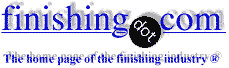
-----
Plating on Plastics: ABS vs PC, Nylon, & other plastics -- What substrate to use?
Q. Hello,
I just began to study some of the issues of plating plastics because next year I will do graduate studies (diploma) in Plastics Plating. I have found many papers of plating ABS but a few plating other plastics (PP, PC, PA66). Does ABS have advantages to be plated over other plastics?
- Monterrey, N.L. Mexico
2002
(2002)
A. Hi Gustavo,
Whereas I know zilch about plating plastics, I know a little bit about ABS.
ABS should have better impact properties than most other plastics (except Pe) and is eminently cementable.
Unlike PVC, for instance, you can, if you know how, edge join ABS using cement to achieve high strengths.
I'd imagine, too, that its coeff. of thermal expansion is far less than PP or Pe. In other words the chances of a plated section 'delaminating' should be less. Go check your books.
It is OK for aliphatic solvents but not, like PP, the polar solvents. It's house usage as drain pipe is excellent..
In mining applications they used a MINELINE pipe which is made of ABS ... and the fittings are CEMENTED together. Why ABS? Because of its impact strength and good abrasion resistance.
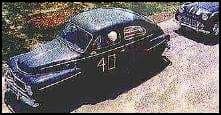
Freeman Newton [deceased]
(It is our sad duty to advise that Freeman passed away
April 21, 2012. R.I.P. old friend).
![]() |
A. The reason that most of the processes relate to ABS is because ABS can be etched chemically giving good keying and therefore adhesion. The "B" butadiene component of the ABS is microetched out with chromic/sulfuric and when the plating is pulled off in adhesion testing plastic comes away with the electroplate. ![]() Geoffrey Whitelaw - Port Melbourne, Australia 2002 A. ABS is acrylonitrile-butadiene-styrene. It is the workhorse of the plastics industry and is used in a myriad of parts. The beauty about it is that it is cheap and easy to metallise. Metallisation is achieved by etching it in chromic acid; this dissolves out the butadiene particles to leave a micropitted surface. The etchant also chemically reacts with the surface of the polymer to give chemically reactive sites. Other chemical etchants, such as permanganate are also known and can be as effective as chromic acid, but they are not as universal. The surface can then be easily metallised by conventional plating on plastics processes. Other plastics can also be treated in this manner and it is possible to get good metal adhesion. The polymers you mention (PP, PC and PA66) are a mixed bag. PP is very difficult to metallise, although it can be done; however, adhesion is not brilliant and it has a large coefficient of expansion,so delamination can be a problem, especially with high thermal cycling. PA66 is a nylon and readily adsorbs water; this makes it dimensionally unstable and not very suitable for wet processing; it also runs the risk of adsorbing chromic acid and this will not do any good to the products long term integrity. PC can be metallised by the above method with a great deal of success, but it is expensive (relatively). Other good plastics are MIPS and HIPS, acetal, etc. However, it is essential that before metallising plastics you are sure the plastic is fit for purpose in the final product. It is also possible to activate plastics by more sophisticated methods such as plasma etching. ![]() Trevor Crichton R&D practical scientist Chesham, Bucks, UK 2002 A. Dear Sir, - CAIRO, EGYPT 2002 |
A. Hi, Gustavo,
If you are to graduate on Plating On Plastics(POP) then you should already be aware that ABS is perhaps the only plastic readily available that has three components, one of them (butadiene) is a sort of rubber, the other two are plastic. This rubber is discretely and randomly dispersed in the form of round particles in a matrix formed by the other two components. When you immerse it in the proper chemical only those rubber balls are dissolved leaving tiny rounded pits over the plastic part. Maximum adherence is obtained at those pits where the orifice is smaller that the inside. This creates a mechanical counterlock when metal builds .inside them. No other roughening or etching can produce this geometry.
Monterrey, NL, Mexico
2002
Multiple threads merged: please forgive chronology errors and repetition 🙂
Chrome-plateable plastic alternatives to ABS and PC/ABS
Q. Hello,
I work for a manufacturer of injection-moulded plastic fasteners for the automotive industry. We have a customer that we currently make a plating-grade ABS component for. This part is chrome-plated by an outside plater. Our customer would now like to over-mould the chromed part with EPDM but the ABS cannot take the surface temperature of the second mould and melts. Has anyone had any successful experience chrome-plating other thermoplastics than ABS or PC/ABS? The plastic would need to be able to handle 200 °C (390 °F) and be able to pass an exterior automotive chrome plating spec. Any info on chrome-plating other plastics seems limited. I gather so are the platers willing to handle alternate materials. Any help would be greatly appreciated.
Thanks,
- Concord, Ontario, Canada
2003
A. Some grades of Allied Chemical's (Honeywell Plastics) "Capron" Nylon-6 are plateable, and as I read it are apparently good for 390-410 °F. Some chrome plated parts of this material are already used in the auto industry.
