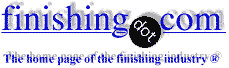
-----
Nickel-chrome plating is peeling off steel tubing
Q. Dear Sir / Madame:
Subject: Plating peeling off.
Plating Used: Nickel and Chrome on SAE 1017 tube.
What is the best way to have nickel plating and chromium plating on carbon steel without having the problem of peeling off?
- Taipei, Taiwan, R.O.C.
2002
A. It absolutely should not peel off. It sounds like you either have not cleaned and activated the tubing, or there is something very wrong with the contact arrangement and you are getting make-and-break and laminar plate.
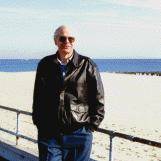
Ted Mooney, P.E.
Striving to live Aloha
(Ted can offer longterm or instant help)
finishing.com - Pine Beach, New Jersey
2002
A. Mike, for carbon steel substrate, most people use ultrasonic clean -- soak -- Electroclean --HCl dip -- electroclean -- HCl dip and rinse -- then cyanide copper strike -- copper plate -- acid copper -- bright nickel -- chrome.
If the parts are oily /grease/ heavily scaled and you cannot remove, then you have peeling problem. First you have to find out if peeling is from base or peeling different layer.
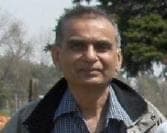
Popatbhai B. Patel
electroplating consultant - Roseville, Michigan
2002
A. Hire a consultant for a week.
James Watts- Navarre, Florida
2002
Jim, I like your reply! Give some info about your preplating cycle so we can try to understand where the problem is coming from.
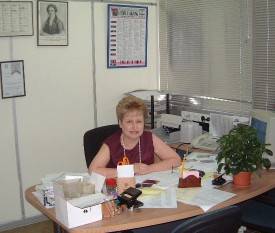

Sara Michaeli
Tel-Aviv-Yafo, Israel
2002
A. May I suggest you monitor the brightener dosage into your Ni bath? Excessive brightener may cause brittleness (although the preferred brightness too), high stress may cause Ni plating peel-off.
Good luck!
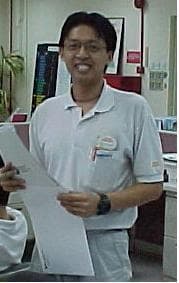
Chee Hong, Lee
- Singapore
2002
The plating on tools is peeling in transit
Q. We are manufacturer and exporter of hand tools, i.e., spanners in India. We received complaints from our overseas customer of the nickel chrome spanners having rusted (due to peel off, small %) as they reach them through sea. When we checked the leftover spanners of same lot lying with us we found not even a single piece rusted or peeled off. Hence we concluded that it has been peeled off during transit through sea's saline atmosphere. Can you explain any reason for this and what precautions should be taken to avoid it in future. We are applying 7 to 8 microns of Nickel layer and 0.4 to 0.5 microns of chrome layer on highly polished hardened chrome vanadium steel spanners.
Krishan Sharma- Jalandhar, Punjab, India
October 5, 2012
A. Hi Krishan. I have from time to time heard of delayed peel-off, but I have personally never heard of a case of nickel-chrome plating peeling because of the environment rather than something having been wrong at the time of plating.
I would try baking some sample parts to see if you can establish a pattern such as: the nickel plating splitting laminarly due to current interruption, or the peeling being in one particular spot where perhaps the polishing compound isn't removed as well. I think things will go better for you if you can see some of the defective parts because parts can certainly rust without peeling, and there may be a translation issue: maybe the parts are not actually peeling, but badly rusting, undercutting the steel that the plating is attached to.
Regards,
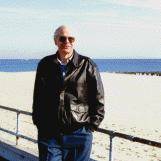
Ted Mooney, P.E.
Striving to live Aloha
(Ted can offer longterm or instant help)
finishing.com - Pine Beach, New Jersey
January 1, 2013
Does threading cause plating to peel?
Q. Dear Sir,
Does threading done after copper plating result in peel off of the material plated?
Please help me.
Engineer - India
January 21, 2013
A. Hi Abhiraj.
Threading would seem to be an extremely difficult adhesion test. Still, the plating can probably be done well enough for adhesion despite the threading. It sounds like an unusual application.
Regards,
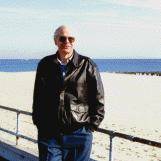
Ted Mooney, P.E.
Striving to live Aloha
(Ted can offer longterm or instant help)
finishing.com - Pine Beach, New Jersey
January 22, 2013
Q. Dear Sir,
Is it possible to carry out threading after copper coating up to 250 microns?
When I try to thread it after copper plating the coating peels off.
Is Dull strike not giving me proper adhesion??
Earlier process was threading, then plating.
Please help.
