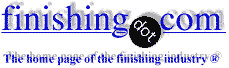
-----
How to make bronze / History of bronze
Current discussion:
Q. Re. Harry C's suggestion: I was thinking of melting copper scraps first, then adding the calculated amount of 260 brass scrap to obtain proper zinc proportions, then add some tin solder and mix all before pouring. Comments?
Jason BoshHobbyist - Indianapolis Indiana USA
April 16, 2022
@Matthew D: First copper smelting was discovered long before sumerians knew they would become sumerians in modern day Serbia by Vinchan culture -- not only copper but other stuff which are believed to be done by sumerians first were done by people of Vincha/Danube river valley civilization etc.
Like the wheel with axle, bread, domestication of wild animals. I believe even fertilizers were discovered there, too, as there is evidence they used the same plot of land for a long period of time to plant things such as wheat.
- Serbia
June 30, 2022
⇩ Related postings, oldest first ⇩
Q. I'm 15 years old, and I'm wondering how do you make bronze. I know it consists of copper (90%) and tin (10%) which should be 9 parts in 10 copper. Is there any way I could use aluminum like soda cans? Please give me tips and techniques about bronze making.
Thank you,
Matt [last name deleted for privacy by Editor]- Henderson, Nevada
2002
A. You need to melt the copper and add the tin to it. Aluminium cans will not withstand the temperatures and will melt before you melt the copper.
By the way, there is a wide range of bronze compositions, all with different colours. Low copper bronzes can be silver in colour, whilst high copper ones are a golden brown or even with hints of green.
You won't do it unless you have access to a furnace that can reach well over 1000 °C. Not only is this dangerous, but such furnaces are expensive to buy and run.
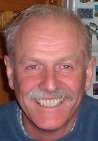
Trevor Crichton
R&D practical scientist
Chesham, Bucks, UK
How to make bronze, etc.
Mr. Crichton: Your response was very interesting, brief and to the point. I had often wondered how to make bronze and copper etc and it was by accident that I came upon this site. I decided - in my own small mind - that you must be a man of distinction!~
Thanx very much.
Ruth C [last name deleted for privacy by Editor]- Santa Monica, California
A. Hello, post number 2 is incorrect with the temperatures, please DO NOT post if you do not know what you're talking about, it's very annoying. Anyway I just thought I would post pretty much everything you would ever want to know about bronze:
Bronze was developed about 3500 BC by the ancient Sumerians in the Tigris-Euphrates Valley. Historians are unsure how this alloy was discovered, but believe that . . .
Matthew D [last name deleted for privacy by Editor]New York, New York
2004
----
Ed. note: the balance of this posting was deleted because it is accurately reported below that it was simply copied and pasted from another site without attribution. The actual author of the article, John Paul, was kind enough to log on and comment further on down the thread.
Matthew D.,
I do not appreciate your answer, as I understand you simply copied that text from another web page (www.americanbronze.com/WhatsBronze.htm).
What you seem not to understand is that brazing (what requires the metal to be heated below melting point, or 430 °C (800 °F)) is simply how to join to other metals with bronze. This has nothing to do with making bronze, and I suppose if you had actually read through and understood what you were plagiarizing, you would already know that.
Robert Z [last name deleted for privacy by Editor]- Provo, Utah
2004
----
Ed. note July 2022: Sorry, americanbronze.com has dropped that article :-(
2005
Whilst the second post in this thread may have been accurate and to the point I feel it was rather discouraging in its intent. A fifteen year old inquiring mind asks a question of people who have experience to offer and is told flat out not to bother trying anything as it can't be done. My personal experience is that most non-ferrous metals can be cast quite safely at home if a little research and a lot of care is taken.
If the first poster is still looking, I would start at www.theworkshop.ca. The owner of that site is helpful, insightful and above all else nobody tells him what he can and can't do.
regards,
- Auckland, New Zealand
----
Ed. note July 2022: Unfortunately, that website is gone.
Thanks for the link, Gregg! ... but I didn't read Mr. Crichton's posting your way whatsoever …
Trevor Crichton has extremely patiently and for no personal benefit whatsoever answered more than a thousand student questions on this site, often in exhaustive detail. Just use the search engine with his name as the search term to see his yeoman efforts towards helping students. I am amazed at his generosity when students nearly never thank him ... but adults drop in to criticize.
We have more 10,000 student questions on line here ... half a dozen new ones every single day. If either you and/or the owner of www.theworkshop.ca could please volunteer to handle even a couple of those student questions a month it would take a load off of Mr. Crichton, and perhaps allow him to be less constrained by time. Thanks again for the link!
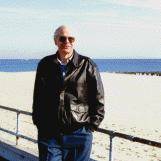
Ted Mooney, P.E.
Striving to live Aloha
finishing.com - Pine Beach, New Jersey
2005
Q. Okay guys, so here I am trying to recall the two main ingredients of bronze with the help of the internet. Got some more questions for any of you out there that may have an idea as to the answer. How do we know where bronze originated from, how did they figure that they could get it from ore, how did they build these furnaces and generate those kind of heats, was there residual materials that needed to be moved? A web link will suffice if I'm asking too many questions thanks.