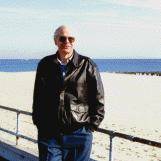
Ted Mooney, P.E.
Striving to live Aloha
(Ted can offer longterm or instant help)
finishing.com - Pine Beach, New Jersey
2003
A. I work in the automotive industry and PA (Polyamide) is plated for the automotive Industry. In France there is a company called "Sarrel" that plates it.
Best regards,
- Portugal
2003
Multiple threads merged: please forgive chronology errors and repetition 🙂
Plastic compounder finds that Platable Nylon isn't platable
Q. I am searching to find information pertaining to Platable Nylon plastic materials. DuPont states their Minlon grade (mineral filled Nylon 6\6) is suitable for plating. We have a highly filled (metal very dense) Nylon that our customer would like plated, but is running into difficulty. Any suggestions would be helpful.
Thanks,
Plastic Compounder - Worcester, Massachusetts, US
2003
A. It would help if we knew what you were doing so we can perhaps identify why it isn't working.
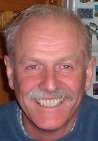
Trevor Crichton
R&D practical scientist
Chesham, Bucks, UK
2003
A. Plating on plastics is extremely difficult, and many of the process chemistry, such as hydrofluoric or peroxide will have detrimental effects on the metal fillers (which may be why it is not working). Usually only ABS and Polycarbonate blends are plated. I have not heard of anyone plating on Nylon 66.
Michael Zuraw- Georgetown, Ontario
2003
A. Nylon is soluble (hence degradable) in Sulfuric Acid and Fluoboric Acid so stay out of those two.
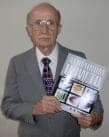
Robert H Probert
Robert H Probert Technical Services

Garner, North Carolina
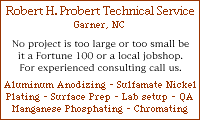
2003
A. I believe Michael Zulaw's reply saying that "I have not heard of anyone plating Nylon 66" was somewhat misleading. There are quite a few applicators doing plating on Nylon 66, Nylon 6 + others. Moreover you can also do plating on Nylon/ABS blend. Check out with the major POP process suppliers and you will get a better picture.
Also make sure the Nylon 66 resin is plateable in order to give a better etching and adhesion performance (i.e. to provide mechanical "interlocking" properties for subsequent catalyzed reaction for "seeding" process. The etching process is essentially not of a conventional chromic/sulfuric type. Proper pre-plate process for Nylon substrate will lead to fine metallizing performance as other resins like ABS, ABS/PC blend which primarily is a conditional metal layer for onward electrolytic copper or nickel plating.
Plating process supplier - Hong Kong SAR, PR China
2003
A. Nylon 66 is not usually metallised because it (like most other nylons) has a high propensity towards swelling in water and therefore losing dimensional stability. That is not to say it cannot be metallised, only that its tolerances and properties will be difficult to maintain.
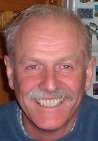
Trevor Crichton
R&D practical scientist
Chesham, Bucks, UK
2003
What determines if PC/ABS plastic is plateable?
Q. I am a materials engineer for a plastics company. My company makes a PC/ABS (similar to GE's MC8002 product). A customer has asked me if this product would be "chrome plateable" and I don't see any reason why this product would not.
Do you have any reasons why a particular plastic wouldn't be plateable -- and PC/ABS in particular? (As in there are "platable ABS's and non-Platable PC/ABS" -- what makes them more readily platable)?
Kind Regards
- Grand Rapids, Michigan
2004
A. I thought someone like you, working for a plastic manufacturer should know better. Most of the people participating in this forum deal more with plating processes. Plastic manufacturing trade secrets or tricks are not our specialty. Ask your peers or competitors what they put in it to make it platable (and then tell us to increase our knowledge).
Guillermo MarrufoMonterrey, NL, Mexico
2004
A. Hello Mr. William Atwood,
We electroplate on (PC/ABS). Actually it all depends on the mixing of the PC in the ABS, the percentage of mixing. The higher the PC percent (%) in ABS, the more difficult the process will be.
Regards
- Karachi, Pakistan
2004
2004
A. Dear sir
PLATABLE OR NOT? That depends (in my opinion) on two things:
1- Etching: If you can make suitable holes then you have a good key to plating this polymer; but these holes (in most cases) depend on something dissolving out and leaving in its place a hole. In case of ABS, butadiene plays this role (actually it is Ideal for this role because its particles are spherical; when dissolved in acids it leaves wonderful spherical holes.
Polystyrene is not platable with the usual procedure, but when butadiene is added it is converted to polystyrene high impact and plated with the same method as ABS.
Polyester is too difficult for plating but when when some carbonate is added as a filler it will be easy to make a hole on its surface.
It was found that if etching will be two stages.
Pre-etching [SWILLING] & etching most polymers give a Good results for pre etching solution it always contains amines, strong alkali,and Glycols this solution is very active against poly carbonate as a pre etchant.
