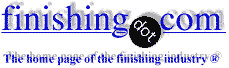
-----
316L Rusting
2002
I work for a Pharmaceutical company that will decontaminate its biofermentors with 0.78 Advance cleaning solution at 137 °C. The Advance cleaning solution is about 39 % NaOH and there is a chelating agent present. After cleaning the top inside lid of the biofermentor is covered in a reddish rust or rust colored material.
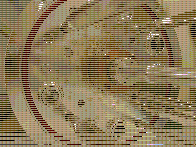
The biofermentor tank is 316L stainless steel and only the inside top lid is affected by this cleaning and is not in direct contact on a continues basis as is the rest of the tank which is submerged in the cleaning solution and experiences no rusting. Each time the rusting appears we send the fermentor lid out (the inside only) to be electro-polished. This has happened each time we clean the fermentor. Connected to the inside of the lid is a shaft that is about 3 feet long through which plant steam is used to heat the system (cleaning solution). The first 3/4' head of the shaft is a wider in diameter then the rest of the shaft. The head of the shaft is really two pieces held together with 316L bolts but the joint is a Tungsten and Graphite interface and it is at the interface that there seems to be depositing of rust on the rest of the inside lid. We seem to be losing passivation of the 316L Can you please help us determine what might be causing the rusting? Is there some kind of Galvanic corrosion happening between the 316L and Tungsten?
Robert Hart- Lake County, Illinois, USA
It certainly appears that you have set up some galvanic corrosion between the two, UNLESS there is something in your cleaning solution that causes a vaporous corrosive agent at that temperature.
You can easily get rid of the rust and repassivate the lid with commercial citric acid formulations. If you want to electropolish, you can try passivation after electropolishing to get a higher chrome/nickel surface. The highest chrome oxide ratios can be attained with the citric system.
Let us know if we can help.
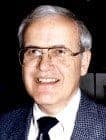

Lee Kremer
Stellar Solutions, Inc.

McHenry, Illinois
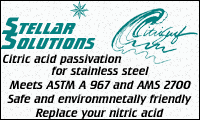
2002
Have your boiler water tested. Looks like your are leaking steam at the joint where the pipe goes through the lid. If the rust is only on the surface and not eating into the lid, this is definitely the source of your problem. Dan Weaver
Dan Weaver- Toccoa, Georgia
2002
Mr. Kremer, are you saying there is a difference between electropolishing and passivation? I thought electropolishing gave you a high degree of passivation? Can you please explain the difference?
Thanks,
Robert Hart- Lake County, Illinois, USA
2002
2002
Robert, we answered your questions on this in 18620. There are lots of differences between electropolishing and passivation. Both improve corrosion resistance substantially and additively (electrop. followed by passivation). The determining factor on what you use is your desired end results aesthetically and your cost parameters.
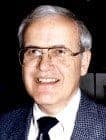

Lee Kremer
Stellar Solutions, Inc.

McHenry, Illinois
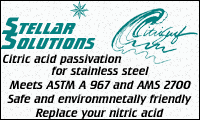
2003
Many of these bio-fermentation vessels contain nitrogenous bases as part of the nutrient medium. These are typically present as hydrochloride salts (e.g. guanine hydrochloride). At moderately elevated temperatures, hydrochloric acid evaporates from the solution and frequently condenses on the metal in the vapor space, producing corrosive attack. Because the buffering action of the less volatile organic base is absent in the condensate, vapor space corrosion is frequently far more severe than liquid phase corrosion. Unless hydrochloric acid condensation can be prevented, use of a more resistant alloy is the only solution. Super stainless steels like 904L and AL-6XN (N08904, N08367) are more resistant but have sometimes still been attacked. Nickel alloys like C276, etc. (UNS N10276, N06022, N06625, etc.) are better.
If the problem is just surface staining rather than corrosion attack of the metal, I'd look at the tungsten (presumably hard facing). While the tungsten carbides are generally corrosion resistant, the typical binders (Co, Ni and Fe) are not very corrosion resistant. Corrosion products from these could be staining the 316L lid. If so, a chelating agent like oxalic or citric acid should remove the stain.
Graphite is very inert (noble), and has been shown to cause galvanic corrosion of stainless steels. This is especially true in seawater systems where graphite gaskets have been implicated in numerous crevice corrosion failures.
John F. Grubb- Brackenridge, Pennsylvania, USA
Q, A, or Comment on THIS thread -or- Start a NEW Thread