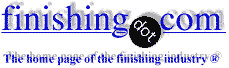
-----
15-5PH Heat Treated to H-1075 Rusting Hex Flats after Passivation
2002
I am in search of a solution to alleviate rusting hex flats of
15-5PH per AMS5659 heat treated to H-1075 after passivation. We manufacture hydraulic fittings for aerospace. These are our facts thus far:
1. Utilizing 15-5PH Hex Bar (12'R/L) sizes 1/2 - 2".
2. Heat treating to H-1075
3. Machining Fittings (Hex's only unmachined surface)
4. Cleaning heat treat scale by: grinding, sanding or ball burnishing.
5. Passivating per QQ-P-35C (canceled) [link is to free spec at Defense Logistics Agency, dla.mil] type II (type VIII is optional but we have not utilized this)
6. Verification sample testing of passivation via copper sulphate
⇦ on
eBay or
Amazon [affil link] or
2hr salt spray.
Problem: Our parts are not passing the verification test. Hex flats may appear bright and shiny or slightly gray but fail testing and develop iron oxide visible to eye over a period of a month or two. Action: We cut 2 samples of heat treated bar, bead blasted one and grit blasted the other. Passivated both and both failed the verification test. Grit blasting caused hex finish to be Non conforming to spec. Must be surface finish of 250 or less and bright shiny to gray due to passivation. Question: Can anyone give us insight into what our failing point(s)may be? Cleaning, Passivation type, Heat scale...? and what would be a cost effective solution. The part in question is of high quantity and we are attempting to avoid utilizing round bar and milling fitting to hex.
Thank you!
- Anaheim, California
Deborah,
You might try checking the blast media itself. We are one of the shops using the round bar to milled hex process, and have found that aluminum oxide sanblasting media can have high concentrations of iron oxide in it. The result is embedding the iron into the stainless and thus having it show up after passivation.
Williams Tool Inc. - Chadwicks, New York
2003
Q, A, or Comment on THIS thread -or- Start a NEW Thread