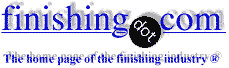
-----
Gemba Kaizen and 5s
Q. I'm a student of university, and now I'm doing my final paper. I really interested in kaizen and 5s I want to ask about what the relation between gemba kaizen and 5s. Thank you for answering and I'm sorry for my English
Tri Rahayu K [last name deleted for privacy by Editor]- Surabaya, Indonesia
2001
2002
A. A term commonly used in Japan is gemba kaizen. It is an expression that conveys commitment to continuous improvement of practices and processes as a business philosophy. Translated to English "gemba" means shopfloor and "kaizen" means continuous improvement. This certificate prepares students/workers to actively participate in implementing ongoing, world-class manufacturing activities necessary to keep their company globally competitive now and into the future.
The term "gemba" was introduced to Westerners by Masaaki Imai in 1997 to describe the "real place" where products are developed and made, and where services are provided. Small kaizen enhancements to these key operations will multiply into greater success and profits many times over. One of the more attractive features of gemba kaizen as a management philosophy is its independence from technology, complex procedures, or equipment, because gemba kaizen techniques focus on techniques like total quality management, just-in-time, total product maintenance, and visual management to deliver maximum quality. For some companies, gemba kaizen has become a leading philosophy for implementing "lean thinking" into their processes and products. The result has been elimination of waste (in terms of materials, effort, money, time, etc.) and an improvement in fiscal performance. Not surprisingly, gemba kaizen's approaches to eliminating waste are also one of the easiest and least costly steps to take in improving environmental performance.
The concept of gemba management has its own "golden rules", and the first rule is: when a problem arises, go to gemba first. Much of what occurs in gemba can be passed off as routine, repetitive, and even boring work tasks, but it's amazing how often we tend to overlook the importance of understanding the processes in gemba to financial and environmental performance. To take the concept of gemba performance to its ultimate level of simplicity, gemba kaizen offers the "5S" steps of good housekeeping:
Seire: Distinguish between necessary and unnecessary items in gemba and discard the latter.
Seiton: Arrange all items remaining after seiri in an orderly manner.
Seiso: Keep machines and working environments clean.
Seiketsu: Extend the concept of cleanliness to oneself and continuously practice the above three steps. Shitsuke: Build self-discipline and make a habit of engaging in the 5S by establishing standards.
Western companies typically modify the above approach into the following 5S:
Sort: separate out all that is unnecessary and eliminate it.
Straighten: Put essential things in order so that they can be easily accessed.
Scrub: Clean everything -- tools and workplaces
-- removing stains, spots, and debris and eradicating sources of dirt.
Systematize: Make cleaning and checking routine.
Standardize: Standardize the previous four steps to make the process one that never ends and can be improved upon.
If you've been pondering what steps to take to improve environmental, health, and safety performance as operating budgets continue to tighten, go to gemba.
Kartikey B [last name deleted for privacy by Editor]- India
Multiple threads merged: please forgive chronology errors and repetition 🙂
Q. Hey folks,
I am looking at some very comprehensive information about 5S. If any of you have done a project in 5S in a company I am hoping if I can get some of the details.
Anshuman Mehrotra- Knoxville, Tennessee, USA
2002
2002
Dear Anshuman Mehrotra,
I herewith reproduce what I have seen in a website www.tpmonline.com
Based on Japanese words that begin with 'S', the 5S Philosophy focuses on effective work place organization and standardized work procedures. 5S simplifies your work environment, reduces waste and non-value activity while improving quality efficiency and safety.
Sort ø (Seiri) the first S focuses on eliminating unnecessary items from the workplace. An effective visual method to identify these unneeded items is called red tagging. A red tag is placed on all items not required to complete your job. These items are then moved to a central holding area. This process is for evaluation of the red tag items. Occasionally used items are moved to a more organized storage location outside of the work area while unneeded items are discarded. Sorting is an excellent way to free up valuable floor space and eliminate such things as broken tools, obsolete jigs and fixtures, scrap and excess raw material. The Sort process also helps prevent the JIC job mentality (Just In Case.)
