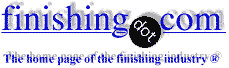
-----
Nickel Vs Copper as an Undercoat
Could somebody be kind enough to supply or point me in the direction of information regarding undercoats. I am looking for spec sheets and answers as to the better undercoat, Nickel or copper to be used on Brass terminals for Tin/Lead plating. Many Thanks.
Colin Greig- UK
2002
You do not say what you want the tin-lead for; is it soldering or bearings? The choice of interlayer depends on the properties you want. Nickel is a better barrier layer and will reduce the formation of intermetallics if the article is to be heated, although it can still form them. These in themselves are quite brittle. Copper is superior if you are plating thin parts that will be flexed, as the copper will help reduce the chance of crack propagation by dissipating the stresses induced during flexing. Nickel is harder, so if you want rigidity, it is the better option. Copper is cheaper and easier to deposit; it is also environmentally and health-wise a better option. If cost is no problem, why not use both, then you have some of all the properties
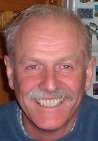
Trevor Crichton
R&D practical scientist
Chesham, Bucks, UK
2002
Q, A, or Comment on THIS thread -or- Start a NEW Thread