- India
January 22, 2013
A. Hi again. As I say, this sounds like an unusual application; so I don't know that we'll find any readers who have done it and can answer definitively. Still, you need to provide particulars if you seek more exacting answers. We don't know the substrate, we don't know what you mean by "dull strike", we don't know what kind of copper bath you are using under what conditions, we don't know what kind of parts you are speaking about, or what kind of threads they have, or whether the threads are deeper or shallower than the 250 microns. Thanks.
Regards,
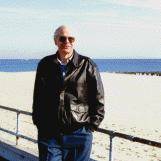
Ted Mooney, P.E.
Striving to live Aloha
(Ted can offer longterm or instant help)
finishing.com - Pine Beach, New Jersey
January 23, 2013
Q. Dear Sir,
The substrate to be plated is a steel rod,
The process we carry out is:
1st the roll threading at the end, then the acid pickling followed by cyanide plating , then the acid copper plating with 225 g/l of copper sulphate, 32 ml/l of sulfuric acid, 70 ppm, and plating up to 250 microns.
Now the problem is that there is masking on the threads and the gauges doesn't pass through out the threads
Now we started to thread the rods after the plating but their is a peel off of the material while threading ... I just wanted to know can it is possible to carry out threading after the deposition up to this much of heavy deposit?
- India
January 24, 2013
A. Hi Abhiraj. I understand now. But my guesses are no substitute for your actual experience in trying it ... and it's not working :-(
If this product is grounding rods, my limited experience is that this business is highly competitive and you will be competing against junk, with rods still having scale here and there, not being particularly clean, etc. If you devise a cycle that offers sufficient adhesion, you might not be able to afford it because of the selling price.
Despite the economic impracticality, I'd probably start by sandblasting some test rods just to see whether the limitation on adhesion is due to low quality substrate vs. the plating quality.
It's possible that a nickel strike in place of the cyanide copper might give better adhesion, and it sounds theoretically possible (but perhaps not practical) to anneal the hard acid copper plating before threading so it's not so chip prone. Is there any possibility of building the cyanide copper to the full required thickness, since it's softer and probably easier to thread?
All I have is ideas to develop, not solutions :-(
Regards,
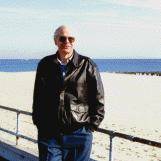
Ted Mooney, P.E.
Striving to live Aloha
(Ted can offer longterm or instant help)
finishing.com - Pine Beach, New Jersey
January 25, 2013
January 30, 2013
Dear Ted,
Thank you for your valuable time and answers you gave.
Actually I am a bit confused, but I think I should do some practical things so that I can achieve that feat.
Hope I can increase the cyanide bath throwing capacity and also to try some etching process before cyanide to get some roughness before plating to get proper adhesion.
I know my earlier question looked stupid but I need to make something new.
I will keep you updating the changes and also the process changes made.
thanks
- India
A. Hi Abhiraj. I have not found your questions to be stupid at all. Moreover, I do not agree with your perceived need for an etching process. Plating adheres by metallurgical bonds, not by mechanical "keying" or "tooth" like paint. My suggestion to try sandblasting was not to increase the roughness but to be certain that all traces of mill scale were removed. Best of luck.
Regards,
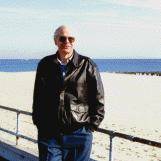
Ted Mooney, P.E.
Striving to live Aloha
(Ted can offer longterm or instant help)
finishing.com - Pine Beach, New Jersey
January 31, 2013
Q. I tried something different.
After plating of the ground rods, I kept the rods for certain period of time and tried to thread and was successful in that process.
But I am not sure as electroplating has uneven deposit on the surface means the coating is not uniform and the nut doesn't enter the threaded portion
So I am worrying about that.
- India
February 9, 2013
Hi Ted,
I tried the process and I got success in that, but it was a sample and I don't know if it will be successful in actual production.
- India
February 11, 2013
Q. Hi Ted,
Does Sulfuric acid make to improve the ductility of the products?
Does it helps to improve the softness of the product?
- India
February 21, 2013
A. Sorry, I do not follow your train of thought.
Regards,
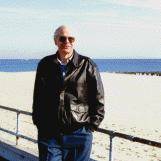
Ted Mooney, P.E.
Striving to live Aloha
(Ted can offer longterm or instant help)
finishing.com - Pine Beach, New Jersey
February 21, 2013
What happens on a molecular level to make plating adhere?
Q. I am a college student currently doing a research project on plating the metal Vanadium. I understand that metal ions in the solution can be reduced and then effectively plated onto the cathode... what I don't understand is what causes those metal ions to "stick" to the cathode. Why do they bind? Why do they not fall off?
