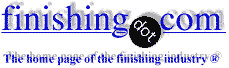
-----
Gold plating of aluminum
finishing.com is possible thanks to our supporting advertisers, including:
Current question and answers:
Q. Greetings,
I have an aluminum part that goes through two plating cycles, first electroless nickel and then hard gold, and want to mask the plating to limit gold deposited to only a certain area.
Is it possible to use MICCROShield or other masking?
- Belmont, Massachusetts
December 14, 2020
A. Hi Jeff. I think most maskants can withstand a hard gold plating cycle and wouldn't expect much trouble there. But even if you already know it, we should mention for other readers following the discussion that the electroless nickel will probably passivate during the masking operation, so a Wood's Nickel Strike will probably be required before the gold plating.
Luck & Regards,
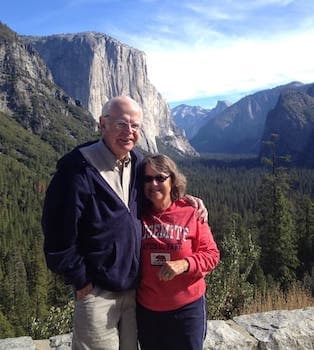
Ted Mooney, P.E. RET
Striving to live Aloha
(Ted can offer longterm or instant help)
finishing.com - Pine Beach, New Jersey
December 2020
Q. Thanks Ted, got it.
Could we mask before cleaning and the electroless nickel bath, with a gold flash right after electroless nickel to preclude passivation or oxidation, and then go to the hard gold. Does gold flash perform a similar function as Wood's Nickel Strike and is the cost comparable? Also, is a hard gold bath typically acidic, alkaline, or neutral?
- Belmont, Massachusetts
December 15, 2020
by Reid & Goldie
-- hard to find & expensive; if you see a copy cheap, act fast!
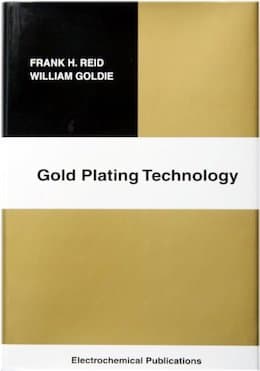
on eBay or Amazon
or AbeBooks
(affil link)
A. Hi again. You should normally clean before & after masking. Many electroless nickel baths are quite hot and aggressive, so reliable masking may be more difficult, but yes, you can mask before any plating.
Yes a gold strike is very useful not just for activation but to prevent immersion plating and as a sewer to protect your main gold tank from contamination. It's probably not as powerful an activating agent as Wood's Nickel, but probably more than adequate if you're going there right after electroless nickel rather than stopping to mask.
I'm not a gold plating expert, but I understand that you can get good hardness from any of the three, but you need a little (probably less than 1/2%) of cobalt or nickel for good hardness. Book knowledge says acid golds are easiest to operate and most robust.
Luck & Regards,
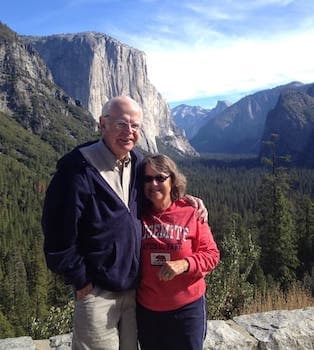
Ted Mooney, P.E. RET
Striving to live Aloha
(Ted can offer longterm or instant help)
finishing.com - Pine Beach, New Jersey
⇩ Related postings, oldest first ⇩
Q. For optimum electrical conductivity, I need to hard gold plate an aluminum vacuum plate (.5" x 8" x 8") that has been lapped for a very flat and smooth surface on the top. The top of the plate has 300 pin holes (.025) thru the plate. I need to plug up 200 of the holes prior to hard gold plating. The plate is used in a clean room.
Can you advise what method of fill will be compatible with the nickel / gold plating process? I'm hoping not to have to use alum .025 dowels.
