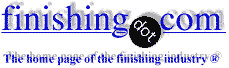
-----
Using SNAP AM -Macdermid- as wetting agent for nickel sulfamate
In production of stamper matrix we use SDS (sodium dodecyle sulphate) as wetting agent for nickel sulfamate. The use of SDS causes two problems : a lot of bubbles in the bath and tensile stress on stamper -I think- especially after activated carbon treatment each six months. The quantity of SDS used in the bath of 400 liters of electrolyte is 0.02 g/l about eight grams. Now we want to use SNAP AM (MacDermid) but we haven't any idea about quantity to use as first in the bath and how to maintain this after many days of production.
BENAMER Mohamed- ORAN, ALGERIA
2002
The first thing to do is ask the guys wearing the funny jackets!(Your Macdermid representative.) The SNAP series, original the "Barrett SN" process, has several addition agents, some for Anode corrosion(Bromide), some for Antipit wetting agents(Surface Tension reducer), and some for grain refinement(stress reducers & hardeners). I believe(?) the product you specified is a liquid wetting agent for an air agitated processes and in the past has been formulated to run at about 0.5% v/v. The powders run at about 0.5oz/gal, If no local vendor help is available, what you need to do is Carbon your bath, then off to the side, using either a "Stalagnometer" (available thru ACE Glass, Inc.) or a set of Rings, make a calibration curve for your bath of a suitable Surface tension variable vs. the additive concentration. Surface tension below 40 dynes/cm is fine to shut down pitting. This can be calculated from the Stalagnometer procedure. You may still require a stress reducer additive, but properly run, this process should be able to hover (theoretically) within ± 3000 or so PSI from Zero stress condition. 3000 sounds like a big number but its really very small as internal stress numbers go.
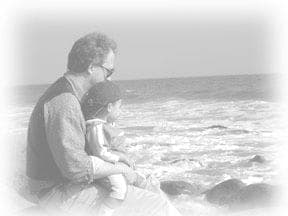
Dave Kinghorn
Chemical Engineer
SUNNYvale, California
2002
Q, A, or Comment on THIS thread -or- Start a NEW Thread