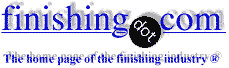
-----
Wiping problems in Hot-Dip Tinning of Wire
Q. I am searching for alternative 'wipes' for wire after a hot dip tin plate. Presently cotton rope is the medium used.
Diane A. Mancini- Oxford, Massachusetts
2001
Air wipes for hot dip tinning of wire
2003Q. Hi there,
I use a hot-dip type process for tinning of copper wire. My problem lies in the wiping of copper wire soon after it comes out of the tin bath. The wiping material is of silicone rubber and the wire passes thru the rubber. The rubber needs to be replaced every 10 minutes. It can't be done that way every time. I wish to change it. my questions are:
1) Should I change my entire process to Electroplating? Is it better in quality and quantity?
2) Or should I change the material for wiping?
3) Where am I going wrong?
Please reply back,
Soorya- Bangalore, India
2003
A. 1) Hi Soorya. There is an old saying in engineering practice as well as metal finishing: "The chemistry must precede the engineering". In your case this means you don't switch from hot dipping to electroplating because of engineering difficulties in building the equipment; if hot dipping is preferable for your function, you stick with it (but see letter 1797, "Hot dip tinning vs. tin electroplating") for some comparisons.
2) UHMPE will probably outlast rubber, but what you may need is "air wipes". In this case the wire is not supposed to actually touch anything; rather it passes through the center of a cylinder which is perforated to blow air across the wire to wipe it, and the wear-resistant material is selected just for the incidental contact.
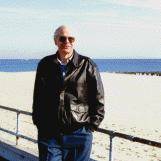
Ted Mooney, P.E.
Striving to live Aloha
(Ted can offer longterm or instant help)
finishing.com - Pine Beach, New Jersey
Thanks for that wonderful suggestion. I will try it right away! More doubts ...
Q. 1. Should hot air be blown around the wire, otherwise tin gets solidified.
2. Can I control the thickness of tin coating by varying the speed of the air being blown?
3. The air has to be blown normal to the wire. Otherwise the coating will be uneven.-- Is this right?
Awaiting for your reply; thanks once again.
Soorya [returning]- Bangalore, India
2003
A. Hi again. I've never designed these air wipes, I'm only bought them and seen them. They looked like a tube or cylinder less than an inch long and an inch in inside diameter. A compressed air hose was connected somewhere on the outside diameter. They were perforated all around the inside diameter with a dozen or so holes. I believe that the drillings were probably not at right angles, but at some slanted angle so they tended to continually push the molten tin back. Look up "air-wipes" on the Internet and you'll immediately see them. Best of luck.
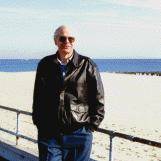
Ted Mooney, P.E.
Striving to live Aloha
(Ted can offer longterm or instant help)
finishing.com - Pine Beach, New Jersey
2003
Multiple threads merged: please forgive chronology errors and repetition 🙂
How to wipe hot dip tin?
Q. I work in a hot dip tin process, we process steel wire. my question is what is the best way to mechanical wipe tin from the wire. I have tried many different wipe but none seem to work well. There is still bumps on the wire and white streaks. Any help would be appreciated.
Eric Wrightproduction manager plating - Elizabethton, Tennessee, USA
2007
A. Use teflon coated, woven fiberglass tape. Just stretch the tape across the tin pot and thread the wire through it. You may need several thicknesses, spaced 1/2" or so apart.
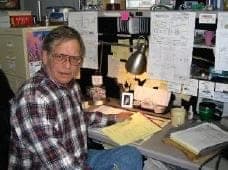
Jeffrey Holmes, CEF
Spartanburg, South Carolina
2007
Q, A, or Comment on THIS thread -or- Start a NEW Thread