In a specific situation:
I am intending to plate the metal Vanadium on a copper cathode. The Vanadium is in the form Vanadium (V) Pentoxide. When dissolved in water, this V (V) forms a V5+ ion. When it gets reduced, it can be reduced several oxidation levels, from 5+ -> 4+ -> 3+ -> 2+, changing colors until it reaches the V(II) Ion. See this video for Vanadium Chemistry -- it's cool:
When Vanadium gets to V(II) it is in its nearly completely reduced form. I'm not sure any lower than that is possible in any stable manner. At what point would this particular metal adhere to a copper cathode? I understand perfectly well how the metal can be reduced from V (V) in an electrolytic reduction, but I am not entirely clue at what point this ion decides to adhere to the cathode and effectively "Electroplate". I did some searching and it is indeed possible to electroplate this metal, though I have not had any luck finding specifics on it. I'm going to take a moment here and assume it is not an overly complicated process.
Any ideas? Suggestions? Explanation for why metals adhere during reduction?
- Cary, North Carolina, USA
January 25, 2014
A. Hi. That's a very good question, John!
I claim above and in other places that plating adheres by metallurgical bonds rather than by "tooth" or "keying", and I'm sure it's true. And we all know that the plating doesn't adhere if the surface of the substrate is greasy or oxidized, although the same reduction process is occurring to the ions in the plating solution. That means that adhesion occurs because a clean and active surface metallurgically interacts in some way with that reduction process ...
But now that you've made me think about it, I realize that I don't fully understand it.
Regards,
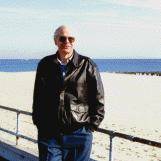
Ted Mooney, P.E.
Striving to live Aloha
(Ted can offer longterm or instant help)
finishing.com - Pine Beach, New Jersey
January 27, 2014
A. Hello John,
I don't have any experience in plating Vanadium and have not seen it done before, but maybe I could answer part of the Electrochemical question you had. When the DC current is applied to the electrolyte, the negative ion gets attracted to the positive electrode (opposite charge). The negative ion loses the electrons it gained from the positive ion during bond formation and becomes an atom. Electrons that are lost are transferred in the outer circuit from the anode to the cathode. The positive ion from the electrolyte is attracted to the cathode where it gains the electrons lost by the negative ion and becomes an atom as well. In addition to the reduction process that Ted mentioned and the importance of a clean and active cathode surface, simply put, the positive charged ions are attracted to the cathode. When I try to explain the reduction process of plating to fellow employees, they ask me if I could repeat that in English, so I give them the condensed version!
Process Engineer - Malone, New York USA
January 27, 2014
January 27, 2014
A. I'm going to mostly defer to the Wikipedia article on "Metallic Bonding" for this one, but to state it quickly, a metal atom that is missing electrons will want to be an ion floating free in solution, and a metal atom that has all its electrons likes to share with other metal atoms.
In an electrochemical situation, the cathode is providing excess electrons, and any metal ion that happens to bump into it will grab some and eventually work its way back down to a zero valance. At which point it doesn't want to be in solution anymore, and it's already sitting on a big piece of metal, so it decides that's a nice place to be and joins in with the existing metallic bonding there.
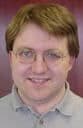
Ray Kremer
Stellar Solutions, Inc.

McHenry, Illinois
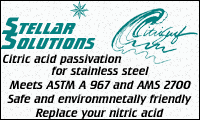
A. This surface deposition subject is very academic in nature. If you would like to explore further, try these keywords- electrocrystallization, electronation, adion. John O'M. Bockris was among the forefront in this area.
The theory was too hard for me. For all I remember, it surprisingly resembles thermal process. Metal ions need to cross "double layer" to reach the surface of electrode in a similar fashion that solute atoms need to cross diffusion layer in solidification model. Once the ions reach the surface, they exchange charge (electronation) and become "adions", looking for favorable sites to deposit. This is surface diffusion phenomena. The favorable sites turn out to be dislocations. This in then a part of electrocrystallization, which looks very similar to crystallization from vapor phase. A metallic bond develops from there.
- Warsaw, Indiana, USA
January 28, 2014
Semi-Bright Nickel Plating Cracks and Peels off after Hammer Test
Q. Hi experts, We are facing issue (Crack and peel off) on semi-bright nickel plating. Usually peeling due to poor pre-cleaning or very high pH. But this both are perfect in our process. There is no deviation from our control spec. PEEL OFF TAKES PLACE ONLY ON THE CRACKED AREAS. We are following the procedure for hammer test. Can anyone explain how to improve our process and solve crack issue.
Note: We are using Nickel sulphate process. Please do not suggest sulfamate or any other process. Thanks in advance.
Plating shop employee - SINGAPORE
November 5, 2014
A. Hi Gandhi. It seems that your plating is very highly stressed (perhaps due to excess addition agents). I would suggest running "stress tabs" (a comb-like Hull Cell ⇦ huh? panel, masked on one side) or some similar stress test.
Regards,
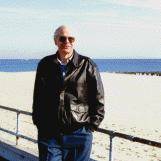
Ted Mooney, P.E.
Striving to live Aloha
(Ted can offer longterm or instant help)
finishing.com - Pine Beach, New Jersey
November 2014
Q, A, or Comment on THIS thread -or- Start a NEW Thread