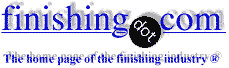
-----
Effluent streams....
1998
We have recently refurbished a couple of evaporation units (meaning they aren't working at optimum of course) in answer to a need to establish a "closed loop".
We use a counter-flow/ drag-out method of rinsing chromated and non-chromated aircraft parts. We are trying to evaporate drag-out from our Alodine process and our deoxidizing process. The need to keep our CrO3 in control is and has always been obvious. The need to keep our deox. under control stems from first) Boeing's limits toward cleanliness, ppm, etc. second) a dragout that is very quickly contaminated with the heavy metals associated with aluminum alloy. (Zinc in particular)
We have just hired a chemical engineer to make observations and help us come well within compliance of WA state tolerance. He mentioned that evaporation could be a bear (maybe not worth the energy, resources, etc.). He also mentioned that some shops have made it work quite successfully. He also said that now was the time for me to make any suggestions I might have.
Being myself, who can be considered completely inept in the science that encompasses chemical engineering, I seek any information to bring myself up to date with a concern that has, somehow, fallen into my lap. I'm enticed and curious enough to beg for information about evaporation, effluent standards, methods of reduction, etc.
Any references or advice that can be given will be well taken. The chemical answer man will leave soon and then it will be up to us to decide the future of our shop and our environment.
Thanks in advance, for those willing to help and spread the wealth of knowledge, literature, links, etc.
Please help me be more green.
J.A.
James A. CorierJames:
There's a lot involved in waste reduction and treatment. You might want to consider taking an AESF waste treatment course.
One issue you need to recognize in your case is that deoxidizing and chromating baths are not "equilibrium" type processes like plating baths, where you might expect the bath to last indefinitely with maintenance additions. Rather, they are chemical reaction processes where the chemicals are exhausted by each load that passes through them. Purifying the rinse water for reuse is okay, but the concentrate you would be returning is not etching solution or chromating solution, it is largely chemicals that have reacted as desired and are now exhausted garbage. Does it really make sense to pour this exhausted garbage into your process baths?
But if you decide that the dragout is in fact garbage and you don't return it, then you are using the evaporators to concentrate waste. I know of a shop that was criminally prosecuted for using evaporators that way, on the grounds that such use made them an illegal treatment and disposal facility. While the charges were eventually dropped, it was not before they went through agony. To insure yourself against that, you would need to get your local regulators to sign off on what you would be doing, and I think you'll have trouble doing that.
My reply is of course a generic one, not based on the specific facts confronting you, and worth what you paid for it; but I don't think I would use evaporators on deox and chromate tanks in most cases regardless of how much or how little they cost me. I think I'd use ion exchange.
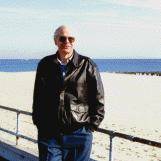
Ted Mooney, P.E.
Striving to live Aloha
(Ted can offer longterm or instant help)
finishing.com - Pine Beach, New Jersey
1998
1998
Mr. Mooney is correct.
Several years ago we went to a zero discharge line with evaporators.
We are now using new rinse technology. Our water cost as raw water has gotten larger, clean and ultraclean water is really expensive and waste water has the high cost and the problems Mr. Mooney mentioned.
I think you are correct that water was so cheap and so plentiful for so long that no one ever really figured out how to use it efficiently. Inefficient use of water means large tanks and huge flows. All common measuring techniques are based on these situations because this is what has always been common.
The mathematics of rinsing is fairly easy. the practical actually follows the mathematics better in rinsing than in many other disciplines.
There is now retrofit equipment to modify existing rinse operations without a need for additional floor space. We are working with Sematech for electronics mfg and were wondering if the plating industry was interested.
I would be more than happy to talk to you in any case.
Tom WalzNW Research Institute, Inc.
1998
I agree with the previous answers, but there are also ways to eliminate your discharge if you are willing to have concentrated wastes hauled off-site (to a properly licensed disposal contractor). Many aircraft finishers are doing some version of this.
If you are interested in doing this, then there are several steps to consider. First, you need to recycle your rinsewater; next use your evaporator(s) to concentrate any wastes from process dumps and the water recycling system; lastly, haul away any process dumps and evaporator concentrate.