Thanks, Brent
- San Diego, California
2000
A. That is one nasty job. So tiny and so many in a relatively small area.
I would check to see if any vendor makes a "pull plug" out of soft silicone. A 0.030 would probably be a proper size.
You can get taper plugs that small, but they are not easy to install.
You can take vinyl tubing, about .030 OD, cut the ends on a taper at appropriate lengths and pull these thru. They work, very well, but are more time consuming than a pull plug.
Do you absolutely have to plug them, Could 0.001 oversize and plated do the same thing? I assume that they cannot be plated and chased afterwards because of edge burrs.
- Navarre, Florida
2000
Q. I don't have to plug the aluminum block before gold plating.
So, can you advise a gold type filler to fill the holes after the plate has been gold plated?
thanks, Brent
- San Diego, California
2000
A. Sorry, I don't understand what you are looking for. Please explain what you mean by "I need to plug up 200 of the holes prior to hard gold plating" but "I don't have to plug the aluminum block before gold plating". I guess you're saying that 200 of the holes have to be permanently "blocked" and after reconsideration it really doesn't matter that it be done before plating? Maybe a reader who has done something similar will have more insight :-)
I'm a little lost, Brent. Sorry :-(
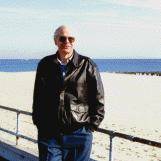
Ted Mooney, P.E.
Striving to live Aloha
(Ted can offer longterm or instant help)
finishing.com - Pine Beach, New Jersey
2000
A. Me too.
James Watts- Navarre, Florida
2000
Gold plating aluminum with no nickel layer
Q. I would like to gold plate an ultra high vacuum electron spectrometer made entirely out of aluminum. I have heard of gold plating aluminum using a nickel substrate but nickel is to be avoided as it is a magnetic material and thus inappropriate for electron spectroscopy. The reason I would like to gold plate the spectrometer is to get rid of possible charge up effects due to the non-conducting layer of aluminum oxide that can form.
Theo ZourosKansas State University - Manhattan, Kansas
2003
A. Hi Theo. This should not be a problem. The aluminum can be zincated, then copper plated, then gold plated. Although gold and copper will interdiffuse at high temperature over time, if the part is not hot the plating should meet your needs. Good luck.
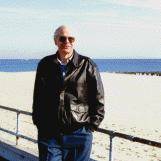
Ted Mooney, P.E.
Striving to live Aloha
(Ted can offer longterm or instant help)
finishing.com - Pine Beach, New Jersey
2003
A. High phosphorus electroless nickel deposits are non-magnetic unless heated to over 250 °C.
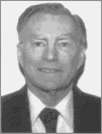
Don Baudrand
Consultant - Poulsbo, Washington
(Don is co-author of "Plating on Plastics" [on Amazon or AbeBooks affil links]
and "Plating ABS Plastics" [on Amazon or eBay or AbeBooks affil links])
2003
Gold plating an aluminum sword
Q. I am an artist, and I have been crafting a decorative sword for a while now. The sword is very important to me, because it symbolizes me. I have been reinventing the metal working process during the sword's construction. The blade is made of construction grade steel and has been chrome plated. I cast an aluminum handle around the base of the blade. When the blade was plated the electrode had to be attached to the aluminum handle. Unfortunately, the current which passed through the handle oxidized the piece of the handle below the electrode. I am in the process of trying to repair the oxidization right now. Next, I want specific regions of the handle to be gold plated, but I am concerned that the handle, or worse the blade, will be damaged when electricity passes through the sword. I would like to know a few things. I want to do as much of the work as possible. Is there a way I could plate the handle safely myself? How can I clean the residue from the handle if it needs to be plated professionally? I would also like to do this as cheaply as possible. Any suggestions y'all have would be greatly appreciated.
