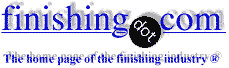
-----
What is the best material to use for a load bar, or work bar
Q. We are looking into designing a different carrier or hood for our anodizing racking system.We currently use a stainless steel framework with a 2" aluminum rod as our carrier work bar.We hang our racks from this work bar and this carrier or load is placed into the anodizing bath for anodizing. In our new design we were intending to use a 2" by 4" aluminum bar with stainless framework.Recently it was suggested that we consider a 2"by 4" Titanium clad aluminum bar. Does anyone have a system that uses,a titanium a work bar or have information regarding the use of titanium for a work bar in an anodizing system? We use both titanium and aluminum in our racks but not in such a heavy duty area as the work or load bar.
R. Scott Ebert- Fridley, Minnesota, USA
2003
A. Scott,
I'm long removed from this subject but think if you spend the money to get titanium clad aluminum go the extra mile and get titanium clad copper. Copper will carry 1000 amps per sq. in. Are you at Spec Plating?
Jon Quirt- Minneapolis, Minnesota
2003
2003
A. Jon has a good point, if you're going to bear the cost of cladding, use copper to make the members small.
Less expensive constructions include all stainless steel (but it has very low current carrying capacity), and aluminum (which gets dingy looking as well as hard to maintain fairly quickly.
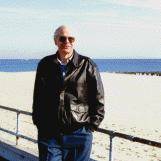
Ted Mooney, P.E.
Striving to live Aloha
(Ted can offer longterm or instant help)
finishing.com - Pine Beach, New Jersey
Q. Ted are you suggesting a stainless work bar to hold the anodizing work? This would be the electrified bar that sets in the electrical connections, over the anodizing tank with the work to be anodized in the ano solution. We currently use aluminum,and originally that was the recommendation of our consultants. The project has been on hold for awhile. Now with new members in the design committee someone got some suggestion that titanium would be better, and if I understand you, Stainless is also a good option. Please respond.
R. Scott Ebert [returning]- Fridley, Minnesota, USA
2003
![]() |
They are talking about flight bars, not racks. NO, bare SS will not last on a rack. James Watts- Navarre, Florida 2003 2003 Stainless is a highly suitable material of construction in most ways but, as mentioned, it offers very low conductivity. I recently worked on a Japanese anodizing line with all-stainless work bars where the manufacturer rated the stainless for 200 A / sq. in. (although I've never sized it for over 100 A / sq.in.). Depending on the current you need to carry, and whether you have bussed the workbar from both ends, stainless construction might be practical for your situation, but you would still need something with better conductivity at the contact points. ![]() Ted Mooney, P.E. Striving to live Aloha (Ted can offer longterm or instant help) finishing.com - Pine Beach, New Jersey 2003 Re Anodizing work bars: I have experience with Al, Ni(EN)-plated Al, Cu & Ti-clad Cu anode bars up to 6000 amp capacity. Stainless steel & Ti should only be used for support structure, Ni-plated Al is suitable for an alkaline electrocleaner workbar, bare Al needs daily cleaning when used as anode bar, Cu (bare) is the best anode workbar (although an argument could be made for gold plating over a Ni barrier layer). While my experience is on manual lines, all automated lines I have seen had Cu workbars with SS support. Ti-clad Cu anode bars suffer from the poor conductivity of the thin Ti skin, and are basically about as useful as Ti racks: Only suitable for small parts requiring small currents, and necessitating a slightly higher voltage. I have one such rectangular bar with dimples on the two top edges where the brass hooks of fully loaded anodize racks left impressions in the overheated Ti & underlying Cu. A round bar has similar but shallower indentations, presumably due to larger contact areas. Please keep in mind the electrical conductivities of each material (not to mention the surface oxides that may form). Some values: Metal conductivity, % IACS Silver 106 - Goleta, California ![]() Rest in peace, Ken. Thank you for your hard work which the finishing world, and we at finishing.com, continue to benefit from. |
Q. Greetings,
I am currently in the infancy stage of setting up Types I, II, & III anodize in our processing line and was wondering what would the pros and cons be of using Titanium busbars in place of Copper. For a 7' long, 1" dia copper busbar, I'm used to seeing ampacity of about 500, but what would the benefits of Titanium be? I understand the wear and tear would be minimized with Titanium and overall less work on the tank, but are there any drawbacks from using this material? Cost is obviously going to be higher.
Any input would be appreciated.
Regards,
- Phoenix, Arizona
April 22, 2016
A. Hi Alex. You are calling this item a "busbar", but I would call it a "work bar", "load bar" or "flight bar" if the work hangs from it, or a "cathode bar" if the cathodes hang from it. In the plating & anodizing field, we have long considered the ampacity of copper to be 1000 A /sq in. of cross section, making the ampacity of a 1" dia. copper bar 785 Amps.
Unfortunately, the allowable current in titanium would be at absolute most, only about 5-10% of this ... Ken Vlach, above, suggests 1-3% depending on the type of titanium. The short answer is that you can't use titanium for this.
Regards,
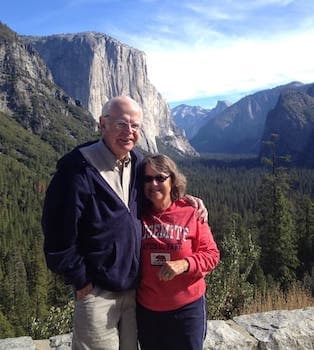
Ted Mooney, P.E. RET
Striving to live Aloha
(Ted can offer longterm or instant help)
finishing.com - Pine Beach, New Jersey
April 2016
Q, A, or Comment on THIS thread -or- Start a NEW Thread