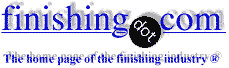
-----
Nickel plating over copper flash

Q. As part of a research project. I am trying to find out when in the history of nickel plating steel was the idea of first flash coating the steel with copper introduced?
I know it is common/standard now, but I've not been able to find a reference for the practice.
Sincerely
Robert
- San Antonio, Texas
July 6, 2022
A. Hi Robert. Unfortunately I don't think you'll find the answer you are looking for as a generic industry-wide practice; you may be better off researching the particular product rather than the whole finishing industry. It is questionable whether a flash layer of copper on steel before nickel plating accomplishes much, and once we have the situation of a process having dubious value, people will start & stop the practice repeatedly, and the history of them doing so is probably quickly lost.
Lowenheim in Modern Electroplating in 1948 claims that copper covers imperfections better and thereby reduces porosity as proven by CASS tests, and he references papers by Schlotter and Macnaughton & Heathersall from 1925 and 1928 ... so somewhere around 1928 is probably when it was first practiced.
Whereas a copper strike before nickel plating is necessary on zinc and may be optimal on aluminum substrates, and whereas a heavy, buffable, layer of copper before nickel on steel may result in a brighter finish, a thin flash of copper on steel before nickel plating? Most people probably don't quite believe the claims anymore, perhaps because of improvements in nickel plating.
It looks like you'll find some references to the practice via a scholar.google.com search but such research articles may not be definitive in terms of what was actually practiced as opposed to what an individual researcher felt was best :-)
Let us know what you find.
Luck & Regards,
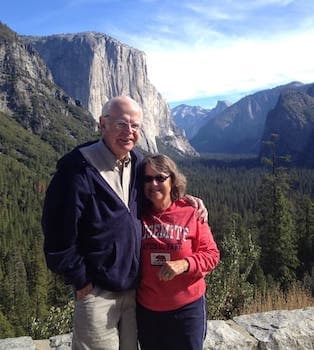
Ted Mooney, P.E. RET
Striving to live Aloha
(Ted is available for instant or longterm help)
finishing.com - Pine Beach, New Jersey
July 10, 2022
Mr. Mooney,
Thank you for your response. A month ago I knew nothing about nickel plating, but an unusual discovery forced me to it.
It began with a 2nd Model Colt Dragoon manufactured ca. 1850. It is for the most part handsomely engraved and has a nice polished finished, most of which remains. You can see it here:
(extracted from the full photoshoot at www.discovercolt.com/samcoltpresentations.html)
The finish is not highly reflective. Some may say muddy or cloudy, but in any event for sixty-years the finish has been said to be silver. Now, if you look at the backstrap and trigger guard you can, given the tarnish, see those are silver. But the frame, barrel, cylinder, etc. are not tarnished.
I came upon an expert's opinion as to the authenticity of the gun in which he said the finish was tin. Colt did make some tin plated guns, though I've never seen one. So what was it? Silver or tin, and did it make any difference as to authenticity?
I took the gun for Xray Spectroscopy and what pops up? Nickel directly on steel. So I started digging into the history of nickel plating. The most helpful current source I found is the March 2021 history of Nickel Plating by Bill Niebolo. https://www.remchem.com/resources/evolution-of-nasf/
Nickel plating in 1850 was done by adding ammonium sulphate to the bath. Adams Plating in 1872 got a better result by adding double ammonium sulphate. Watson in the early 1900s improved things with the Watts bath which included boron and chlorine. Still, a lot of hand labor was needed to get a bright finish. Then Max Schloetter, discovered in 1930 that the introduction of the organic aromatic sulfonate compound; sodium benzene disulfonate, would generate a dramatically improved, hard, smooth, mirror-reflective finish to what was formerly a semi-bright nickel plated deposit.