2- Activation: We have to chose the suitable manner of activation.
Some materials are weak against acids so alkaline activation is preferred. Some materials the acidic activation is very successful like the ABS/PC you mentioned.
GOOD LUCK
plating of plastics - Cairo, Egypt
Q. How can I test to see if the material is ABS or HIPS plastic?
Thank you,
working in shop selling finishing touch - Morristown, New Jersey
2007
Grain depth in ABS parts
Q. We are plating on decorative plastic engineering parts. We are plating on ABS and PC+ABS and Hex/Tri and Satin finish on emblems, logos, grills, garnishes, fog lamps, hood strips and door handles.
I want to know what are the grain size allowed in any Grill or Garnish which will easily pass all plating tests as applicable in plain surface. Actually Grills have both shiny and matte surfaces. After plating we are facing an issue in matte surface areas where grain structure for matte finish. That area fails in thermal cycle test. Etching parameters Cr2O3 = 410 gm/lit , H2SO4 = 410 gm/lit , Cr+3 = 8 gm/lit , Temp 67 °C.
Electroplating plant - Pune , Maharashtra , India
September 21, 2014
Alternative to chromic acid etch for plastics?
April 27, 2019Q. Hello, I've been reading this forum for quite a while now and usually find an answer to my question, but this on does not look like it has been asked. This is for a sponsored research project in my research group.
We are trying to perform electroless plating on plastic of a mix of iron and cobalt using palladium catalyst and a boron reducing compound. The specific plastics we are working with are polystyrene and Kraton G (styrene-ethylene/butylene-styrene). We know the plating solution works since we are able to get the metal to deposit on copper after activation by dipping it into a PdCl2 solution. For the plastics we are using a tin chloride sensitizer step before the palladium step however it appears that the tin is not depositing or the palladium is not reacting with the tin because we can only ever get barely visible indications of metal deposition in the end.
We are aware that an etching step is required but our health and safety folk would sleep much better if we did not have to use the chromic acid etch that sounds like the favored option. I've tried corona treating, immersing in 30% H2O2 and undiluted sulfuric acid (doubtful the latter would actually help, tbh). None of these work, so I am reaching the point where it's either the chromic acid or piranha solution... it can't be good when you are forced to choose between those two options! (PSA, for anyone who does not know piranha solution earned that name for a reason; explosive reactions with organic solvents spraying sulfuric acid and shards of whatever container formerly held the mixture). Can anyone suggest something that works and doesn't have as bad of a rep as the above two?
A few notes:
- Yes, we know iron plating is not easy but it's what we have to do for the project.
- Specific aspects of the project make electroplating a non-starter
- We are not really concerned with the quality of the adhesion to the polymer as it will be encapsulated by another layer of plastic
- Kraton is a thermoplastic elastomer; plating onto it is going to break up the metal film upon flexing and is in fact a desired outcome in this project.
Hope this gives a clear enough sense of the situation but I am happy to provide other info as needed.
Professor, U. Mass-Lowell - Lowell, Massachusetts, USA
A. It's quite difficult to deposit metal directly into plastic without any kind of treatment. I've been there many many times, my experience with this is the same as yours, pre-treating the surface with tin chloride sensitizer and palladium activator, that is because of the surface tension of the plastic, but I have had very good success with a wetting agent treatment right before the Tin Chloride sensitizer, it's an organic wetting agent.
Here is the formula; you may want to try it.
For 500 ml of ready to use solution.
100 ml of isopropyl alcohol (High %)
50 grams of Instant coffee, (also called soluble coffee, coffee crystals, and coffee powder, not to be confused with the pure grains)
400 ml of cider vinegar
⇦in bulk on
eBay
or
Amazon [affil link] will work too)
Follow the normal procedures you use to coat the plastic article with Iron/Cobalt but this time treat the piece with the wetting agent instead of the etching and before the tin chloride treatment (don't rinse off the wetting agent, just dip it in the tin chloride sensitizer).
The reason I don't plate directly to plastic is its poor adhesion, but you are okay with that.
- Managua, Nicaragua
Q. Hello, I am a QM in the auto industry. I have a new supplier molding and chroming a part for us (2 shot). The second shot was being manufactured with a PC / ABS material. My new supplier wants to switch to just an ABS only. They are telling me that there is too much stress in PC / ABS and it will cause chroming issues. I did a little research and I find that because my current PC / ABS has a higher melt flow and Vicat softening point than the ABS (again, according to some articles), it should have less stress or recoil. I have also found that PC / ABS is more expensive. Not that I am not a trusting individual, but everything I have read about PC / ABS versus ABS negates what my new supplier is telling me. I am smelling something not right here. Please assist with your take on this situation. Thank you
William GipsonAutomotive - SPRING LAKE, Michigan, USA
March 31, 2020
Q, A, or Comment on THIS thread -or- Start a NEW Thread