Thank you:)
artist - Plano, Texas
2003
Multiple threads merged: please forgive chronology errors and repetition 🙂
Gold plating on electroless nickel plated aluminum
Q. Some electroless nickel plated aluminum parts must be done gold plating. The parts have been drilled after EN, that is to say the base aluminum is exposed too.
Are there any methods to do gold plating on the parts? Any suggestion.
Plating Shop - Vancouver, BC, Canada
2005
A. Exposed aluminum immediately forms an oxide layer that impedes further plating or coating. EN also forms an oxide layer that does the same thing. Both have to be activated to receive a gold plate but the sequence and chemicals are different. It is better to EN plate after drilling, then you'd have a single metal to plate onto.
Guillermo MarrufoMonterrey, NL, Mexico
2005
Cyanide gold plate directly on zincate?
Q. Is is possible to directly plate cyanide gold directly onto zincated aluminium? I'm trying to avoid bringing up a CuCN bath we used to use on the zincate. We've done EN directly on the zincate with beautiful plating results but then I've had problems etching that nickel out of the finished hollow electroform.
I'm hoping that alum-zincate-pure gold-acid copper is possible, but I can't find an online reference saying yeah or neah.
Thanks,
nrao - Charlottesville, Virginia
2006
? You need to clarify. Gold Acid Copper? Do you mean acid gold and/or acid copper solution?
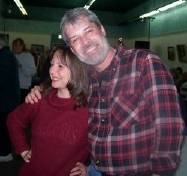
Trent Kaufman
electroplater - Galva, Illinois
2006
A. Hello Gerry,
I understood part of the question, so I'll answer that. Plating gold directly on zincated aluminum is a bad idea. The zincate will migrate through the gold in no time and affect the appearance of the part. If gold is to be the final finish you will need a barrier plate such as Ni. Without Ni or a sufficient diffusion barrier even the copper will migrate through the gold layer. Acid copper is widely used in electroforming, but you may want to consider a copper strike before acid copper either Cn or alkaline to ensure good adhesion. Good Luck!
process engineer - Malone, New York
2006
2006
Q. My English was a little confusing there :-)
To clarify, I'd be starting with an Alum. mandrel which is eventually etched out of the finished piece.
We always zincate the Alum. before further plating. In the past we would zincate the mandrel, CuCN flash, plate a few hundred microinches of gold, CuCN flash over the gold, and then go into our acid Cu to build up copper for the bulk of the part.
After the finished piece is machined we etch out the alum-zn-cu, leaving the gold plate as the interior working surface of a microwave waveguide structure. (alum-zn come out with HCl or NaOH, little HNO3 to get the copper).
Recently we've experimented with: Alum mandrel - zincate - EN - gold - straight into acid copper. This seems to work generally OK, but I think I've had trouble etching out the nickel, EN. (it's an interior surface, hard to inspect)
My thought was that if I could gold plate directly on Zn then my etch out would just be aluminum-zinc. IF the Zinc-Gold dissolving happens fairly slowly I could live with it, since the Zn will be etched out within 3-4 weeks anyhow. I realize the Zn-gold may have "fingered" together some and when the Zn is etched away I'll have roughened the gold surface some, but how much? I don't need a mirror, just a decent gold surface to finish the waveguide interior.
Maybe I should bite the bullet and just set up a CuCN bath, but the acid copper seems to plate fine directly onto gold, so if I can just get a plateable but easily dissolved flash over the alum or zinc we'll be in business.
Thanks for the replies.
- Charlottesville, Virginia
2006
Did a quick experiment re plating gold directly on zincate.
I took a thin alum. plate, few square inches, zincated it on one side (other side masked with plastic).
I went into my CN-gold with that and plated on .0005" of gold.
Good news is, it plated nicely from the first second, no signs of any strangeness at all. Went in hot, hope I'm not contaminating the bath with zinc at all. But the plated gold came out nice as anything.
