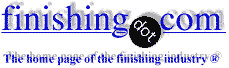
-----
Hot-Dip Tin Plate Composition
Hi!
I'm doing an experiment on electrolytic method for determining tin coating thickness. With this, I'd like to know any differences between electrolytic tin plate and hot-dip tin plate with regards to chemical composition(e.g.which method of plating causes presence of more alloy of tin and steel substrate). This would help me interpret the graph of potential vs. time for my experiment.
Aniceto V. Idjao Jr..- Manila, Philippines
2002
If you galvanostatically strip the tin in a 2N sodium hydroxide ⇦ on Amazon [affil link] with an anodic current density of about 5-6mA/cm2 you will see all the relevant layers of the tinplate. The solution should be at 70C or higher. Initially a very thin layer of tin oxide will be dissolved off at a potential of about -1200mV (vs Hg/HgO reference electrode). This will be followed by another plateau at about -1V and this is the tin being removed. As you continue, you will see another plateau at about -800mV and this is the intermetallic alloy FeSn2. Once this has gone, the potential will rise by another volt or so.
The tin and tin oxide both dissolve at about 98+% efficiency, so the thicknesses can be easily calculated. The intermetallic layer does not dissolve very efficiently and if you are very careful, you can follow its mechanism electrochemically. Initially the alloy is disrupted by dissolution of the tin but this is quickly followed by oxidation of the iron from Fe(II) to Fe(III); this breaks open the alloy structure and allows total dissolution. Iron and tin form a whole range of intermetallics, FeSn2, FeSn, Fe2Sn3 and Fe3Sn2, but only FeSn2 is found in conventional tinplate. The others can be formed by heat treating the tinplate until all the tin has diffused into the steel substrate, but they are unstable and break down to Sn and (ultimately) FeSn2 again. They can be detected by the process above, but they all have different dissolution potentials.
As far as differences in electrolytic and hot dip tinplate are concerned, hot dip has much more tin on the surface, but it also has a lot more intermetallic because the plate is made by dipping the steel into molten tin. This causes greater diffusion of the tin into the steel and it follows Fick's 3rd Law of diffusion. There is also some evidence to suggest it can entrap trace elements from the cleaning process. Electrolytic tinplate, on the other hand is made by electrodeposition of tin and then flash melting and quenching in a suitable oil. As a rule of thumb, electrolytic tinplate has about 90% tin, 10% alloy and about 0.2% tin oxide. Hot dipped tinplate will have a higher amount of alloy and this can be as much as 20%. All of these values will, however, vary with the thickness of tin being applied.
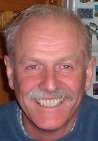
Trevor Crichton
R&D practical scientist
Chesham, Bucks, UK
2002
2005
2002
This is a follow-up question on the query I posted before. I have performed a galvanostatic stripping of tin coating on steel substrate using HCl as my electrolyte and applying a constant current density of about 63mA/cm2. The potential vs. time plot shows a constant potential of about -140mV for about 1 minute, then a constant slope increase in potential which lasted for another 13 mins. This was followed by a drastic increase in potential from -180mV to -280mV, then a gradual decrease in potential.
What could possibly be the chemical reactions in these various stages of the galvanostatic stripping process? Could you give me possible oxidation reaction of tin and what could it possibly react with. Is it not simple dissolutiuon of tin metal to Sn2+ only?
I have assumed that the constant potential(-140mV) at the initial stage of the process corresponds to the tin dissolution and have disregarded presence of any tin oxide because I have cleaned my sample surface with acetone ⇦ on eBay or Amazon [affil link] Warning! Flammable! beforehand. I used this data(time=1min) to calculate for the tin coating thickness(which is the objective of my experiment) in which I arrived at 4.9um thickness. Am I on the right track?
Aniceto V. Idjao Jr..- Manila, Philippines
Hi!
I'm doing an experiment on electrolytic method for determining tin coating thickness. With this, I'd like to know any differences between electrolytic tin plate and hot-dip tin plate with regards to chemical composition (e.g.which method of plating causes presence of more alloy of tin and steel substrate). This would help me interpret the graph of potential vs. time for my experiment.
Ekkawat KaewluanCTW - Auytthaya, Thailand
2004
Q. Hi sir,
My inquiry is --
How can I differentiate between electroplated tin and hot dipped tin (on steel) in laboratory.
Many advanced thanks,
Dalal
- Egypt
February 2, 2012
Hi, Dalal. As you see, we appended your question to a thread that may wholly or partially answer it for you. If not, can you please explain your situation rather than casting the question in the abstract? A problem with abstract questions is that they usually introduce a dozen if, ands & buts before anyone can start trying to answer :-)
For example, if the article was electroplated and reflowed, do you want it to register as electroplated or as hot dipped? Are you concerned about tin whiskers, remnants of brighteners that could degrade, authenticity of an antique? Sometimes it's easier to answer the real question than an abstract one that has been erected around it. Thanks!
Regards,
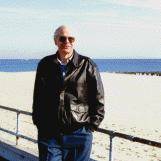
Ted Mooney, P.E.
Striving to live Aloha
(Ted can offer longterm or instant help)
finishing.com - Pine Beach, New Jersey
February 2, 2012
Q, A, or Comment on THIS thread -or- Start a NEW Thread