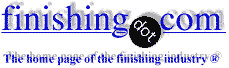
-----
How to plate the bright nickel on brass parts
Q. How to plate bright nickel over the brass parts? We have soak cleaner, electrocleaner, power acid (sulfuric acid 10% by vol), Wood's nickel strike and bright nickel. What is the plating cycle to plate nickel over brass parts?
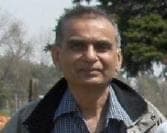
Popatbhai B. Patel
electroplating consultant - Roseville, Michigan
2002
A. Brass used to manufacture parts usually contains lead as a machining aid. Sulfuric acid and hydrochloric acid form insoluble compounds with lead in the surface of the brass resulting in a star dusting type of appearance in the bright nickel. One cycle that works well is mild alkaline clean, rinse, acid dip in either sulfamic acid 4-5 oz/gal. or fluoboric acid 6-10% by vol., rinse, copper strike (either cyanide or fluoboric acid copper) 1-2 minutes, rinse, acid dip in sulfamic acid 4 oz/gal, rinse, and nickel plate.
Note: cyanide copper strike will accumulate lead in the solution. Small additions of sodium sulfide will precipitate the lead to be picked up in the filter. Do not add a large excess of sulfide.
Either process will result in a clear bright finish.
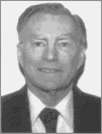
Don Baudrand
Consultant - Poulsbo, Washington
(Don is co-author of "Plating on Plastics" [on Amazon or AbeBooks affil links]
and "Plating ABS Plastics" [on Amazon or eBay or AbeBooks affil links])
2002
A. There seems to be no problem with the process that you are following. The Wood's nickel strike also may not be required, but I would recommend using a dilute HCl predip after the alkaline cleaners instead of the H2SO4 if brass is the substrate.
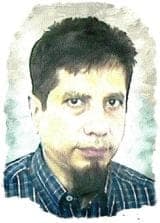
Khozem Vahaanwala
Saify Ind

Bengaluru, Karnataka, India
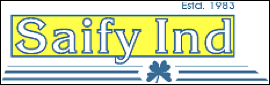
2002
A. Hi Popat Patel,
Your pretreatment cycle is perfect. You don't need a nickel strike. sulfuric acid should work well and acid concentration also is good. If your plating the parts with watts nickel which has both nickel sulphate and nickel chloride you can use either sulfuric or hydrochloric acid for activation. Both works equally well. If you want to improve your cleaning you can introduce solvent cleaner preferably with ultrasonic effect. If the brass parts are tarnished it can be dipped in 5% sodium cyanide solution.( optional, not a must)
Venkat Raja- Kitchener, Ontario, Canada
2002
A. I would agree with Don, but lean towards the fluoroboric acid option. Note: this is an immersion dip not electrolytic.
Gene Packmanprocess supplier - Great Neck, New York
2002
Cu underplating needed for Ni plating on brass?
Q. For a brass terminal (terminal A) in an electrical connector for an automotive sensor application we use 1-3 µm Ni plating. A similar brass terminal (terminal B) has 2.5-5.0 µm Ni over 0.75-2.50 µm Cu preplating.
1) What could be the reason for using a Cu preplating under Ni?
2) What would be the risk (if any) if I would increase the Ni thickness of terminal A to 2.5-5 µm without a Cu underplating?
Design Engineer - Hengelo, The Netherlands
October 8, 2018
A. Hi Jaap. Although most people recommend copper plating before nickel I don't think copper plating is absolutely required. My own theory of why it's often worthwhile is that there are many different 'brasses', plus when you have rather thin plating you are liable to get a pin-hole, especially in the case of nickel which sometimes gets gas pits; but the chance of having a pinhole at the same spot in two different plating layers is much smaller. So the chance of exposed brass and corrosion spots may be smaller with the copper plating.
If 2.5-5 µm of nickel is free of pinholes, as determined from salt spray testing, I think it will offer better protection than a layer of copper followed by a thinner layer of nickel.
Regards,
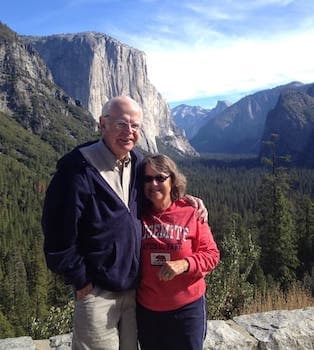
Ted Mooney, P.E. RET
Striving to live Aloha
(Ted can offer longterm or instant help)
finishing.com - Pine Beach, New Jersey
October 2018
Q. Hi Ted,
Thank you very much for your reply.
