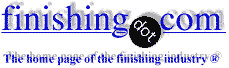
-----
Seeking alternative to zinc plating
Q. I am interested in finding alternatives to zinc plating/blue chromating my parts. The application is retaining clips, .020" thick 1050 steel, hardened to approx. Rc 42.
The clips need to withstand damp locations without corroding. I am currently experiencing sporadic incidences of hydrogen embrittlement failures, and am seeking an alternative coating that is cost effective and more repeatable.
Thanks!
Scott Duprelighting - Fall River, Massachusetts
2002
A. If the parts are properly baked in timely fashion you should have no hydrogen embrittlement problems at all. Critical high-strength parts are routinely plated every day. And it must also be noted that no corrosion resisting treatment is as simple, reliable, and inexpensive as zinc plating.
But, yes, there are many alternatives: black oxide and oil (not as corrosion resistant), mechanical plating, electroless nickel plating, zinc-rich dip-spin processes, etc.
To summarize, move to another coating if the properties of the other coating improve the product if you wish, but don't do it because your parts fail from hydrogen embrittlement because this is a problem of execution, not a design problem.
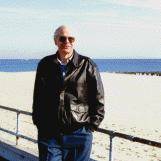
Ted Mooney, P.E.
Striving to live Aloha
(Ted can offer longterm or instant help)
finishing.com - Pine Beach, New Jersey
2002
A. Do not use acid in the prep cycle, instead remove oxides and scale with 2#/gal Alkaline Deruster (available from any cleaning house supplier) at about 185 °F. This will solve the embrittlement problem.
Blue Bright Chromate over zinc should not reintroduce embrittlement, however, you can get the same corrosion resistance without a chromate by switching from zinc to zinc-nickel or zinc-cobalt at slightly higher cost. But when you figure in the cost of chrome disposal the alloy zincs just might be lower net cost.
A top coat of about 1% or 2% Soluble Oil, dry to the touch, should even further increase the corrosion protection.
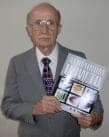
Robert H Probert
Robert H Probert Technical Services

Garner, North Carolina
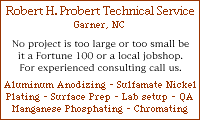
2002
A. Despite what Mr. Probert is saying, alloy zincs typically are treated with a chromate conversion coating to increase corrosion protection and to prevent oxidation of the deposit. Properly treated zinc plated components should not have problems with embrittlement. There is no generic material call "Alkaline DeRuster". A variety of alkaline derusting compounds are available from a myriad of suppliers each one of which has specific application data that should be followed. Acid pickling or activation is a necessary step if the parts are being plated in an acidic zinc solution. It is excessive pickling without the use of a pickle addition agent that can cause further embrittlement.
Gene Packmanprocess supplier - Great Neck, New York
2002
Thank you for your input. I am going to keep the zinc plate w/chromate, and specify a 375 °F bake for a minimum of four hours immediately after plating. We will see how that goes! Thanks again for the help.
lighting - Fall River, Massachusetts
2002
A. Scott,
You left out an equally important spec, It must be in the bake oven as soon as possible, and not exceed one hour after coming out of the plating tank. Many books will use 4 hours, but that is too long for spring steel.
James Watts- Navarre, Florida
2002
Q. Mr. Watts,
Thank you for your comments....you are saying that the bake cycle should not exceed 1 hour? Or are you saying that no more than 1 hour should elapse between plating/baking?
If four hours is too long, what type of cycle would you recommend? I have read many varying opinions, most say 4 hours min., some say 24 hours wouldn't hurt....the idea being, I suppose, that 375 °F will not affect the physical properties of the steel.
Scott Duprelighting - Fall River, Massachusetts
2002
A. Hi Scott. James is saying that the parts should get to the oven within an hour. That is because it is not enough to just get the hydrogen out, it has to be gotten out before it does damage.
Regards,
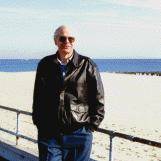
Ted Mooney, P.E.
Striving to live Aloha
(Ted can offer longterm or instant help)
finishing.com - Pine Beach, New Jersey
A. The pickling stage and the plating stages induce Hydrogen embrittlement. Using Alkaline derusters will eliminate the embrittlement at the pretreat cycle stage.
Bake at 180 to 220 °C for 1 to 4 hours, depending on actuals, to remove the embrittlement that occurs at plating stage.
Then passivate with the blue chromate after allowing the parts to cool at room temperature to ambient ... DO NOT QUENCH in water or oil.
This will need tuning to decide exactly how much time is actually needed at bake temperature to actually remove the Hydrogen embrittlement.
Regards,
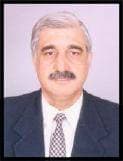
Asif Nurie [deceased]
- New Delhi, India
With deep regret we sadly advise that Asif passed away on Jan 24, 2016
2002
A. For spring steel, We used a criteria of immediately after rinse and blow dry. We used 15 minutes as an "explain why you exceeded". Bake time is: the longer the better. 4 hours would be a normal minimum for bake. As stated above in several replies, the acid pickle/etch is the worst offender! Hold the etch time to an absolute minimum and you should not have any problem. Notch bar testing will prove it.
James Watts- Navarre, Florida
2002
Q. I am looking for finishing processes for mild steel that provide a similar look to zinc electroplating, but have a more uniform overall finish. I've noticed discoloration around features like welds, holes and edges, as well as white residue on flat surfaces. I'm looking for something that's true to the material (rather than a coating or paint), and that can serve as both a corrosion-resistant and cosmetic finish. Thanks!
Marie Lanes- Austin, Texas
December 16, 2014
A. Hi Marie. It is true that zinc plating is usually not considered a decorative finish, but there are exceptions. Bicycle rims have been zinc plated and clear coated as an alternative to nickel plating, for example.
Nickel plating is more decorative and may meet your needs, and is corrosion resistant, but "corrosion resistant" can be a rather loaded term :-)
Zinc plating provides sacrificial galvanic protection to steel, whereas nickel plating provides only barrier layer protection, i.e., it only works if the plating is perfect (thick enough, and free of porosity and pinholes). No other plating is as inexpensive as zinc plating. Good luck.
Regards,
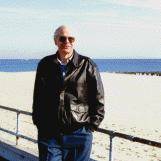
Ted Mooney, P.E.
Striving to live Aloha
(Ted can offer longterm or instant help)
finishing.com - Pine Beach, New Jersey
December 2014
Q, A, or Comment on THIS thread -or- Start a NEW Thread