Curious to see if any of the organics appeared under Xray Spectroscopy, I had examined nickel plated guns from 1872, 1875, and 2012. Of course, they are not elemental so they did not show up. All was nickel on steel except for the 2012 gun that I personally had restored and plated. That gun also showed copper. Against a net count of 121,470 of nickel, there was 1,260 of copper. So, a copper flash plate about one-percent the thickness of the nickel. I'll have to check with the guy to see what we are talking about in actual thickness, but nominal use of copper as a leveler is 150nm or 0.000006 inches.
Colt and Smith & Wesson experts have sworn up and down that the companies never struck copper plates, but the companies say otherwise. Given the thinness of the copper I'm not surprised that you might never see it.
Anyway, I decided my quest was not to look for what's in the nickel plating to date a piece, but to find out when copper strike plating began. It seems that your 1920s date is about right because copper, nickel, chrome was the way to go for automobile bumpers, etc. Schloetter's 1930 discovery was great, but it came right at the depression and when the US began gearing up for WW2 so many metals were restricted for military use only. Copper was no exception. It was needed to make coils for magnets and motors. As you recall we had steel pennies that were zinc plated. That saved 5,000,000 pounds of copper. Not having enough copper to create the coils necessary to separate U-235 from uranium, the army procured 15,000 tons of silver from federal vaults, shipped them to Wisconsin where the coils were fashioned into magnets, and then to Oak Ridge, Tennessee.
During this period, nickel plating guns was not high on anyone's priority list. After the war though, many guns were flashed with copper, nickel plated, and then chromed. Often these were service guns from which serial numbers and US Property stamps were removed by their new owners.
The copper flash improved the nickel throw, but the combined ductility of copper and nickel was not sufficient to prevent the hard chrome from cracking and looking like hell. Gun makers and gunsmiths restoring firearms since then have used copper flash that levels, is ductile, and, importantly, improves adhesion. Local platers as a matter of course flash copper.
In 1960 the Bureau of Ordnance conducted a study of what makes nickel bright. They used the Watts bath and adding various organics. A few things affected the brightness, like the alignment of crystals, but the only constant was that without finely and distinctly shaped crystals (observed at less than 15 microns) you cannot be assured of a bright finish:
citeseerx.ist.psu.edu/viewdoc/download?doi=10.1.1.865.9898&rep=rep1&type=pdf
My guess is that if I look at the 1850 gun under an electron microscope the crystals will be rugged and irregularly shaped. The quest continues.
- San Antonio, TX
A. Hi Bob. I've mentioned my related story on this site before, but I think it's applicable --
I was at one of America's most famous modern museums doing a small consulting project when the museum's metals curator who I was working with had to step away for a few minutes for some reason.
So I was looking at their huge collection of silver plated and nickel plated tea sets & such to pass the time. When she returned I said, approximately, "Some of the silver sets here I would have guessed to be nickel plated, and some of the nickel plated items I would have guessed to be silver" as I'm thinking to myself that I've learned something here about the weakness of trying to rely on the looks of something to determine what it actually is. And she shocks me by saying "If you tell us which ones you think are wrong we'll change the labels". WHAT??!!
There are hand-held x-ray fluorescence instruments ⇦ on eBay or Amazon [affil link] which can non-destructively determine actual metal content, and resolve a lot of questions for you. They are very expensive, probably $40K and up, but they are so crucially important to scrap yards that many or most have them and call them alloy sorter / scrap sorter ⇦ on eBay or Amazon [affil link] . If you have a friend of a friend who works in a scrap yard you can determine whether pieces are nickel, silver, or tin, and whether there is copper beneath ...
In your field and/or at certain times copper was flashed under nickel plating, but today I'm 100% confident that there is far more nickel plated directly onto steel than onto a copper flash. or copper plating.