I then etched the Alum-zinc away with HCl to get a rare look at the "inside" of some plating. That inside surface (was against the zinc layer) looked nice, but had a "brassy" look. So possibly after just 2-3 hours in contact with zinc, at bath and ambient temps, we've had enough zinc go into the gold to change it's appearance.
I might take this a little further, let the next test piece set at room temperature for 3-4 weeks and try elevated temp also.
- Charlottesville, Virginia
Q. Hi,
I have a similar application to above where the gold plated aluminum cannot be magnetic. It is also in ultra high vacuum, so I would worry that the high vapor pressure of zinc and phosphates would contaminate our system. Can aluminum be gold plated without zincate and nickel preplate processes?
- Lemont, Illinois
February 5, 2010
A. Hi, Tony. Atotech offers (or used to offer) their Alstan system for metallizing aluminum in lieu of zincating. The trade name is a play on "all tin". But I can't guarantee that there is no zinc or phosphates or danger of sublimation; you'd need to contact them. Good luck.
Regards,
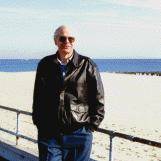
Ted Mooney, P.E.
Striving to live Aloha
(Ted can offer longterm or instant help)
finishing.com - Pine Beach, New Jersey
February 2010
Black spots on gold and nickel plated aluminium
Q. Our company has recently changed back to a Schlotter medium phosphorous bright electroless Nickel from another medium phos bright EN due to problems with step plating in the nickel on Aluminium. We could not consistently dummy the tank to eradicate this issue.
The new EN gives a brilliant finish with no apparent marks until we put soft bondable gold over it. At this point the gold shows spots which look black but when examined with the XRF are in fact areas of no gold.The EN is not pitted in any way where the spots are. These spots are no more than 0.5 mm dia. generally and randomly distributed over the part. They also do not have a defined edge to the spots. We are putting 12 - 15 microns of Ni on the aluminium followed by 0.5 - 1.0 microns of gold.
We do not see this effect with our hi phosphorous EN nor indeed have I ever seen this effect before. If we decrease the amount of time in the electrolytic activator just before the gold, the situation gets worse. If we increase the time in the activator it gets better but we are now at 20 mins (6 mins is standard) and although improved, is still there. If we increase the time too much then there will be the worry of pitting the EN.
Any thoughts would be greatly appreciated.
Engineering and plating shop employee - Honiton, Devon, England
July 25, 2013
A. Steve, there is some more information needed. First of all, I would recommend reading MIL-G-45204 [link is to free spec spec at Defense Logistics Agency, dla.mil] and MIL-C-26074 [⇦ this spec on DLA]. You may find all of your questions answered. Is there any chance the process is overloaded? The step plating should have triggered an investigation into overloading. Next, you'll need a process map to understand C&E and inputs. Is the current process electrolytic or electroless gold? Is there any embrittlement relief or intermediate steps before the gold but after the nickel? Your message almost made it sound as if there is nothing wrong with the new EN and all you are seeing is voids in the gold. If that is the case you can look into drag-out and rinsing. The 20 minute step you describe is not a step I am familiar with. All signs seem to point to overloading but when you are using such a thin gold layer it could be something else, take a look at Mil-G-45204 and you'll see what I mean. I would think a good process would be EN, drag-out, rinse (fast), gold strike, gold. That is the process I am familiar with. One big problem is when people plate the nickel and then let the nickel dry. If the nickel dries just a tiny bit, it can cause spots. This could be causing your problem. The nickel must not dry if you want to use the process I described. Another thing you need to do is verify the EN coating is good. You can do that by destructive testing. There's no sense in curing a gold problem if you really have a nickel or pre-treatment problem. One last thing is to blow dry the parts with dry N2 immediately after gold and rinsing. You can also use IPA rinses and hot rinses after the gold, it's highly recommended, but based on your message it sounds like the gold not being dried properly is not the problem here but it is certainly worth looking into because if you don't dry the parts quickly and properly after gold, you will see a similar spotting condition. Good luck.
