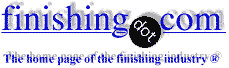
-----
Hydrogen embrittlement of brass
Q. Need to determine if a certain issue is caused by hydrogen embrittlement. Currently have spring tempered brass pins breaking and plating cracking during a bending operation.
Process steps: 1) S.T. Brass pins soldered in housing, 2) housing and pins nickel plated (electrolytic), 3) parts subjected to heat in order to solder in other pins (tin plated steel), 4) pins bent to simulate "gull-wing" for surface mount applications.
Plating cracks and/or pins break at bending stage.
Does this sound like hydrogen embrittlement issues? If so, any suggestions as how to alleviate the issues?
Any suggestions are appreciated.
Thanks,
B.J. Hughes- Salisbury, Maryland
A. You should check the ductility of your nickel solution. A good bright nickel solution should have a ductility of 0.1-0.3 depending on the age of the solution and the type of brighteners. What type of nickel solution are you using? Additive free nickel solutions like sulfamate should have a ductility of 0.5. Ductility is inversely proportional to brightness.
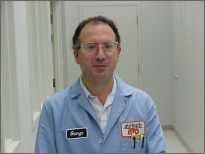
George Shahin
Atotech - Rock Hill, South Carolina
A. Mr. Hughes: I agree with George's opinion. Your problem sounds more like a problem in your plate causing a physical phenomena called "notch fracture", meaning that the plate is cracking first, then the crack is forming a weak leading edge which is propagating to the inner substrate. I don't have any information that brass could be embrittled by H+. In this respect I would also like to hear from others.
Guillermo MarrufoMonterrey, NL, Mexico
Q. Has anybody any information on cases of hydrogen embrittlement of brass in connection with nickel plating? Or any other type of surface treatment.
Kjell Pettersson- Stockholm, Sweden
2002
A. Hi Kjell,
We electroless nickel plate (.0002"-4" thick) 360 brass sleeves all the time and one of our adhesion tests require us to crush with pliers approx. 50 sleeves per lot plated. When unplated parts are subjected to this test the brass sleeve flattens with minor cracks, however after plating the samples always brake into four pieces. At this point I would assume that the sleeves are subject to some hydrogen embrittlement. The sleeve is .350" O.D. x .275" long with a wall thickness of .050" so I don't think the plating thickness is a factor.
I hope I have been of some help and perhaps others with more experience can add more insight into this phenomena.
Paul Szymanowski- Erie, Pennsylvania
2002
A. My guess is the preplate processing that is causing the problem.
James Watts- Navarre, Florida
2002
2002
A. Hi Paul,
Conventional opinion is that hydrogen embrittlement of such material doesn't happen. Your experience is a strong challenge to that, and certainly warrants following up. As the most basic preliminary question, do you expose the sleeves to heat at any time before or after plating? If so, what happens if you expose unplated sleeves to the same heat cycle then crush them?
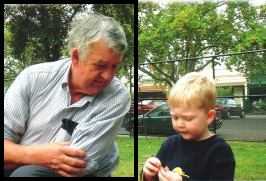
Bill Reynolds [deceased]
consultant metallurgist - Ballarat, Victoria, Australia
We sadly relate the news that Bill passed away on Jan. 29, 2010.
2002
A. Hi James & Bill,
Sorry for the delay but I wanted to run some casual tests to further confirm my assumption about HE in 360 brass.
1) James you are right about the preplate cycle, it does induce approx. 20-25% embrittlement. The plating bath contributes the rest. (Numbers are subjective as I am using pliers.)
2) Bill, the highest temp. the parts are exposed to is 190 °F in the plating bath. Cleaner, about 160-170 °F. We ran a test, enclosing a sample lot in a heat sealed polypro bag, clamped to the barrel to expose the parts to the thermal cycle with no exposure to chemicals. No effect was noticed on the parts.
3)Baked the parts removed from barrel after precleaning and prior to plating at 375 °F 3.25 hrs. Parts returned to preprocess ductility. (Our normal bake is 250 °F) I have not had time to relief bake plated parts but will do so today.