If you do this, then you should also investigate using an acid purification system for the deox solution in order to minimize the wastes from it. The Alodine solution cannot be purified since it is a proprietary formulation; as previous responders have pointed out, it depends upon dragout to prevent an undesirable build-up of contaminants.
This probably isn't the solution to your problem that you were hoping for, but , it is one that works.
Lyle Kirman- Newbury, Ohio
Hi James,
Zero discharge is difficult to accomplish and most of the time not cost effective. It sounds like you are taking the rite steps. What type of quality rinse waters are required? I would love to talk to you about your concerns. I do work for a company that can help you with your situation, but unless a lot of work is involved, we consult for free.
Bill Banham- Newbury, Ohio
1998
Don't overlook pretreatment to applicable discharge standards and then sewering the rinse water. Its often cheaper and simpler than any water recycling. Remember, you're not in the water recycling business. Its just one possible solution to a problem.
Ken Rosenblumfinishing shop - Minneapolis, Minnesota
1998
1998
I hear you...we are doing a similar process, and are a WA state company and involved with their (DOE) Waste Minimization/pollution prevention programs. We have had some success, reducing rinsewater usage by 2/3 and our chemistry bills are lower, yet over 2 years our production is up considerably. The process can work, but it involves considerable pain, much persistence and some sheer dogged endurance. Suggestions: consider that deoxidizing and chem film are two different types of processes, the former is a subtractive process, and chem film is an additive process. You are probably using an iron accelerated, nitric-based deox. Hydrogen peroxide adds will help convert the iron back to its original form (bench test it, but a gallon to 500 gallon tank is about right). Use 4-stage counter-flow rinsing and you will use less water. Actually, if it is all rack work, and you can deal with "blind holes" convert your dragout tank to a bottom draining open spray rinse tank. spray for 10 seconds, let drip, and then hit it three more times. Make this spray rinse DI water, and you will go a long way toward preserving your chem film bath from incidental drag-in. (My first experience with this concept of rinsing is on a zinc rack line we have...we run three tanks 24 hours a day, and all rinses are like this...we use only about 200-300 gallons per day, in very little space). Your deox probably is not heated, so you can't recover it directly, but you have much less to deal with. As far as the chromate, you can try pumping your drag out tank to a designated cone tank...react with sulfuric to pH 2.5, treat with metabisulfite, raise pH to about 8.5-9.5, and your hex chrome will drop out. I know of a company that then returns the decanted water back to the drag-out tank, metal free. There is also a company called Solmetex that has an adsorbent filtration system for hex chromate rinses, being used in the Boston area. I just received some of their material and will be trying it in a re-circ mode on my chromate rinses. To keep contaminants from building in your chromate tank, besides DI spray rinsing, you might consider using about a 5-10% nitric pre-dip. Zinc platers do it as a matter of course to remove some of the brightener agents (only at 1/2% concentration) and "polish" the zinc plate prior to chem film. I have a gold chem film for zinc bath that has been run for nearly three years, and still performs well. I think it has to do with a very clean part always going in the tank. I am hoping that implementing this will help for our aluminum chem film bath too. It is important to keep your nitric pre-dip clean...it is easier to treat that though, than hex chromate. Four stage rinsing helps, or free drain spray rinses. If you run your chem film at 100 °F, and put a bottom heater in your spray tank, leaving about 6 inches in the bottom you could conceivably recover it back to the chem film tank. Also a tank-top spray misting "ring" of nozzles, plus slow withdrawal from the tank, and racking your parts so that they have a good "drip tip" will minimize what is dragged out. This helps whether you are spray rinsing or dip rinsing. We platers/anodizers really have to overcome a lot of inertia in our industry practices. I guess the bottom line is to keep the chemistry in the tank, and use as little water as possible to rinse off what does come out on the part, but then return that or recover it. Only as a last resort do we "treat" it. Bath filtration, periodic decant of small quantities, etc. and good DI rinsing of the parts before they go in the process bath help too. Good luck!
Mike SolvieQ, A, or Comment on THIS thread -or- Start a NEW Thread