Glen [last name deleted for privacy by Editor]- Manchester, UK
2004
A. Dear Matt,
You've got the right idea, bronze should include anywhere from 10-20% Tin and the rest should be copper. What the rest of these guys say is right on as well. You will need to find a way to heat the copper up to 1,000 degrees or more. Tin's melting point is less than half of what copper's is (around 480 degrees), but even a stove top can melt it... but don't try that. I'm not going to pitch you a whole bunch of crap about how you should never do anything dangerous or work with hot fires, I did it in my youth and never got harmed, but that's only because I was EXTREMELY careful and was always in a situation where I could get help if I needed it. I don't care what you're doing with the bronze either, as long as you're being creative and not hurting others then who cares?
Good Luck with your smithing,
Erick M [last name deleted for privacy by Editor]- NYC, New York
2005
A. I would recommend not using just copper and tin by themselves, but also adding a small amount of lead or zinc, or both. This will strengthen the bronze and give it a nicer finish.
Harry C [last name deleted for privacy by Editor]- Wellington, New Zealand
2005
Q. I would like to know how much lead or zinc should be added to a mixture to make the Bronze?
Cyrus C [last name deleted for privacy by Editor]- Akron, Ohio
2005
Q. I'm 13 and my dad & I are going to make bronze and I don't know what is right 1000° F or 800° F? Please reply soon.=)
Danny L [last name deleted for privacy by Editor]- Grand Marais, Minnesota
2005
A. Hello, Danny! I don't think it's 800 °F; I think it's over 1000 °F per Mr. Crichton. But you've already learned that the internet really isn't an authoritative reference. Please try to visit a library and get help from the librarian if necessary to find the melting points in a metals book. You might find the cool charts of eutectic points and such interesting :-)
The American Society for Metals has a series of two dozen oversize volumes which comprise "The Metals Handbook". If you can find a library that has it, you'll be amazed at the exhaustive detail available. Good luck!
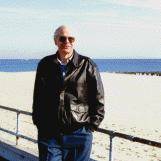
Ted Mooney, P.E.
Striving to live Aloha
finishing.com - Pine Beach, New Jersey
2005
A. The melting point for tin is 449 °F. The melting point for copper is 1984 °F. Therefore, the melting point of bronze depends on what percentages of metal you're using; a high tin bronze will have a lower melting point than a low tin bronze. Hope that clears up any confusion; no one can tell you the melting point of bronze without first knowing the composition.
Ben Friesen- Duluth, Minnesota
2007
Q. I would like to use bronze sheet to make a pair of chassis for valve (tube) amplifiers. If using steel I would use 16 gauge. I have two questions for you experts;
a) Which bronze would give me more of a rose colour, (as opposed to the bright gold of brass), and;
b) Would 16 gauge bronze sheet provide the same rigidity of 16 gauge steel, or should I go to a thicker sheet?
Many thanks in anticipation of your kind replies,
- Burbage, Leicestershire, England.
2006
Q. I was wondering how to make bronze and happened upon this website. I'm 16 years old and my uncle (who's house I visit often) has a building full of tools, so I have a good bit of resources. I have plenty of tin and copper. I wanted to ask
3 questions:
1) How would I go about shaping the mixture?
2) How much of each material should I add to make a strong, durable bronze?
3) Would a blowtorch that reaches 1000-1500 °F work to melt these materials?
- Lanett, Alabama
2006
Q. Hi I'm, well um, I'm nearly 13 and I want to make bronze. Could I make a fire in the ground and using a pump to blow air into the fire whilst adding coal could I reach about 1000 degrees °C? I would be using a crucible please help!
thanks :-)
home - hereford, herefordshire, England
2007
A. Hey, Will, just like yourself I'm 13 -- and to answer your question I don't think that well work. You might need a smithing kiln or an oven but I could be wrong. If so, someone please correct me.
Zack H [last name deleted for privacy by Editor]- Willmar, Minnesota
2007
A. Anyone interested in metal casting and making home made alloys and tools should check out backyardmetalcasting.com. The man that runs the webpage is a hobbyist and provides plenty of useful info on the topic including how to make you own furnaces, crucibles, and casting sands. Perfect for the curious metal working mind in my book. Be advised working with molten metal is pretty dangerous though. I have had molten aluminum (melting point 1440 °F, easily attainable with charcoal and a hairdryer or a propane torch) explode from the ingot casting tray I was using (I guess dirt or some form of moisture bellow the metal) onto my face. Only burnt off a little of an eyebrow thankfully, but I quit casting until I purchased a metal hard hat to protect my scalp and a full face shield you can get from welding supply stores. You also want to make sure not to do this over concrete as even the driest looking driveway will have enough moisture to cause small explosions (personal experience) so a nice sandy spot in the yard would be the best place. With good safety gear this is a very fun and rewarding hobby. Go out there and have fun with it kids.
David kirk- Charleston West Virginia
May 13, 2012
A. I am 15 and for the last several years have worked in metallurgy with only a pit in the ground and have reached temperatures of up to and above 1500 °F using hard wood and some sort or blower weather a hair dryer ⇦ on eBay or Amazon [affil links] or a small fan, the blower I use has varied depending on desired temperature and what I have on hand my fire pit is just a 5 inch deep by about 3 feet in diameter hole in the ground with a wall of bricks about 2 and a half feet tall around it and with that simple set up I have melted copper and gotten hot enough temperatures to make Damascus steel and as warned you should be safe because I have been burned and help from an adult is best to have.