Set In Order (Seiton) is the second S and focuses on efficient and effective storage methods. You must ask yourself these questions:
What do I need to do my job? Where should I locate this item? How many of this item do I need? Strategies for effective Set In Order are painting floors, outlining work areas and locations, shadow boards, and modular shelving and cabinets for needed items such as trash cans, brooms, mop and buckets. Imagine how much time is wasted every day looking for a broom? The broom should have a specific location where all employees can find it. "A place for everything and everything in its place."
Shine: (Seiso) Once you have eliminated the clutter and junk that has been clogging your work areas and identified and located the necessary items, the next step is to thoroughly clean the work area. Daily follow-up cleaning is necessary in order to sustain this improvement. Workers take pride in a clean and clutter-free work area and the Shine step will help create ownership in the equipment and facility. Workers will also begin to notice changes in equipment and facility location such as air, oil and coolant leaks, repeat contamination and vibration, broken, fatigue, breakage, and misalignment. These changes, if left unattended, could lead to equipment failure and loss of production. Both add up to impact your company's bottom line.
Standardize: (Seiketsu) Once the first three 5S's have been implemented, you should concentrate on standardizing best practice in your work area. Allow your employees to participate in the development of such standards. They are a valuable but often overlooked source of information regarding their work. Think of what McDonalds, Pizza Hut, UPS, Blockbuster and the United States Military would be without effective work standards.
Sustain: (Shitsuke) This is by far the most difficult S to implement and achieve. Human nature is to resist change and more than a few organizations have found themselves with a dirty cluttered shop a few months following their attempt to implement 5S. The tendency is to return to the status quo and the comfort zone of the "old way" of doing things. Sustain focuses on defining a new status quo and standard of work place organization.
Once fully implemented, the 5S process can increase moral, create positive impressions on customers, and increase efficiency and organization. Not only will employees feel better about where they work, the effect on continuous improvement can lead to less waste, better quality and faster lead times. Any of which will make your organization more profitable and competitive in the market place.
Kaizen = Continuous Improvement Enrique Mora (a) Papá Kaizen
One of the key elements for the implementation of the good philosophies of Lean Manufacturing is without a doubt the "Kaizen Event". Kaizen is, as many of you know, a Japanese word meaning "Continuous Improvement". . Actually, a Kaizen Event can be set in a few hours or a few days, but the results are so fulfilling, that the people directly involved in it will keep doing their best in order to increase the good results. It is a matter of conditioning to the rewards.
My friend Bob Rosinski explained to me how a 3 ton. whale can jump 20 feet out of the water with astounding precision. She is conditioned to the rewards of success. The first jump was just a few inches when she was a baby, but the piece of fish the trainer offered as a reward was delicious. Then, she kept finding out that in order to keep getting rewards, she should have to jump higher and higher all the time. Later, there is the fish and the applause, double reward! If the bar she has to jump goes ?" higher each time she will just not notice. Of course there is a limit to everything. Well, in these times of global competition, all the people who want to stay in business are having to learn the very same lesson. The marketplace is the bar that we have to jump and reach in order to keep getting the rewards. And there is no doubt, the bar is raised constantly by the fierce competition. If we want to play in the big leagues, if we want to keep our share in the market, our performance must be among the highest standards possible.
Kaizen Events when repeated have three effects equally beneficial: They generate PROFIT, SAVINGS and perhaps the best of all, they GENERATE A HABIT OF SUCCESS. The habits create a culture and that is what lean manufacturing and other best practices are all about.
Prabhu Ram- India
A. I think you will find that 'Gemba' was introduced to westerners long before 1997, in the UK we have had Japanese manufacturers for more than 20 years. Things like Gemba kanry and Gemba Kaizen were implemented in the UK as soon as the factories were set up.
Phil R [last name deleted for privacy by Editor]- Newcastle, UK
2004
Q. I have heard about Six S in reference of 5s. Is this Sukam (Habit)? Please arrange to send the related information,
Regards,
- NOIDA, INDIA
2005
----
Ed. note: Sorry, we don't "send" information nor offer 'matchmaking' services for others to send stuff back & worth, Vivek. But what we do offer to do is to make any non-commercial information which is sent to us available for everyone to download.
Q, A, or Comment on THIS thread -or- Start a NEW Thread