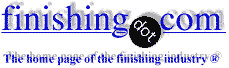
-----
Immersion Tin Plating on Aluminum: Adhesion Problem
Q. I have been asked to replicate a process that is done overseas. The cycle is as follows:
- etch
- cold water rinse
- cold water rinse
- 30% phosphoric acid
- cold water rinse
- 5% HCl
- cold water rinse
- cold water rinse
- 8 oz/gal immersion tin
- cold water rinse
- cold water rinse
- hot water rinse
The problem I'm having is adhesion.I've been told that this cycle works overseas but I've had no success.
I have tried different things like substituting nitric and chromic acid for phosphoric or adding ammonium bifluoride to the phosphoric acid but nothing seem to work.
The alloy of the Aluminum pistons is 7% tin and 93% Aluminum.
I would appreciate any suggestion.
Sincerely,
Christy H.
1998
? Please tell us your chemistry for immersion tin.
bob morrison- ormond beach, Florida
A. I looked up immersion tin in "Modern Electroplating" [on AbeBooks, eBay, or Amazon affil links] by Lowenheim. All of the formulas given use a fraction of the tin that you quoted.
M&T has an Alstan process that several people like. I think that they are Atotech now. A proprietary solution has a lot of information and some service that goes with it. I think you would have a lot better luck with one of those than with a home-brew that currently does not work.
Lowenheim's book has 34 references, and 7 formulas for home brew along with 5 pages of commentary.
James Watts- Navarre, Florida
Mr. Morrison,
I'm using the Alstan process at 8 oz/gal. I have also used it at 6 oz/gal, 4 oz/gal and 2 oz/gal but nothing has worked.
Thanks for responding.
James,
Thank you for the information, but I'm already using the Alstan 65 process. The Alstan is a great product but it just doesn't seem to work on this particular application. I don't think the Alstan is the problem.
Thank you for responding.
Sincerely,
Christy Hardin [returning]A. Customer service is supposed to come with a product, especially one from a major company.
What kind of help or excuses have you gotten?
The squeaking wheel gets the grease. Squeak louder. They can solve your problem, or they should not have sold it to you.
Personal opinion.
James Watts- Navarre, Florida
A. Lowenheim's "Electroplating" ⇦[this on eBay , Amazon, AbeBooks affil links] tells us that most immersion tin deposits are non adherent, and that the silicon bearing alloys of aluminum are the ones that work.


Tom Pullizzi
Falls Township, Pennsylvania
A. Dear Christy ,
I would recommend that you substitute the phosphoric acid with the following mixture
- 30 % by Volume Nitric Acid ( 70% )
- 20 % by Volume Sulfuric Acid (98%)
- 120 grams / litre Ammonium Bifluoride
- immersion time 30 seconds to 1.5 minutes
- rinse thoroughly and go direct into the immersion tin forget the HCl
Regards

John Tenison - Woods
- Victoria Australia
Mr.Woods,
Thank you for the suggestion. I think I might try substituting phosphoric acid with Nitric and sulfuric acid with ammonium bifluoride mixture. I'm also going to plate a stannous sulfate tin solution before going into immersion tin follow by an aqueous bronze bath. I hope this will work.
Thank you for responding.
Sincerely,
Christy Hardin [returning]1998
A. Dear Christy ,
I hope that you have success , but a reminder that if you plan to electroplate Aluminium , then before it will accept a plate it needs a immersion coat of Zinc , usually applied from an alkaline cyanide solution .
I would be concerned that if you went immediately from the zincating stage to a strongly acidic stannous sulfate tin plating bath you would dissolve the zincate before you got any tin to plate so I would recommend a coating of electroless nickel before doing any tin plating , I would further suggest using one of the low temperature electroless nickel processes , then rinse & go directly to stannous sulfate tin for electroplate .
best regards

John Tenison - Woods
- Victoria Australia
Non-electrolytic tinning of 6063-T0
Q. My company is looking to bring tinning of aluminium sections in-house for a product line, and I've been tasked with researching and designing the tinning procedure. I'm a mechanical engineer by trade however, and this is a little out of my wheelhouse.
From what I understand, we can do a direct tinning procedure using a stannate solution, however, the references I've found seem more concerned with its application with high silicon aluminium. I'm uncertain if that means it will work with a low silicon alloy such as 6063, or if that's just the more common use of the process.
As it stands I'd be happy with being directed to relevant literature on tinning processes that have been relevant in your work.
Employee - Delta, BC, Canada
November 26, 2019
Q, A, or Comment on THIS thread -or- Start a NEW Thread