John W [last name deleted for privacy by Editor]- Montesano,Washington
2007
----
Ed. note: Thanks, John. That was terrific!
A. Wow. Lots of comments and recommendations. I created the article for American Bronze as a reference for customers seeking general information about bronze. As far as working with metals at home, no problem. Many people do that.
As far as making metals at home, I would think that would require a lot of research and effort to get the correct mixtures. Also using scrap would require getting impurities out of each before using them. Very time consuming.
I would recommend contacting a foundry that produces metals for the industry. We used Everdure Bronze for statues that has a specific copper, zinc, and some other contents. Other uses requires different percentages of ingredients.
You can purchase small casting tools and equipment online. The number one thing to remember is be very safe. Bronze melts at 1750 °F and we would pour our products at 2250 °F. At these temperatures contact with water would create an explosive action. Contact with your skin would be very very serious. Please DO NOT ATTEMPT WORKING AT THESE TEMPERATURES WITHOUT PROPER SUPERVISION, SETUP AND PROTECTION!
Otherwise, be creative, have fun, and learn.
- Deltona, Florida
2007
2007
A. Hi Guys,
If you want to smelt your own bronze, and just want to have a go, then this the following should be a good introduction.
This will lead to many questions.
In history bronze can be as simple as 90 percent copper 10 percent tin, or it can have precious metal in it such as silver and gold, with no tin to be seen at all (the Colossus of Rhodes was reputed to be made from this alloy called black bronze).
Adding more tin will lighten the bronze 80/20 (bell metal) is almost white (almost), but is brittle, and will shatter with thin castings.
So for your purpose stick with the 90/10, this will make a very durable bronze that has a goldy-brown colour, good for jewelry, and other items.
This is something I created to test refractory materials :-
members.optushome.com.au/charlesanderson/img/MicroFurnace.jpg
And this is probably as cheap and uncomplicated as bronze smelting can get.
The furnace body shouldn't cost you more than $20, the crucible $13 (and is the smallest one I could get... just a materials test remember), the tongs $13, and the expensive component is the JTH-7 Bernzomatic hose torch, and adapters to fit it to a standard BBQ cylinder. You can borrow the BBQ cylinder from your Dad ;-)
The furnace body is made from a milk powder can (about the size of a coffee can), a K26 fire brick, padded with some hi-duty kaowool, and sealed with some zirconium paint (you could use kaowool hardener here instead of the paint).
If you decide that you don't like melting metal and casting metal, then you can give the heating components to your Dad next Father's day, and give the furnace to a friend.
** Caution: This little furnace gets very hot very quickly, the melt point of bronze is 800 °C, but the flow point is 100 - 200 degrees hotter.
** Note: Please season your crucible first, or it will shatter (see a question about seasoning crucibles).
The procedure for this furnace for bronze is as follows :-
1) Fill your crucible to the brim with
bonami, and then tip it out. This lines the crucible with "flux" and makes the metal flow nicely.
2) Put your tin into the crucible (I like to do this first, as the tin effectively lowers the coppers melt point).
3) Your copper goes into the crucible next. The best type of copper for this operation is granulated, but small pieces will do as long as the tin is covered. Put some more borax
⇦ on
eBay
or
Amazon [affil links]
on top.
5) Light your furnace, and lower in your crucible (with tongs), put the lid on the furnace. Check in about three minutes time.
** The following is an old trick that works, but if you don't feel comfortable with it buy a graphite stirring rod.
6) Your bronze should be molten or very close. Get a green stick (not a wet or turgid stick), and use this to stir your alloy. The impurities will stick to the green stick. As an added bonus the stick will turn to charcoal, and can be used as a stirring stick until it disintegrates.
7) Your bronze is ready to pour into your mold (and that is a big topic too).
That's it.
Oh and I can't state this enough, although the furnace is small, it can still burn you very badly. If you don't feel confident don't attempt this.
There are many casting groups on the net that will gladly assist you in this hobby.
Regards Charles
- Mortdale, NSW, Australia
I was looking on how to make bronze for a school project and this was a site I found and it helped (some)
- Hilliard, Ohio
2007
Q. Hi I'm 15 years old.
I would like to make bronze making a hobby but I don't know much about it yet. That's where I need your help.
I would like to know hot to make a furnace capable of melting copper and tin as I don't know what materials to use. It would be helpful if it was household items as I don't have a lot of cash.
Please make a list so I can use it and say where it all needs to go.
Thank you.
hobby - united kingdom
2007
A. I know that the BBC show, "What the Ancients did for Us" had an Egyptian episode in which they made bronze by making their own furnace, with foot bellows, and I was actually looking for more information on that, when I came across this site. Although they had a full safety team, they proved that it is possible to do in a backyard
Matthew Rusworth- Bury St. Edmunds, Suffolk, UK
2007
Q. I am in Eighth grade, and we have been assigned projects that have to do with metals. I have chosen bronze. I wish to make my own, but am at a loss as to where to get the copper for the bronze. I have loads of tin in my home. I just need to know if anyone knows any websites or companies that will sell any copper.
Roberto [last name deleted for privacy by Editor]student - Louisville, Kentucky
2007
A. You can find copper on line, Roberto, but if you only need a reasonable amount you can buy copper wire from most large hardware stores, and strip the plastic insulation off. An interesting thing you will learn in science class is that very pure copper conducts electricity much better than even slightly contaminated copper, so copper wire is very, very pure copper -- well over 99 percent pure.
