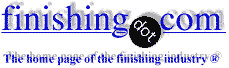
-----
Counterflow and conductivity water reduction
In order to reduce water usage, I have been tasked to design a counterflow (CF) rinse system for an existing 6-stage parts washer. I want to CF water from Stage-2 to Stage-1 and from stage-6 to stage-5. Stage-1 is an alkaline cleaner, stage-2 a clear water rinse stage-5 an iron phosphate tank and stage-6 a clear water rinse. Stages 3 - Champaign, Illinois, USA &4 are not in use. At the end of each tank (3300 gals)is a 1" plug. What do I need in the way of a pump(s), valves, etc. and if I use the existing 1" tank penetration will a 1" line be sufficient to keep the primary tanks filled? I would also like to use a conductivity meter to control both overflow pumps. How does this play into CF rinsing.
Ken Barnes
2003
I would think that a 1" line would be sufficient to provide a fill in a counterflow rinse configuration. I would suggest though, that you use a conductivity meter for the cleaner stage only. I would use a pH controller for the phosphate stage because as iron builds up in that stage, it will skew the conductivity readings.
Dan Brewerchemical process supplier - Gurnee, Illinois
2003
Counterflow means that the rinse water flows counter to the direction of flow of the work; so to move water from a higher numbered rinse tank to a lower numbered rinse tank would constitute counterflow rinsing. But in this case you are not counterflowing rinse water, you are just using what is usually called a "dragout rinse".
You should ideally use stage 3 as a 2nd rinse after cleaning, and relocate the unused stage 4 to become a second rinse after phosphatizing.Then you would have a counterflow rinse arrangement.
The problem with your current plan is that there is little hope of returning enough rinse water to the cleaner tank and phosphatizing tank to constitute a viable arrangement.
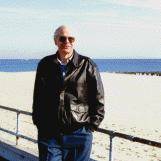
Ted Mooney, P.E.
Striving to live Aloha
(Ted can offer longterm or instant help)
finishing.com - Pine Beach, New Jersey
2003
I understand that the proposed arrangement is actually "counter-flowing" make-up water. Question 1 - Is what you are saying is that there possibly is not enough cost savings generated by doing this as opposed to the cost of plumbing? Question 2 - If both tanks are at the same fluid level and I connect a 1" line between them won't the levels stay constant in both tanks even though I am only adding water to the rinse tank? (I know I would have to monitor the chemical levels in both process tanks with titration and pH control and to do some homework on the level of drag-out for each process tank.) I am not an engineer or scientist.
Ken Barnes- Champaign, Illinois, USA
2003
Right, the dragout and evaporation losses in the process tanks will be so low that almost nothing will be returned to them. Easier may be to leave things piped as they are, and put an electronic level control on the process tanks which activates a small metering pump to refill them with water from the dragout tanks.
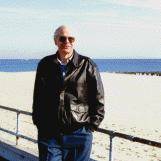
Ted Mooney, P.E.
Striving to live Aloha
(Ted can offer longterm or instant help)
finishing.com - Pine Beach, New Jersey
2003
In my experience a 1" connection in a 6 stage counterflow rise system will result in the first and 2nd tank in the system overflowing , unless the levels of each rinse tank can be made lower , or as you suggest pumping from one rinse tank to the next. As important is the degree of agitation you have in each tank ,running water volume required is substantially less with agitation. Also depending on configuration of the work you are processing a spray rinse introducing your water into each tank can effectively reduce water volume required. Of course this only works if you are pumping as well.
Raymond Sebba- Cape Town, South Africa
2003
Q, A, or Comment on THIS thread -or- Start a NEW Thread