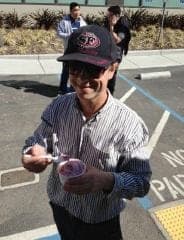
Blake Kneedler
Feather Hollow Eng. - Stockton, California
July 29, 2013
Q. I need a clarification regarding gold plating process,
Like one of our products is AL 6061 T6/T651, The requirement for the surface finish is in Gold plating. Our engineers specified gold plating 0.25 microns over copper & nickel plating. They have not specified whether the pre coating is electro or electroless and the coating thickness, standards to be referenced, etc.
I need to know is there any difficulty in this process, and how do I specify the finish details in clear manner to avoid such discrepancy like visual or functional?
- Chennai, tamilnadu, India
August 13, 2015
A. Hi Bharathi. Unfortunately, one must acquire a good understanding both of finishing processes & the needs of the specific product in order to do what you'd like. There isn't a "standard" type of plating; rather, the plating is designed and specified for the particular application.
0.25 microns of gold is rather little, so the underlying nickel plating will definitely be functional and critical. Some of the first things you need to determine include the function of the plating, and the environment to which it will be subjected. Is the gold for decorative purposes or for low contact resistance electronic application? Then, what type of gold plating do you need (hard gold, soft, solderable, etc.). Then what kind of nickel plating. Yes, there are certainly ASM, ASTM, ISO, and other plating specs which you'll want to reference -- but you can't choose them until you've clearly delineated the general requirements of the plating. Good luck.
Regards,
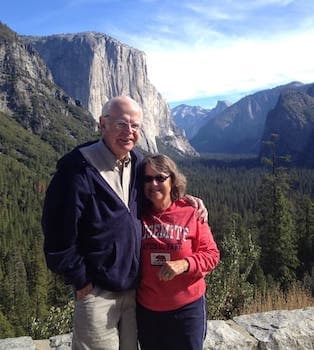
Ted Mooney, P.E. RET
Striving to live Aloha
(Ted can offer longterm or instant help)
finishing.com - Pine Beach, New Jersey
August 2015
November 18, 2017
Q. I have a 1957 Chevy Bel air. The grille as well as the Vee on the hood and trunk is gold anodized aluminum, which is not like bright gold.
Can these pieces be gold plated in bright shiny gold?
Glenn Marshall- Tillatoba, Mississippi USA
A. Hi Glenn. Yes, it can be done. The anodizing must be stripped, then the aluminum zincated, plated with something compatible with zincate (possibly cyanide copper), then nickel plated, then chrome plated.
If you're going to gold plate or chrome plate something though, it's better to not make it out of aluminum if practical. You would have been better off starting with steel or zinc diecast parts if available. Happy restoration!
If you've got the money for full restoration, Hammer & Dolly in Traverse City Michigan just finished a beautiful 1956 Nomad per their Facebook page. Owner Adam Hammer is the son of Chris Hammer, president of Hill-Cross Company [a finishing.com supporting advertiser] and grandson of Herm Hammer -- co-founder of Hill-Cross, along with (small world) Donald Wood, the inventor of the Wood's Nickel Strike process.
Regards,
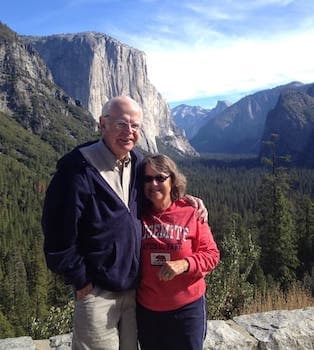
Ted Mooney, P.E. RET
Striving to live Aloha
(Ted can offer longterm or instant help)
finishing.com - Pine Beach, New Jersey
November 2017
November 25, 2017
A. Hi Glenn.
It can be done. But if you intend to use the car rather than stand it in a showroom you should know that roads have one of the most corrosive environments known to plating. Thin gold is porous and will rapidly fail. Sufficiently thick gold say 5+ microns is going to cost serious money.
