. One side of the disc shows in the finished product and has to be cosmetically perfect. Each is carefully degreased and cleaned with acetone
⇦ on
eBay
or
Amazon
[affil link] Warning! Flammable!
, white glove treatment only. The finish side has to be a uniform black matte or semi gloss without imperfections.The first 200 parts have come back from my anodizer with a discolored pattern, mostly on the periphery of the disc. The anodizer says it is a problem with the alloy. If you hold a disc up to the angle of the light under mild magnification you can see very faint imperfections in the surface which seem to have caused the discolored areas. When I look at the same parts that were anodized several years ago and I hold them up to the light the same way, I see the same imperfections but the anodized result is good. Is this a problem with my finish work, the alloy or with the anodizer? Should I consider another type of surface finish?
Is there an anodizer out there who can help me get the cosmetic result I need? I have several hundred more parts to get finished.
- Castine, Maine, USA
2003
2003
Sight unseen you may get several conflicting answers to this one. Surface preparation comes to mind. He may be cleaning in a silicated cleaner and then alkaline etching and this will cause non-uniform finish. The machining operation may have left non-uniform "work hardening" which will give a different anodized crystal in which case the anodizer should deoxidize longer in a Ferrous based formulation - like 10 minutes at 12%/volume air agitated. Getting the current on the part may be a problem, tight racking and at least 16 volts are required. High dissolved aluminum (over 12 gm/L) in the anodizing tank can cause non-uniform oxide formation.
For a shop referral get back to me on a separate message.
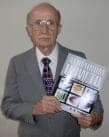
Robert H Probert
Robert H Probert Technical Services

Garner, North Carolina
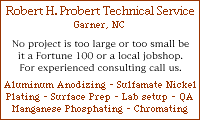
Q, A, or Comment on THIS thread -or- Start a NEW Thread