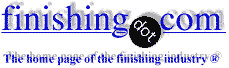
-----
Calculation of aluminum circuit board trace required thickness/size
Q. I have to deposit Aluminum and I know its width is 400 micrometer and I want to calculate the thickness of the deposition so that the Aluminum can carry 3.5 Amps and I have no details about the length of the deposition.
Please help me out.
Texas Tech University - Lubbock, Texas
2002
![]() |
A. I am 100 % positive that you can find data on the load capacity of aluminum in the TT Library. - Navarre, Florida A. I assume you are designing a circuit! Your concern needs to be current density and not length. Your spec of 3.5 A is a very high current to be carried by a 0.4 mm Al strip. If you don't use enough thickness, you will experience "electromigration". Check some literature on that subject. A lot has been studied and published in the context of ICs and hybrids. - Fort Collins, Colorado A. In the macro world we use about 600 Amps per square inch of cross section as a good safe rating for aluminum. That probably has very little to do with the answer you need for your micro device, but there it is for reference :-) ![]() Ted Mooney, P.E. Striving to live Aloha (Ted can offer longterm or instant help) finishing.com - Pine Beach, New Jersey |
Q. Dear James Watts, Mandar Sunthankar, and Ted Mooney,
I would like to Thank you for your valuable comments and I have used the current density to find the thickness and I am enclosing the solution with this.
I request you to review this and comment on any possible mistakes in this calculations.
Thanking you Very much
Aluminum is 400 Microns wide, how thick it has to be to support
3.5 Amps?
Width of Aluminum is 400
Required Current I = 3.5 Amps
Operating voltage 3.3 V D.C
I assume J ( Current Density ) to be 10 e 5 A/cm2 = 1 milli Amps per Micro Meter Square
I = 3.5 A
J = I / A
A = I / J
3.5 / 1 10 -3
A =3500 Micrometer Square
A = W * T
W = 400 Microns
So T = 3500/400 = 8.75 Micrometer ( Micron )
- Lubbock, Texas
A. Hi, Gangadharan. Your conversion factors and math appear correct.
So, assuming the allowable current density is 100,000 A/cm2 as your calculation asserts, then 8.75 micrometer thickness would be the correct answer.
But I don't think that your allowable current density can possibly be correct. I don't have experience in this field, but it sounds a good 10X too high to me, even for copper let alone aluminum, based on some quick reading.
Regards,
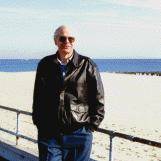
Ted Mooney, P.E.
Striving to live Aloha
(Ted can offer longterm or instant help)
finishing.com - Pine Beach, New Jersey
Q, A, or Comment on THIS thread -or- Start a NEW Thread