Back in the 1950s Daimler produced a gold plated model for Lady Docker.
At that time gold was about $35/oz
It's not now!
Most anodizing shops can offer a very good looking gold finish and a clear lacquer can provide the shine.
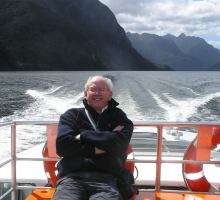
Geoff Smith
Hampshire, England
A. For perhaps the first time in my memory I have to disagree with my super learned colleague, Geoff. Nickel is not expensive and it is the nickel that provides most of the corrosion resistance in a decorative nickel-chrome or nickel-gold plating process. But again, steel or diecast zinc is a better starting point for gold plating than aluminum.
Regards,
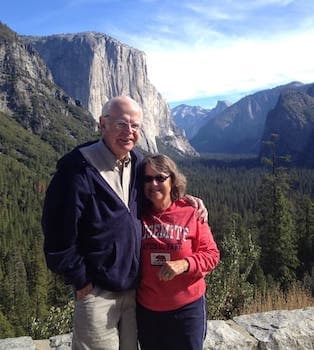
Ted Mooney, P.E. RET
Striving to live Aloha
(Ted can offer longterm or instant help)
finishing.com - Pine Beach, New Jersey
January 2020
Q. I need to gold plate one side of an aluminum plate, probably 6061. This is fairly large, about 2' x 4'. The plated surface will be inside a high vacuum environment so I need to consider using only high vacuum friendly materials. This plate is to be an x-ray generating surface and will be absorbing a high energy level of electrons. The plate will be full of water passages and be actively cooled but there will be a high energy transferred through the plating. The gold needs to be around 0.001" thick as plated. The finish is not important, the gold hardness is not important. The surface temperature should remain under 100 °C. Other than the high vacuum there should not be any other restrictions to the materials used under the gold. Can anyone recommend an appropriate plating process and even a plating service that could perform this for us? Thanks very much for any input.
John Drenter- Davenport, Iowa, USA
December 13, 2019
Q. I need to apply a gold plating to pure aluminium (99.999%) for a piece of scientific equipment to be used at very low temperatures.
I understand I will probably first have to zincate the aluminum, and then will have to plate with another metal before gold. I would, however, like to avoid nickel for my application. I was thinking about plating copper; would that work?
In the end, I want to end up with a bright, mirror-like surface in gold.
I have the gold plating solution (pen or bath). I talked to the supplier, but they say they don't really do aluminum plating because it is too much trouble and the zincate solution which they do sell has poor adhesion and is only suitable for decorative items.
Any recommendations?
Thanks!
- Lausanne, Switzerland
October 20, 2020
A. Hi Maarten. Most anything is possible, but I'll mention a couple of things which you may want to consider...
If corrosion resistance is an issue, it's hard to afford enough gold plating to reliably prevent it -- nickel plating often offers the bulk of the corrosion resistance; it's hard to get gold "bright, mirror-like" without an underlayer of something bright and mirror-like, although cobalt plating or white bronze might do; diffusion of copper into gold is an issue if there is no barrier layer between them, although the super low temperatures may greatly slow it; there might be a coefficient of expansion issue that causes cracking or adhesion problems at very low temperatures.
Your question becomes more interesting and people can be more helpful if you tell us more details on what you're doing -- for example, why you want to avoid nickel plating because if you're doing it to avoid skin allergies, it's possible that cobalt plating may prove just as bad. Plus, if that's the only reason to avoid nickel, you could probably electroless nickel plate the zincate and thereby preclude the use of cyanide in the copper plating. Does "very low temperature" imply liquid gas temperatures? Thanks.