Just to confirm. The Cu underplating would be intended for corrosion protection not to improve adhesion of the Ni layer? Is there a risk of adhesion problems (or flaking) with a 2.5-5.0 µm Ni layer?
Best regards,
Sensata Technologies - Hengelo, The Netherlands
October 24, 2018
A. Hi Jaap. I can only give you my understanding, not ultimate non-challengeable fact :-)
If the brass is leaded, it requires fluoride-bearing acids; and in that case many platers prefer the next step to be copper fluoborate plating. But assuming that the brass is not leaded, nickel plating adheres well.
Please note that this is not a consulting service where studies and investigation are undertaken on your behalf, but a public forum where people share their experience and opinions :-)
... the idea is that if any reader disagrees they will hopefully chime in :-)
Good luck.
Regards,
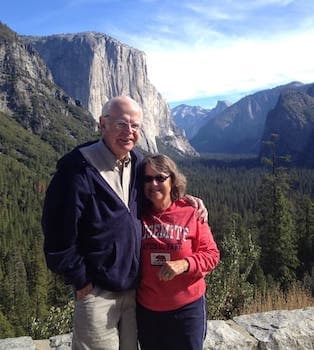
Ted Mooney, P.E. RET
Striving to live Aloha
(Ted can offer longterm or instant help)
finishing.com - Pine Beach, New Jersey
October 2018
Q. Hi Ted,
Thanks again for your reply.
The terminal supplier is using C2600 brass which has a Pb content <0.05%. Would that be considered a brass type without Pb for plating purposes?
Best regards,
Sensata Technologies - Hengelo, The Netherlands
October 24, 2018
A. Hi again. My understanding is that per recent California legislation, <0.20% is considered lead-free brass. I would certainly not expect <0.05% to require special processing due to lead content.
Regards,
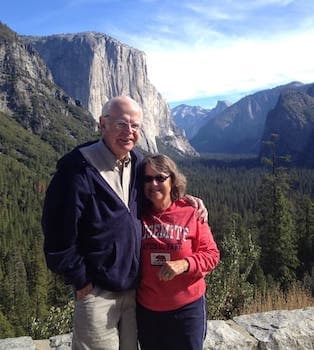
Ted Mooney, P.E. RET
Striving to live Aloha
(Ted can offer longterm or instant help)
finishing.com - Pine Beach, New Jersey
October 2018
Q. I am looking for brass grade(copper casting alloy) that can be effectively nickel plated (satin nickel plating, to be precise). C84400 looks like a good option for now. I need advice in this case - whether C84400 is the right choice or do I need to know about a better alternative? Our product doesn't have high strength operation; however, corrosion resistance is desired. Also, how difficult/easy is nickel plating on Brass as compared to other metals like copper or aluminium?
Hiteshree Pawar- India
August 17, 2019
Drinking Water System Components - Health Effects
NSF-61
[Amazon affil link]
A. Hi Hiteshree. C84400 is a highly leaded brass (6%) but is very plateable. This thread and others suggest that fluoboric acid should be used in the preplate cycle. Most plating shops should be able to handle it, whereas plating onto aluminum or stainless steel can be difficult.
You didn't mention what your product is, but if it contacts food or drinking water, the C84400 might not be acceptable. See NSF61 or similar standards.
Regards,
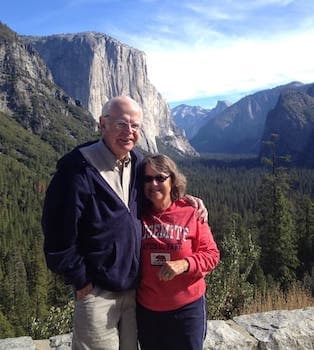
Ted Mooney, P.E. RET
Striving to live Aloha
(Ted can offer longterm or instant help)
finishing.com - Pine Beach, New Jersey
August 2019
August 26, 2019
Hello Ted,
Thanks for the response.
My product is used as an indoor decorative electrical fitting. So I suppose the case with food and drinking water shouldn't be an issue. In any case, I will check out NSF61.
Thank you for the suggestion.
Sigma Electric Mfg. Pvt. Ltd. - Pune, India
Q, A, or Comment on THIS thread -or- Start a NEW Thread