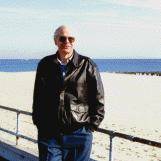
Ted Mooney, P.E.
Striving to live Aloha
finishing.com - Pine Beach, New Jersey
2007
Thanks Mr. Mooney. Do you know which websites might sell some copper? If not, I may try Hardware stores.
student - Louisville, Kentucky
2007
A. Onlinemetals.com is one.
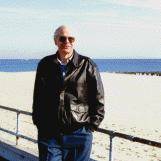
Ted Mooney, P.E.
Striving to live Aloha
finishing.com - Pine Beach, New Jersey
2007
Q. I have plenty of copper wire. Is there anywhere online I could buy some tin?.
If not what are some items I could find the are made of tin (not Aluminum).
- Port St. Lucie, Florida
January 5, 2008
I am 15 and this is my first making bronze and I got all my stuff at Manards for $20.
Aaron J [last name deleted for privacy by Editor]- Prior Lake, Minnesota
February 1, 2008
February 9, 2008
A. This should help people make lots of heat.
I'm not sure if this will work for melting bronze, but I'm a blacksmith and I heat my steel with this.
You need: about 50-ish bricks, not the cheapest, but you don't need refractory bricks either; a metal tube, about 7 cm (3 inches) wide and thickish walls; a cheap hair dryer; sand; and fuel, I use charcoal.
1. Break on of the bricks in half.
2. Put a layer of sand on the floor.
3. Make a box with the bricks on top of the sand 3x3, using the half brick in the bottom row in the middle of one of the sides.
4. Build up three or four levels and then make a dome over the top.
5. Insert the metal pipe in though the gap at the base.
6. Pile sand up to the height of the pipe without blocking the hole.
From there it's straightforward, put charcoal into forge, light, and use hair dryer as air source.If done properly, the fire itself will reach about 1100 °C (2000 °F), but your crucible will be a few hundred degrees lower.
But like I said, this is what I use for heating lumps of steal, not melting things (but I'm trying). Someone who knows about that will have to tell you lot about that.
Oh, and Bricks: Maybe 50p Each, maybe a bit more.
Sand: if near beach, free, if not, cheap.
Metal pipe: Sorry, don't know, I had an old handrail that I cut into pieces, but if you've got a good metal saw, go and nick a street sign pole (No, don't, that was a joke)
Hair dryer: 10-15 Pounds (20-30 Dollars)
Charcoal: 2-3 Pounds the bag, and I use 2-4 bags every time.
- Montevideo, Montevideo, Uruguay
Q. I've read on other Technical question posts that bronze can contain copper and tin basically, and that it would be a good idea to add lead or zinc to the mixture for a better finish and quality.This may be a stupid question but do you have to obtain copper and tin directly from a mine or can you use household items such as cans and pennies. I'm only 13 and I'm not very familiar with chemistry.
Brandon R [last name deleted for privacy by Editor]hobbyist - El Dorado, Arkansas
February 10, 2008
A. I get tin for about $18 AUD a kilo. I get granulated copper for about $4 AUD a kilo. Copper can be found easily, however tin is best bought from a metal merchant, as it is rarely used in its pure form.
Whilst at the metal merchant you can buy 90/10 bronze ingots for about $9 AUD a kilo. I prefer to alloy my own bronze as I can control the amount of tin therefore the colour, and properties.
I like to add the tin to the crucible first, and cover with granulated copper, this way I don't loose as much tin as vapour.
My friend adds the tin after the copper has melted, and comparing our bronzes, mine doesn't look as "pink".
Regards Charles
- Mortdale, NSW, Australia
February 14, 2008
Q. Hi:
I'm 9 years old and interested in making bronze this summer when I am up at my grandparents' farm. My parents said they would help me research and make bronze.
I read that adding water could cause an explosion. Are there any other big safety concerns other than heat and getting burned?
Also, I read that you shouldn't let oxygen into the mix. Why is that? Where can I go for a complete and trustworthy how-to?
Peter
- Brooklyn New York
April 6, 2008
A. Hi, Peter. As mentioned earlier in this thread, your librarian can help you find an age-appropriate appropriate book on the subject. You won't easily get complete and trustworthy info on the free internet. Good luck.
Regards,
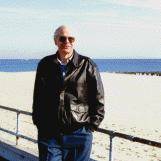
Ted Mooney, P.E.
Striving to live Aloha
finishing.com - Pine Beach, New Jersey
April 7, 2008
A. Another source of information might be to contact the art department of university. I am unsure of whether or not they cast metals on campus, but the sculpture department should be able to point you in a solid local direction of persons that use these materials. it is not 100% required but being able to observe a controlled pour is a great experience as well as a great reference point for when you strike out on your own. I used to assist in the sculpture labs at my former schools and some of the neighboring ones as well. one thing that all of the instructors I have had the pleasure of meeting shared was a great passion for sharing knowledge with young minds that were excited about the process. another portion of the equation is creating an investment (mold) that can withstand having a metal heated to this degree added without overdue stress.
christopher ryan- Las Vegas, Nevada
April 7, 2009
Q. I am doing a research project on metals, and I was wondering how you would cut it if you were going to make something out of it? Also, do you shape the bronze by melting it?
