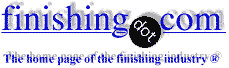
-----
Polypropylene and Sonic Welding Help Needed
2003
Q. PLEASE HELP if you can...Follow up question to letter 6696 --
We are putting together a toy and are having trouble sonic welding an injection molded cap to an extruded tube / pipe that is 1 1/2" OD with a 3/32" thickness. Both pieces are made of polypropylene.
Here is what is happening...
I have tried to sonic weld PolyPro parts and have the following finds:
1) Injection molded PP parts. No problem in sonic welding.
2) Extrusion PP tubes with PP caps turned from a solid rod. Failed to melt together, the energy director on the cap has molten, but no bonding formed between the parts.
3) Extrusion PP tubes with caps turned from the same PP tube. Still failed to melt together, the result was same as sample 2.
According to the above findings, my conclusions are:
a) The welded parts must be in same type (same grade), and most likely they should be in exactly the same material.
b) As shown in the result of sample 3, even the parts are in same material, they still can not melt together. The extrusion PP tubes I tested were sourced in local market, I am not sure what type of PP they were made of. Furthermore. if it implies that the extruded parts can not be sonic welded, I am afraid we will still have problem even changing the tube and cap to other materials (such as ABS).
Does anybody have any possible causes or solutions?
Thank You!
- Wayne, Pennsylvania, USA
2003
A. Hi Joe,
What puzzles me is that the original query came from someone living in a different State !
Anyhow, to business.
You mention that you are trying to sonically weld 3/32" PP material. Um. I am not sure but think that the power requirements for such a 'heavy' thickness would be excessive... as I believe/think that only very, very thin materials can be ultrasonically welded.
Your solution to 'welding' a cap onto a piece of pipe should be a piece of cake! You'd need a fusion welding tool which would consists of a handle, an extension rod and a metal 'T' top. The top to consist of a socket and a spigot. The socket being a hair smaller than the pipe size, the spigot being a hair larger than the cap.
The heat source in Ye Olden Days was an open flame. And if you asked a Georg Fischer distributor (of PP pipe & fittings) about their fusion tools, you'd have a better idea of what can be done, heating-wise, I mean.
The actual job on a small size piece like yours should take l0 or seconds to fuse them together but maybe 20 seconds 'in the preheated tool'. OK?
And if this saves you $l million or so, please send me a cheque, I need it ... I'm retired.
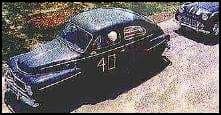
Freeman Newton [deceased]
(It is our sad duty to advise that Freeman passed away
April 21, 2012. R.I.P. old friend).
Freeman, Thank you for the response. It is greatly appreciated.
- Wayne, Pennsylvania, USA
2003
A. Hi,
I don't know what kind of ultrasonic welder you are using since you don't mention this...But the frequency of the welder makes a big difference. i.e. 10khz, 15khz, 20khz. Also, the color or magnification of your booster, Gold, Silver, Black etc. etc. also makes a huge difference. Again, I don't know what equipment you are using so this would make a big impact on your results. It sounds to me as if you don't have the right equipment. Polypropylene tends to absorb energy, not like nylon. We tend to either vibration weld, or hot plate weld (fusion) polypropylene, although we do ultrasonically weld very few PP parts effectively but we have to over weld if compared to nylon parts of the same configuration. Hope this helps a lil.
Good luck.
Automotive Under-hood components - Delavan, Wisconsin
2003
A. Hi,
In our experience, its not cost effective to sonic weld PP. If you must use PP (it is generally more corrosion resistant than ABS), you might want to consider a glue with a solvent applied to plastic first to open it up, or spin welding. On the other hand, if ABS suits your purpose, then sonic welding should work well. Sonic welding works very well with ABS and PC (both amorphous plastics) - you can even weld PC and ABS together. One the other hand, it generally doesn't work well at all with crystalline plastics such as PP and nylon.
From a theoretical point of view, it shouldn't make a difference whether the PP is injection molded or extruded; it shouldn't work at all:) Guess you got lucky.
- Shenzhen, Guangdong, China
January 31, 2008
A. To ultrasonically weld PP the weld design needs to be a shear weld not a energy director; go to Branson's or Dukane's web sites and look for shear / stud weld designs.
Rick Churchwell- Gilbert, Arizona
October 4, 2011
Q, A, or Comment on THIS thread -or- Start a NEW Thread