Luck & Regards,
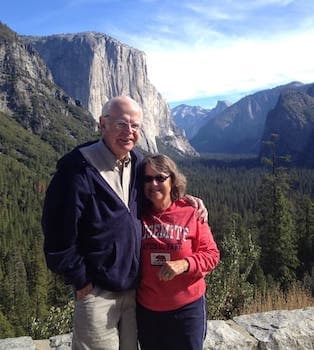
Ted Mooney, P.E. RET
Striving to live Aloha
(Ted is available for instant or longterm help)
finishing.com - Pine Beach, New Jersey
Did they change the labels?
I would agree with you on direct plating, but, for example, restoring well-used guns from the 19th century not every restorer can achieve a great finish. Pitting on such arms could require extensive polishing that would throw the measurements and fits off.
In many instances you can identify replated guns when pitting is over nickel. I'll check with notable restorers to see what they do. Copper as a leveler which can then be polished flat can cover a lot of sins.
As I said Colt still flashes. There are so many nooks and crannies to deal with. They can't remember when they didn't do it.
On some nickel-plated antique Colts I have seen the substrate can be steel, bronze, and brass. Each area looks different. I guess if they thought to copper flash that wouldn't have happened, but they didn't ask me.
Robert Swartz [returning]br> - San Antonio. TxJuly 17, 2022
A. Hi again. I was flabbergasted that there was not a provenance and detailed history on the items in the museum and couldn't believe that people sometimes just guessed at labels to put on museum pieces :-)
.... but I certainly wasn't going to add to the problem :-)
There's no question that copper plating is widely used for 'mush buffing' to try to fill small pits in the classical auto restoration field as well, and I wasn't suggesting that copper flash/plating could or should be dispensed with. I was simply noting, so as to not mislead other readers who might read this page and assume that copper plating is always a necessary step in the nickel plating process that that is not the case.
Luck & Regards,
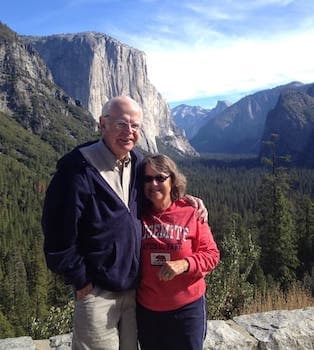
Ted Mooney, P.E. RET
Striving to live Aloha
(Ted is available for instant or longterm help)
finishing.com - Pine Beach, New Jersey
⇩ Related postings, oldest first ⇩
Q. The thickness of nickel is 0.0002/0.0003" over copper flash of 0.000005". Would this type of plating have any corrosion resistance? How long would it take to start corroding?
Is copper flash & nickel, or nickel & chrome plating better?
Peter Wang- Taipei, Taiwan, R.O.C.
2002
![]() |
A. The corrosion protection of nickel over copper flash depends on the basis material in two ways. If it is steel, best corrosion protection is achieved when the metal is smooth. Rough or porous surfaces will not produce good corrosion protection when nickel plating is to the thickness you mentioned. A pore-free deposit would stand hundreds of hours of salt spray (ASTM method). If the basis material is brass or aluminum or zinc special pretreatments would be required. Again a smooth pore free surface is mandatory. If the copper strike-nickel plate is subjected to heat, the copper may alloy with the nickel or the basis metal and result in poor adhesion after heat treating. In this case a minimum of 0.0004" of copper would be required. The copper contributes little to corrosion protection, so the nickel must be of high quality free of particles and pores. ![]() Don Baudrand Consultant - Poulsbo, Washington (Don is co-author of "Plating on Plastics" [on Amazon or AbeBooks affil links] and "Plating ABS Plastics" [on Amazon or eBay or AbeBooks affil links]) A. Electroplated nickel can be columnar or laminar or one over the other. It can be pure as in sulfamate deposited nickel or occluded with organic additives as in so-called "bright nickel". Electroless Nickel can be porous as deposited under poor quality control conditions. All "bare" nickel will corrode in air, first light yellow, then dark yellow, then brown, then black. That is why decorative nickel plating is always topped off with about 30 millionths of chromium - and the automotive industries have all sorts of corrosion data on this subject if that is what you are looking for. "How Long" cannot be answered on the basis of your info, unless you mean conventional automotive nickel plating -- then go to Ford, GM, or Chrysler and you can get exact salt spray data. ![]() Robert H Probert Robert H Probert Technical Services ![]() Garner, North Carolina ![]() |
Q. As a follow-up on my request.
The tube that I am plating has a length of 1.578 ±0.003, od 1.568 ±0.003, id 1.429 ±0.002; material: SAE 1015-1020.