Tina BobzStudent - Oklahoma City, Oklahoma
December 30, 2009
A. Tina, in reference to your question about how to cut or mold bronze.This depends on what you would like to create.
I am here to help.
Master Jeweler and sculptor.
Pete
- Algonquin, Illinois
January 8, 2010
Q. I am understanding that it takes an exceptionally high temperature to melt copper. if you were to use a metal file to grind the copper to a rough powder, or a hacksaw to cut a copper pole into thin bands, then would that in any way make it easier to melt? Please post a response to let me know.
Brent Bandy- Wichita,Kansas
February 18, 2010
A. Hi, Brent. Chopping the copper into fine pieces might shorten the time required for it to melt, but it will not change the melting point temperature.
Regards,
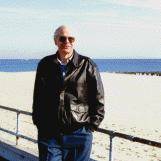
Ted Mooney, P.E.
Striving to live Aloha
finishing.com - Pine Beach, New Jersey
February 19, 2010
March 8, 2010
!! Having run across this page at random, and having never tried before to create an alloy, I performed a most interesting experiment today, and thought I'd share. I formed an almost-bronze alloy using a jeweler's furnace. I didn't have any tin, so I used pewter instead, which is generally over 90% tin; that and the copper were in the form of the small droplets one generally buys from jewelry supply stores for casting.
My alloy was made from 50% of each metal; from advice on this page, I positioned the pewter under the copper in the crucible. No detectable fumes emerged as the amalgam heated.
Monitoring the furnace as it heated, I found that the pewter melted at a regular 500 degrees or so, while the copper melted into the pewter at around 1500 degrees Fahrenheit, some 480 degrees lower than its usual melting point: I find this fascinating, by the way: how does the copper "know" that the pewter is there?
Using the Kerr Satincast product, I created a mold for a ring using two sprues: one for pouring and one for the air to escape. I burned it out in a burnout oven and allowed its temperature to reach 1200 degrees, which appeared to be appreciably below the alloy's melting point, but still hot enough to allow the metal to flow without hardening immediately.
I poured the metal into the mold and noticed that I was obliged to tap the mold several times to encourage the metal to flow around it properly and emerge from the ventilation pipe I had included; it appeared to have assumed an almost syrupy consistency. Having convinced myself that the metal had permeated the entire mold, I then allowed it to cool.
The result was a black, very smooth surface, which felt like anodized aluminium. To my surprise, I found that the alloy was so brittle that it had the strength of a ginger snap. Upon breaking sections of the metal, I saw that the cross section had a silvery color, very similar to the original pewter. All traces of the copper's coloring had disappeared. The metal appeared to have an unexpectedly crystalline consistency which I found impossible to file or shape in any way: it was completely inflexible and stiff, and would break before allowing itself to be manipulated in any way.
I shall repeat the experiment tomorrow, this time using only 10% pewter to 90% copper. Most interesting.
- Los Angeles, California
A. It's a matter of dissolving.
Salt (NaCl) melts at 1440 °F, but can dissolve readily in room temperature water.
The same is happening to your copper. The molten tin is dissolving the solid copper well before the copper melts. However unlike salt and water, the solubility of copper in tin really doesn't become significant until the 1500 °F you observed. At the melting point of the tin, only a minute fraction of your copper can dissolve - so little you probably won't notice it.
- Toledo, Ohio
March 10, 2010
A. I have been trying to cast bronze for a while now with my son. We built a small furnace from a design on the internet and put wheels on it for easy ., but we could not get it up to melting point trying different mods over about 4 months.
We where also doing a bit of forging and Ben suggested putting the crucible in the forge This we did and had our molten bronze in about 6 minutes I was amazed how quickly it melted and he cast a scarab in a mould he made using the lost wax process.
- Fermanagh, Northern Ireland
April 4, 2010
A. I have been a blacksmith for 3 years now at age 16 and only recently were we able to melt bronze. Our forge is just a cement lined pit in the ground, fired by coke (coal or charcoal works too) and an old hair dryer for the airflow. Though me living in Pennsylvania does help with the forge (I can just go pick up coal and coke off the ground) After reading the posts above I plan to try the method of dissolving the copper into the tin, sounds like a good idea. Anyway as for materials I use copper tubing and a 99% tin solder.
Pennies wont work for the copper because they are mostly zinc
as for the tin don't use stray cans, foil, or random solder because you could be contaminating the bronze with resin, lead, or silver.
If I missed any questions please post again :P
- Pittsburgh, Pennsylvania, USA
July 6, 2010
A. Actually you can melt the necessary constituents of most bronzes by making a temporary hearth from bricks, preferably "Firebricks" (used by builders for hearths in houses, so quite cheap - and if you want it more permanent you can use "Fire cement" in the construction). Your fuel should be barbecue charcoal. Make the central space about a 10 inch cube. Leave a small gap in the bottom tier to take the end of an old vacuum cleaner's exhaust air pipe. (Mind you get the "Blow", not the "Suck" end (Lay the initial fuel load on some newspaper and dry wood kindling and pack the charcoal around your crucible (a small length of steel pipe hammered closed at the bottom). Once it is glowing. start the blower (not too much air, mind). If you are lucky you could get hold of some coke - not so easy these days of natural gas, but this lasts much longer than charcoal. The early bronze-age smelters could only have used charcoal in a pit on a slope with a hole at the bottom facing the prevailing wind - they had no other fuel nor had they firebricks!
