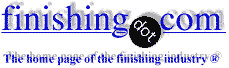
-----
How can I "refinish" stainless steel fittings?
Hi,
I want to re-process old stainless steel sanitary and hi-vacuum fittings for re-use. Of course the range of contamination and corrosion on incoming parts is potentially unlimited, but for now I'm sticking to parts with little visible corrosion or deposits. End polish of the process should be pretty fine, class 5 or 6 (?) ie: 600-800 grit, for hi-vacuum the finer the better, or in preparation for electropolishing. About %30 of the fittings are <12"^3, %30 are <24"^3, %40 >24" in at least one dimension. I'm not adverse to building my own custom "tumblers". It's very important small, blind nooks and crannies and surfaces inside corners get clean and polished, too. But I may need to protect some surfaces, knife edge and sealing surfaces, from some of the processing. I'm not sure where to begin, I'm thinking ultrasonic, vibratory, or sand blasting: ultimately I will probably need all three techniques (and electropolishing and alkali baths) to deal with the widest range of materials.
Now for a few questions: Does removing .0001" to .002" of material sound like a reasonable target to remove discoloration and renew the surfaces? If I could achieve that at .0001" per hour I would be happy for now. How would a cut of this magnitude be classified, and how could it be achieved with due regard for the blind hole factor? I suppose at some level I'm hoping my "cut" might actually count more as a polishing or burnishing. Are slurries of suspended grit sometimes used by themselves in vibratory or rolling tumblers, or in ultrasonic cleaners, which do not rely on impingement of larger objects (i.e., shot). Should I just start experimenting with walnut shell media ⇦ on eBay or Amazon [affil link] and rouge? Should I focus on vibratory, or roller types?
Thank you in advance for any help.
Jeff Miller- San Francisco, California
2003
You provided a lot of information and questions; however, not enough to make a proper decision. What is the overall size of the part(s) and size of the blind hole and/or passageway to the hole. Of the 3 processes you mentioned, the liquid system is the only one capable of reaching all the areas, but it may not have enough energy to clean up the parts properly and they will not modify the surface. The blast method may achieve good looking parts, but not the surface finish you indicated you want to achieve. Vibratory systems work well in a lot of applications, but are not good on I.D. areas unless they have easy access.

AF Kenton
retired business owner - Hatboro, Pennsylvania
2003
Q, A, or Comment on THIS thread -or- Start a NEW Thread