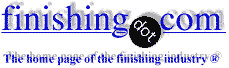
-----
Passivation of Carbon/Tool Steel
Q. We mold various rubber and plastic parts. Some of the molds we can sand blast, but some must be cleaned using a combination of water and beads. The molds are carbon steel/tool steel, and after cleaning them, we use chromic acid to "passivate" the surface to prevent corrosion during storage.
We would very much like to find a replacement for the chromic acid. Would citric acid or nitric acid work for this application? Is there anything else that someone can reccommmend. We cannot use anything that leaves a coating on the mold.
Thank you in advance.
Joyce Wagner- Ashland, Ohio
2003
![]() |
A. Carbon steel cannot be "passivated", unfortunately. You can search this site to see ways to improve the corrosion resistance of carbon steel, but citric or nitric acid are not going to help you. You can get in real trouble if you put it in nitric acid! ![]() ![]() Lee Kremer Stellar Solutions, Inc. ![]() McHenry, Illinois ![]() 2003 ---- Ed. note: There is a semantics issue here, so we ought to re-order the words in Lee's response to something like "citric acid and nitric acid cannot be used to passivate carbon steel" ... because although those chemicals are used in the ASTM A967 process for "passivation of stainless steel" the word 'passivate' has other meanings to other people: to zinc & cadmium platers and galvanizers in can mean chromate conversion coating, to phosphatizers it can mean a final dip in a chrome-bearing or other post-treatment rinse, to steam boiler engineers it can mean a coating on steel components achieved by proper operating conditions which slows corrosion, etc. A. Your procedures are a bit unusual and have maybe discouraged suggestions. Are you abrasive blasting to remove rubber residue or rust? I have never heard of chromic acid being used on these materials. Two traditional coatings for this purpose are hard chromium and electroless nickel (heat treated for hardness) plating. Either will reduce wear, adhesion and rusting. Ion implantation using Mo or Ta was recommended for improving the corrosion resistance and hardness of S7 tool steel in an ASM Int. forum. [Nitrogen implantation is commonly used to improve hardness, but usually only on specific alloys and not for corrosion resistance.] For uncoated molds, a dilute phosphoric acid-based cleaner should remove rust and slightly passivate the surface. Coated surfaces don't require any acid. In any event, quit sand blasting; it encourages adhesion of rubber and rusting of uncoated steel (microscopic roughness) and might damage any coating. The water+ beads blast is probably OK, or its pressure can be adjusted to only remove rubber. Maybe examine surfaces under magnification to verify. The links below should provide you with a choice of metal finishing jobshops and chemical suppliers within a reasonable distance. Ken Vlach [deceased]- Goleta, California ![]() Rest in peace, Ken. Thank you for your hard work which the finishing world, and we at finishing.com, continue to benefit from. 2003 |
A. About 20 years ago I was involved in "passivating" carbon steel. We did the work for the nuclear industry. The process details were provided by the customer. I don't have any information left in my records, but from memory I recall the process used a solution containing sodium nitrate ⇦ on Amazon [affil link] and sodium hydroxide and was heated. Maybe somebody else has more information about this process.
Thomas Kemp- Erie, Pennsylvania, USA
2003
A. If mold is not very big it can be passivated by high-voltage electropolishing process for few minutes in special solution of salts. The surface will become slightly yellow due to oxide film. Our experiments show that such film protects surface agains rusting.
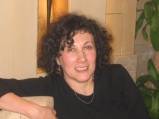
Anna Berkovich
Russamer Lab

Pittsburgh, Pennsylvania
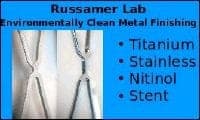
2003
Discoloration of Chrome Plated Parts after Citric Passivation
March 11, 2020Q. First let me describe the part and its processes in detail, and then describe what's happened.
Part: Medical Drill Bit
Material: AISI D2 Steel, Annealed, 48Rc, Chromimum content 11.4% min, ASTM A681
[withdrawn]
Processes Prior to Citric Passivation:
1) Machined (turned)
2) EDM Wire Cut
3) Bending Process to Straighten Parts
4) Ultrasonic Cleaning
5) Hand Deburr
6) Heat-treat (Vacuum Furnace, Hydrogen Atmosphere, Per AMSH6875 and AMS2759/5)
7) Grind
8) Vapor Degrease
9) Glass Bead Blast
10) Electro-deposited Chromium Plating per ASTM B650 (2002)
11) Laser Mark
12) Passivation, Citric, per ASTM A967
The part looked silver and un-blemished prior to step#12 above (citric passivation). However, after the passivation process and prior to the water rinse, there were blackish areas which had appeared on the parts. After the rinsing with water after the citric tank, tan/light brown areas also appeared (maybe rust?). We ran some of these same parts again through citric passivation again and the same thing occurred. The rust-like coloration did disappear after coming out of the citric tank (still and the blackish discoloration) and then, once again, had tan/browning areas re-appear after the water rinse.
Of note, we had an order processed the same day of a similar but different part number. The operations were identical to the problematic parts but they appeared to be fine after completing the passivation. The only differences I could see was that the material lots were not the same (different material ID, heat-treat number, etc) and that the outside-service chromium plating was performed on different days.
Can anybody try to shed some light on why the one lot of bits discolored and the other turned out fine? Could it be either the difference in the raw material lots or maybe the an issue with the chromium plating?
Any ideas would be greatly appreciated. Thanks.
- Naples, Florida, USA
A. Hi Mark.
I don't claim to have heard of everything that exists, but I don't recall ever having heard of ASTM A967 passivation of hard chrome plated steel. Hopefully we'll hear from other readers one of the following:
- that it's a commonplace and Ted is showing his ignorance, or
- that you are processing to a very strange spec, the origin of which should be investigated or
- the spec is fine but something is supposed to be done to prevent the citric acid from penetrating the cracks in the chrome and attacking the D2 base steel :-)
Regards,
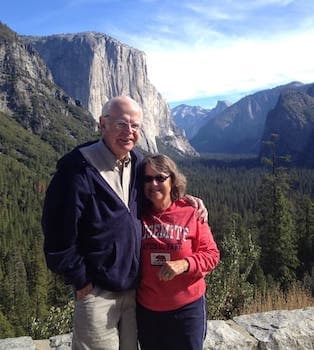
Ted Mooney, P.E. RET
Striving to live Aloha
(Ted can offer longterm or instant help)
finishing.com - Pine Beach, New Jersey
March 2020
A. Ted covered the problem: citric acid in the cracks and GALVANIC CORROSION in the cracks. citric acid does not "passivate", it is A "REDUCING AGENT". It "ACTIVATES" and depends on the air to passivate (oxidize), but before it can oxidize down in the bottom of the cracks it promotes galvanic corrosion which is as you say, brown iron rust.
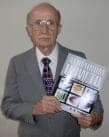
Robert H Probert
Robert H Probert Technical Services

Garner, North Carolina
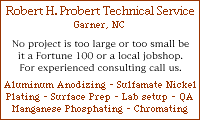
March 13, 2020

this text gets replaced with bannerText
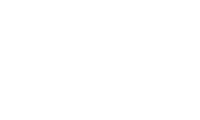
Q, A, or Comment on THIS thread -or- Start a NEW Thread