Good luck with your smelting!
Cheers, Pette Dewar
- Oxford, England
July 12, 2010
A. Making a small forge to melt and cast metals from is easy and cheap.
This past weekend I made some bronze in a forge made from a refractory cement lined large flowerpot. All up it cost around AUS$50.
My airflow comes from an old vacuum cleaner, though I think a cheap leaf blower will be a better source of air.
- Hobart, Tasmania, Australia
May 10, 2011
A. Hey guys I noticed you talking about a heater. Well, I'm 90% sure an open fire could melt them both; all you need is a pot, a fire, and a structure to suspend the molten metals in. Lol -- it's gonna seem weird of me but I've also had an interest in it because I've always wanted to make weapons and stuff out of it.
Scott Stevenson- Detroit, Michigan, USA
November 24, 2011
A. Smelting metals has been performed safely for years with nothing but a fire pit and a clay pot (I made mine out of Kitty Litter Clay). I have smelted many metals and even made carbon steel all in a fire pit. This is how smelting got started centuries ago. Care must be taken but the basics equipment is a heavy duty pair of fire resistant gloves and a really big pair of channel lock pliers.
I plead with all though never discourage learning just add the advice of using caution.
Peace
Paul
- Dallastown
December 19, 2011
Hi, Paul. I largely agree with you: Smelting is very low-tech and has been practiced for millennia.
But we have the practical problem that telling young people to "be careful", without being able to give any 'hands-on' instruction or even specify all the things that they should be careful about is of limited value. Some of the writers identify themselves as 9 years old, 15 years old, in 8th grade, etc.
The internet is a vast one-room schoolhouse, where kids invariably read snippets of discussion between experienced people who certainly can't precede every sentence with every possible appropriate warning for a nine-year old. If you were to read on a medical site "... then simply inject 10 ml of sodium thiosulphate ⇦ on eBay or Amazon [affil links] ", you know that this is not something for untrained people, but children reading about metal casting on the internet might not recognize the dangers in similar situations. Hands-on training wherever possible seems to me more fun, more practical, faster, and fwayar less dangerous than internet reading.
Regards,
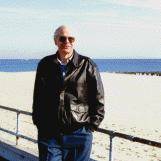
Ted Mooney, P.E.
Striving to live Aloha
finishing.com - Pine Beach, New Jersey
Q. I want to know which is the best copper alloys for the investment casting. And what is the proportion of copper and other metals. and I also want to know which bronze suitable for this castings.
Ankit Adeshara- Baroda, Gujarat, India
February 1, 2012
Q. Okay, bronze is 90% Cu and 10% Sn. Or perhaps it's 88% Cu and 12% Sn. But how is this percentage defined? Percent by mass (mass fraction)? Or percent by relative number of atoms (mole fraction)?
Jim Luschen- San Diego, California, USA
March 23, 2012
March 25, 2012
A. Hi Jim.
Bronze, and all alloys, and most mixtures are described by mass fraction. Compounds, in contrast, are often described by mole fraction: H2O (water), is two atoms of hydrogen to one atom of oxygen.
I suppose the reason is that chemical compounds react with each other molecule by molecule, whereas mixture proportions are more conveniently described by weight. Sometimes, though, mixtures are described by volume fraction: in making cookies, you might use two cups of flour to one cup of sugar.
Regards,
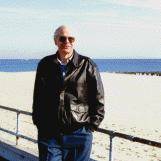
Ted Mooney, P.E.
Striving to live Aloha
finishing.com - Pine Beach, New Jersey
Q. "Moses then made a serpent out of bronze and raised it as a standard, and anyone who was bitten by a serpent and looked at the bronze serpent survived."
How did he do this in the desert living as sort of a nomad?
John Flynn- Sun Prairie, Wisconsin, USA
March 27, 2012
A. Hi John. The bronze age preceded the iron age in every culture; it's not high technology at all, so casting bronze serpents was easy enough for nomads.
However, curing snakebite by lasering an antidote in through the eyes is extremely advanced technology, and is probably better ascribed to divine intervention than to the science skills of an ancient nomadic culture :-)
Regards,
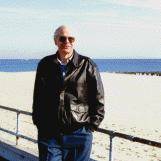
Ted Mooney, P.E.
Striving to live Aloha
finishing.com - Pine Beach, New Jersey
March 27, 2012
Cool!
- Sun Prairie, Wisconsin, USA
March 27, 2012
info... While copper/tin is what's used for making for making Bronze today, copper/arsenic was commonly used in ancient times. In fact it was probably the most common type of bronze in the early bronze age. Arsenic is very poisonous and that's probably why copper/tin bronzes became more common later in the bronze age.
In addition to using homemade charcoal-fired furnaces to melt copper, tin and bronze, you can also build charcoal furnaces to smelt (smelting: To extract a metal from it's naturally occurring ore) copper tin and even iron. Smelting doesn't require temperatures that would melt the metal being extracted. It works by a chemical process called "reduction" where oxygen is removed from the metal oxide in the ore. The reducing agent in these furnaces is the carbon monoxide gas from the charcoal fire.
www.youtube.com/watch?v=Fwo3rNLhlmI
- Tucson, Arizona
May 31, 2012
Q. I am glad I stumbled upon this site as it provides some interesting and verifiable information on bronze casting. I am writing a fiction novel and have been searching for answers to these questions, but I am lacking the proper knowledge of metal working to figure out how the bronze hardens. What I mean by this is that after a sword is cast, it is then worked, or forged by the smith, hardened, for use. I have come across other sites that have shown how late Bronze Age swords were just as effective as early Iron Age swords due to advances in metal working, and increasing knowledge. The answer I have come across seems to be saying that bronze hardens after being worked over with a hammer, the exterior of the metal being harder than the center, making a sword more effective. I guess I am looking more for confirmation that bronze hardens when hammered, effectively tempering the blade.