Luck & Regards,
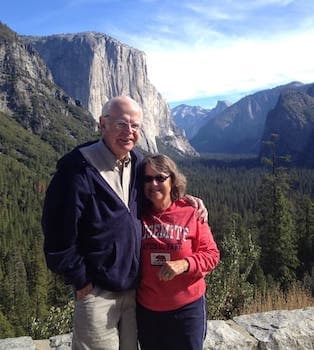
Ted Mooney, P.E. RET
Striving to live Aloha
(Ted can offer longterm or instant help)
finishing.com - Pine Beach, New Jersey
October 2020
October 21, 2020
by C W Zanariah Ngah
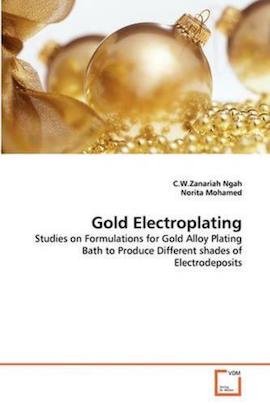
on eBay or Amazon
or AbeBooks
(affil link)
Q. Hi Ted. Thank you for your response. I will give some more details.
When I say "very low temperatures", I mean VERY low. Less than one degree away from absolute zero. At such a low temperature, aluminum is a superconductor (which is what I want and it is why I am using very pure aluminum).
The piece that I need to plate is a small, aluminum box. I will be doing an experiment inside this box that requires that all magnetic fields are excluded (the superconducting aluminum will do that). The magnetism is why I do not want to use nickel (and this would be a problem with cobalt as well).
I did read earlier in this thread that high phosphorus electroless nickel deposits are non-magnetic, but I worry there may be a difference between "should be non-magnetic" and "definitely is non-magnetic".
I need a reflective surface because it is difficult to keep things as cold as I need them to be. Something with a dull surface will warm up due to radiation from any source, whereas something with a bright surface reflects the radiation and stays cold. Most everything else in this cold environment is made of gold plated oxygen free copper that is well suited for this.
I'm not really worried about corrosion resistance as there should be no contact with anything corrosive.
While in use, the piece will be in vacuum. When not in use, it will be stored in air at room temperature. In any case, I will only handle it with gloves.
You are right of course that thermal expansion/contraction can be an issue. At the moment, I am trying to get an idea of what materials could be plated. When I have an idea of which materials may work, I can look specifically into their coefficients of thermal expansion.
Any further advice you can offer is much appreciated.
- Lausanne, Switzerland
A. Thanks for the details, Maarten -- sounds like very interesting work!
I think the sequence: zincate, cyanide copper strike, heavy bright acid copper plate, heavy gold plate sounds promising. Strictly theoretical possibility: If it still results in cracking due to thermal expansion issues, it might be possible to either anneal the copper then bright dip it before the gold plating or deposit dull soft copper and bright dip it before the gold plating.
Luck & Regards,
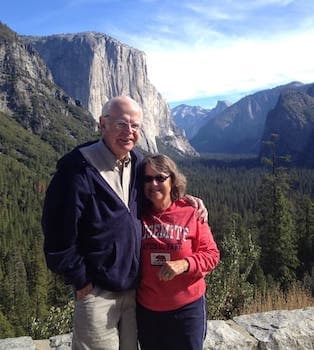
Ted Mooney, P.E. RET
Striving to live Aloha
(Ted can offer longterm or instant help)
finishing.com - Pine Beach, New Jersey
October 2020
A. Hi Maarten,
Wonder if you have considered sputtering or thermal evaporation for depositing gold on aluminum? It is pretty straightforward. Adhesion may not be a problem. If it is, a thin - less than a micron- layer of Ti or Cr would solve it. Good reflectivity could be obtained if aluminum is polished to required brightness before depositing as PVD coatings are conformal. You may have to tackle the geometry of the Al box.
Your experiment at zero B and near zero T should be something special and interesting. Good luck!
Bangalore Plasmatek - Bangalore Karnataka India
October 22, 2020
Q, A, or Comment on THIS thread -or- Start a NEW Thread