What is the best type of plating:
1. Copper Flash of 0.000005 thick and nickel 0.0002/0.0003 thick.
2. Nickel 0.0002/0.0003 and Copper 0.0002.
Presently I am using the second option, but, we are suffering from flaking / peeling. What sort of testing should I conduct from here?
Peter Wang- Taipei, Taiwan, R.O.C.
2002
A. Hi Peter. There are a couple of different problems here. Copper and nickel are both cathodic to steel. What that means is that they offer strictly "barrier layer" protection, unlike coatings such as zinc which offer cathodic protection to steel. In turn, this means that if there are any pinholes or porosity, these coatings accelerate the corrosion of the steel rather than retard it. For that reason you need either rather thick coatings (automotive coatings are perhaps 10x your thickness) or, as Don Baudrand referred to, a very smooth substrate so your thin deposit can be pore-free.
The second issue is that we don't understand why you have chosen a multi-layer copper and nickel deposit when it doesn't seem to even matter to you which one is done first. The third issue is that flaking/peeling is usually unrelated to corrosion, but related to a poor plating practice: if both the nickel and copper both peel off, the substrate is either not clean or not active; if the copper peels off of the nickel, the nickel probably went passive before you copper plated it. Good luck.
Regards,
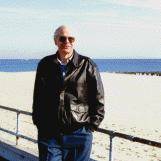
Ted Mooney, P.E.
Striving to live Aloha
(Ted is available for instant or longterm help)
finishing.com - Pine Beach, New Jersey
Q. Hello,
Is plating nickel on copper good for flue gas at 840 °C (using recuperator)? Inside 35 °C, outside 840 °C?
Thanks,
Mahdi
- Yazd, Iran
November 25, 2012
A. If the copper stays at 35 °C it is OK but if the copper gets to over 800 °C it will come right through the nickel and discolor the outside.
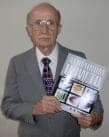
Robert H Probert
Robert H Probert Technical Services

Garner, North Carolina
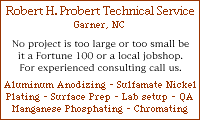
Q. Hi, I am facing the Deposited Nickel over copper plating, the Nickel peeling off during the forming process, the plating thickness is .0002"- .0004" ELECTRO-DEPOSITED NICKEL OVER .00003"-.00005" COPPER FLASH.
Appreciate if anyone can help to solve the problem.
Yuu Guan Seng- Butterworth, Penang, Malaysia
August 25, 2015
A. Hi Yuu Guan. A soft unstressed nickel deposit such as nickel sulfamate will be less prone to this separation than a sulfurized bright Watts nickel plating, but it is not clear to me exactly what you start out with in this "forming process" and what is being done, and therefore whether there is a realistic chance of the plating adhering. More detail would help.
Luck & Regards,
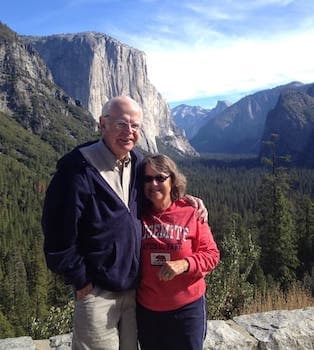
Ted Mooney, P.E. RET
Striving to live Aloha
(Ted is available for instant or longterm help)
finishing.com - Pine Beach, New Jersey
Q, A, or Comment on THIS thread -or- Start a NEW Thread