Dwayne Wallage- Halifax, NS, Canada
June 13, 2012
A. About bronze vs. iron. My understanding is that bronze is quite hard as cast. Early iron, on the other hand, was relatively impure cast iron which is very brittle. Only when forging was invented as a technique did iron become better. However the raw materials are more common. Roman officers had bronze swords while the troops had iron ones, I've been told.
Ian Chandler- Cambridge, UK
September 25, 2012
A. You CAN use pennies to make bronze if they are pre-1982 which are all copper. Then you take a little tin (on top) and put it on a hotplate. I've seen it done before without a fancy kiln or oven type thing. It's fairly simple but just keep in mind that melting pennies IS illegal :D
- USA
December 5, 2012
January 2014
Hi Lexii, although it's theoretically illegal, when the intention is education it's not going to be a practical problem. What would be a big problem leading to prosecution is buying thousands of pennies, melting them down, and selling them for their copper value -- which exceeds their face value :-)
Regards,
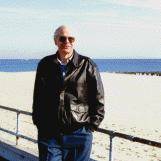
Ted Mooney, P.E.
Striving to live Aloha
finishing.com - Pine Beach, New Jersey
A. I came across a series of three DVDs that explore the process of making bronze, including full do-it-yourself instructions for making a backyard foundry. I found these videos at Survival.com. Respected outdoorsman Ron Hood went to Romania researching the roots of bronze-making. Although I'v not seen this particular video I've watched his primitive knifemaking video that includes making your own forge. His videos are always well done and informative.
http://www.survival.com/?page_id=76
- Louisville, Kentucky, USA
January 20, 2013
----
Ed. note July 2022: Ron Hood has passed away but his wife Karen is carrying on his work.
Q. Hi, I'm 13 and was wondering where did people get the stuff to make bronze at. HELP! I need good answers. Thanks.
Taylor Cave- Dayton, Ohio, USA
May 23, 2013
Q. I have an ornate, many-armed chandelier that was roughly handled and bent. Can I heat parts of it to gently return to its original position. Maybe use a torch? What do you recommend I do to restore it?
Margaret Piper- North Little Rock, Arkansas
January 5, 2014
A. Hi Margaret. And you're sure this chandelier is solid bronze?
Regards,
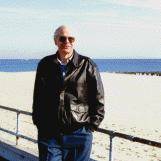
Ted Mooney, P.E.
Striving to live Aloha
finishing.com - Pine Beach, New Jersey
January 2014
Q. I think so, because it is an antique, very old.
Margaret Piper- north little rock arkansas
January 7, 2014
A. Bronze is very brittle and hard to work. If you try to bend your piece around much it is apt to break.
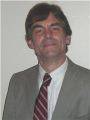
Dave Wichern
Consultant - The Bronx, New York
January 7, 2014
A. Try to heat it to dark red colour; when it is cold try to bend it but very very carefully. Repeat process several times and don't use too much force. Old bronze is very brittle metal. Best approach -- try to find professional metals conservator. Hope it helps and good luck!
Goran Budija- Cerovski vrh Croatia
January 9, 2014
A. The way they learned to make brass in the ancient world happened by a process of elimination. They grew things. And kept them in earthen pots. When sugar goes bad from fruit it creates alcohol which degrades into acid. It changes things in the earthen vessels. By watching they probably dipped different utensils into the pots. Or things just to see what it would do to the thing. By this process you could primitively create brass through electroplating. Which would be improved on over thousands of years. Metal being smelted or superheated and mixed in liquid form was not possible till much later. 6870 years ago till 2018 years ago was a primitive time in most societies and an endeavor like smelting was probably in the infancy of anything we would call a process. 2018 years ago to about 1400 would be the time that I'd focus on to look for advancing metallurgy. And solid metallurgy from 1400 to present.
Matthew Bugg- Wellington, colorado, usa
January 1, 2016
A. You can make a homemade furnace; it's a little dangerous but be safe; wear protective gear as on leather gloves, have proper tongs and safety glasses. You can use charcoal or propane or other gases and make sure to have a good air flow. I use a hair dryer and I would prefer to use a graphite crucible.
Robert h. [last name deleted for privacy by Editor]- Mason, west Virginia, usa
December 8, 2016
Though bronze is most often made from copper and around 10-15% tin you can also make aluminum bronze. Aluminum bronze is a little tougher than regular copper/tin and has a bit more of a 14-22 kt gold color. It's the same process as regular bronze but you use 8-11% aluminum instead of tin. If you have the means you can also add up to 4% nickel and 2% silicon which will also make the bronze more durable.