If either of you would like some samples of each test (Bare, Precleaned-unplated, precleaned & baked, plated, plated and baked) please feel free to contact me.
I was always led to believe HE was associated with high carbon until I ran into this phenomenon. I hope someone with better instrumentation can pick up the ball from here. I will help in any manner I can, to the best of my ability.
Kjell, I hope this information is of some help.
Paul Szymanowski- Erie, Pennsylvania
Q. I'm encountering a similar problem with tin plated brass parts. My question is how did the plated parts come out after baking.
Paul Haas- Centreville, Michigan, USA
2002
A. Paul,
Parts did not return to normal after baking @ 375 °F 3-1/2 hrs. After extensive research it was determined that the breaking was due to the E/N plating, and not HE.
Paul Szymanowski- Erie, Pennsylvania
2002
March 2016
Hi. I'm no metallurgist, but as a layman I've heard that, exactly opposite to the way steel hardens if quenched but stays soft if very slowly cooled, copper & brass harden if slowly cooled but stay annealed if quenched. Hopefully a metallurgist can flesh out my understanding or correct my misunderstanding :-)
Regards,
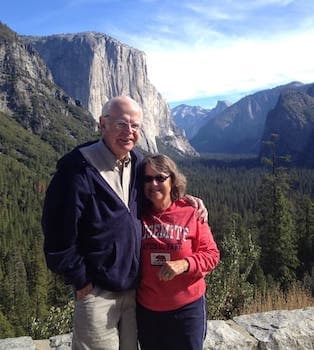
Ted Mooney, P.E. RET
Striving to live Aloha
(Ted can offer longterm or instant help)
finishing.com - Pine Beach, New Jersey
Post Baking Nickel Plated Brass Parts to "repair" parts that are cracking/flaking
Q. We have been having adhesion problems on parts we make from 360 Brass and then have them Electroplated(watts) to QQ-N-290. The spec calls for Min .0002 copper and min .0004 Nickel and they specify "Bright". The end customer "Crimps" the parts onto a hose, and has been experiencing flaking/peeling of the plating.
We have worked hard with our plater to determine the root cause of the issue which has a lot of variable's but the plating thickness, as well as the "Bright" specification" seem to be big contributors to the issue.
My customer has been repairing the parts (if samples are cracking) by putting them in an Inert Atmosphere Oven (with Argon gas and positive pressure) and baking at 600 degrees for 2 hours. My customer does not know how they developed this procedure, or exactly what is happening that fixes the problem.
Can anyone offer any opinion on what is happening. I think this would make the Nickel Plating HARDER, and more brittle; my plater suspects it is actually stress relieving the Nickel plate.
Thanks for any opinion on the "repair", as well as thoughts on why the plating is peeling in the first place.
Machine Shop - Addison, Illinois
March 16, 2016
March 17, 2016
A. Good day John.
From what I am reading, it is clearly an adhesion issue. What is the composition of the brass? Does it contain lead,and if so, an acid dip with fluoboric will deal with the lead, as it is insoluble. Is the brass electrocleaned anodically or cathodically? A loaded cleaner operated cathodically can deposit impurities to the surface of the brass. An electrocleaner operated anodically can produce oxides on the surface which can cause adhesion issues.
I use an acid dip @ 10% sulfuric with bifluoride to remove any "smut/oxides" produced either anodically/cathodically electrocleaned.
Regarding the nickel plating, excess brighteners can cause adhesion issues, as high TOC values. Has there been a analysis done on Total Organic Carbon? Has there been any Hull Cell
⇦ huh?
testing to determine LCD coverage? What are the sulphate and chloride concentrations? I think baking parts will show adhesion issues.
I bake SS parts (head light bulb shields) @ 650 °F for 2 hrs that are plated semi bright nickel, bright nickel, chrome (micro cracked) to determine adhesion failures,and rarely discover any.
Hope this helps.
Regards,
Aerotek Mfg. Ltd. - Whitby, Ontario, Canada
Q, A, or Comment on THIS thread -or- Start a NEW Thread