To produce the amount of heat needed, just under 2000 °F to pour bronze, you can use an old steel rim or old brake drum from the junk yard as the fire bowl, some (ungalvanized) pipe and a T fitting. Find a friend or family member with a welder and weld the fitting to the center hole of the drum or rim so that ash can fall straight out the bottom. Screw a piece of pipe into the horizontal part of the fitting and shove a blow dryer into it. Screw a pipe cap loosely into the bottom hole so the air will travel into the bowl.
Once that is done, put a small metal plate with holes drilled in it over the air supply so your fuel doesn't fall in but plenty of air can come out. Load it with charcoal, coal or smithing coke over a ball or newspaper and light the paper. When it is lit petty good turn the blower on and let it heat up. Getting a coal fire started well take practice and coke is even harder do it's often easier to start the fire with charcoal or wood then add the coke or coal after until you get it figured out. You can also wrap duct tape around the opening where the hairdryer is so you don't lose as much air pressure.
The fire produced is hot enough to melt steel so please be very very careful. I would invest in a clay/graphite crucible, and they are not too Spendy and will make your life easier. Always always always wear eye protection, preferably brazing goggles and a face shield. Always wear cotton or natural fiber clothing like wool because synthetic cloth will melt to your skin; and always use welding gloves when handling molten metal and a larger welding apron. Water is your enemy with molten metals also. Do not quench (cool in water or other liquid) until you are 110% sure the metal is no longer molten. Patience is very important here, kiddos. Always use tongs to remove and pour the crucible. It may not be glowing red but it will burn the meat off your hands down to the bone. I am very sure these guys can fill in what I forgot but have fun and be very safe.
I love hearing about younger generations showing interest in the old metallurgical arts. I'm a blacksmith by trade, making Damascus knives, but at times I cast parts for my knives and just because it's fun. I would love to pass some knowledge on to inquisitive minds. Best of luck kiddos :)
Daniel PriceOwner of Tine Anam Blacksmithing - Mansfield, Texas, USA
December 7, 2017
A. This is an extremely old thread … but if anybody really wants to know how to cast bronze and a couple of recipes search youtube.
opinion! I was looking to increase my bronze making abilities and came across this thread. Horrible how people treat a sponge-like mind …
- Garden City, Michigan, United States.
July 6, 2018
July 2018
A. Hi Phillip. Thanks. But I'd call a thread spanning 16 years and still constantly receiving fresh updates "long-enduring" rather than "extremely old" :-)
Youtube is great, I use it all the time ... but I also see the value in dialogs like this where dozens of people from around the world contribute, so we hear many different perspectives balancing each other, rather than being limited to one person's take on a situation.
I do not understand who you feel treated a sponge-like mind horribly though.
Regards,
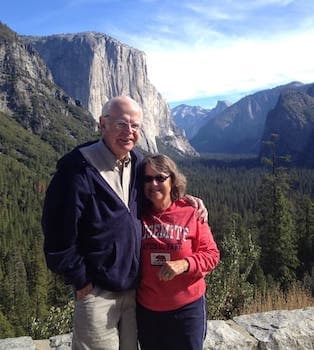
Ted Mooney, P.E. RET
Striving to live Aloha
finishing.com - Pine Beach, New Jersey
Q. Can anyone tell me if adding 90% (by mass) copper plumbing pipe to 10% old pewter tankard will produce a reasonably machinable bronze? thanks in advance ; Paul (50 years old and still learning)
Paul Hucknall- Settle, North Yorkshire, UK
December 4, 2018
A. Hi Paul
That should work but I would melt the copper first and then add the pewter. You will not be able to get the pewter hot enough to melt the copper without serious oxidation of the tin.
Copper melts about 1083 °C tin 232 °C and bronze 913 °C
Assuming the pewter is modern it will be mostly tin and the lead content will help machinability.
The other minor metals in pewter will tend to make your bronze near old formulations where such things were not easily controllable.
But a simpler way might be to visit your local scrap yard and collect worn out bronze bearing shells.
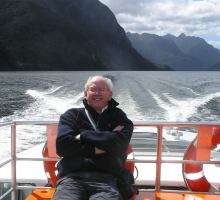
Geoff Smith
Hampshire, England
December 6, 2018
Thanks Geoff,
I will visit a scrap yard, but also try the other as I have a lot of copper and pewter available, although I guess the scrap yard would take the copper anyway...
- Yorkshire, UK
December 8, 2018
I used with my dad an arc furnace which is basically a welder with graphite rods which is more safe, easier and also cheap.
If you don't have such a thing watch this:
child - zilina, Slovakia
July 12, 2021
A. Hi Peter. Easy & cheap is an understatement -- I'm flabbergasted by that video! Thanks!
But 'safe' is a much tougher question. What might be considered relatively safe in Slovakia, and which was considered relatively safe when I was a boy 65 years ago is one thing; but introducing this project to a high school class today might cost an American high school science teacher her tenure :-)
Luck & Regards,
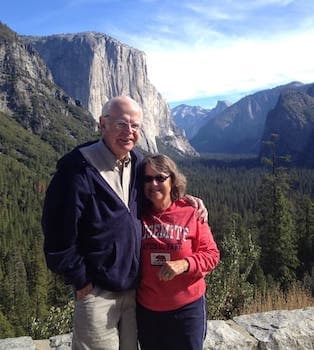
Ted Mooney, P.E. RET
Striving to live Aloha
finishing.com - Pine Beach, New Jersey
July 2021
Q, A, or Comment on THIS thread -or- Start a NEW Thread