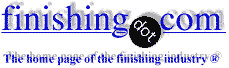
-----
Pickling bath pollutants
2002
Dear Sir,
I work for the Valle d'Aosta Environmental Protection Agency (Valle d'Aosta is a region in north-west of Italy). I'm studying the problem of the air emissions of a stainless steel pickling plant.
In this plant, steel treatments are made using three kinds of pickling baths:
- Bath with a solution of HNO3 (15-20% by weight) at ambient temperature;
- Bath with a solution of H2SO4 (10% by weight) at 50 °C;
- Bath with a solution of H2SO4+HF+H2O2 at 50 °C (the composition of the bath in this case is not known).
I'm looking for an answer to some questions:
1) Which kind of reactions occur between HNO3 and metal oxides of the scale?
2) Which kind of reactions occur between H2SO4 and metal oxides of the scale?
3) About the bath with the HNO3 solution: the most important pollutants emitted are NOx; should I consider also HNO3 vapors as pollutants emitted from the bath?
4) About the bath with the H2SO4 solution: I know that H2SO4 vapors can be emitted because of the rise of gas bubbles (for example H2) developed from the reactions between the scale and H2SO4, causing the presence of acid mists that are harmful for workers. H2SO4 vapors sucked from the bath can be a relevant pollutant emitted in the atmosphere?
5) From a measurement of the gas emitted from the plant (including the emissions of all the three kinds of bath) we founded a value of 55 ppm of SO2. From which bath can develop SO2? What reaction causes the formation of SO2 from a pickling bath?
Can you suggest me a book, or a technical publication or any other source of technical documentation concerning chemical reactions that occur in a steel pickling bath, and the air pollutants that can be emitted from a steel pickling bath?
Thank you very much for your help.
Devis Panont- Italy
2002
Hi Devis !
How nice it is to see a query re air pollution ... this rarely comes up!
You sure gave some pretty pertinent information. Thanks.
In short, I don't consider the sulfuric to be a problem at all it's the nitric one has to worry about. However, you are just handling stainless and NOT copper products where I believe it is MUCH more of a problem.
Nitrics! They can break down into varying compounds, some of which are easily eliminatable, some not so like NO2. An Italian Company designed a gold refining plant in B.C. back in the early 80's, AJM VIERI (I believe that is the correct spelling) which, unfortunately, never went into service. Their design of the NOX (from the superheated nitric retorts) was superb. A row of 'empty' l0 foot or so high 12" diameter PVC pipes with mini inlet bleeders. Then onto a typical NaOH sprayed mass transfer scrubber. Their idea being that one needed a long retention time. The 'bleeders' just bled in a little air = oxygen for the NOX fumes to convert themselves back into scrubbable compounds such as HN02.
In your case I do not believe that you will generating nearly as much NOX ... and in one case (Toronto, l970) a plater had a brown "NO2" fume being emitted which, after passing through a good l2 micron horizontal airflow mist eliminator, disappeared much to his and MY pleasure! My conclusion in his case is that the brown fume was WET!
Having supplied the 'ordinary' l2 micron eliminators to the Assay field (nitric, sulfuric, aqua regia, HF, HCl and, my favourite, Perchloric) even recently, I am sure that they will work for the sulfuric side.
I cannot ... and never could ... guarantee any nitric capture due to the variances of l. temperature 2. concentration 3. chemical reaction and, importantly (for nitric!) 4. the cooling down of the exhaust gas AND the mixing of it with 'other' acid fumes ... ie. air dilution and excess oxygen in the airstream.
For the sulfuric I'd only use, based on past experience, a well designed l2 micron eliminator. One could use a coalescing eliminator design and achieve 3 micron capture (INCO R & D in Port Colborne, Ontario, l974-ish) had a HOT sulfuric emission of 0.2 to 0.8 microns. These emitted from a Joy prescrubber. Capture efficiency was 86% and that solved the problem of sulfuric clouds during inversions. This unit was, however, sprayed with NaOH. There are extremely few Companies who have the knowledge and equipment to measure low microns. They did.
I hope that this data might be of some help to you.
... ah, I forgot... the eliminators were made in most cases of PVC, the low micron coalescing units (I called them LMITS inertial scrubbers) were also of PVC and had a PP mesh coalescing stage just before the final eliminator bank.
Cheers !
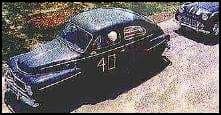
Freeman Newton [deceased]
(It is our sad duty to advise that Freeman passed away
April 21, 2012. R.I.P. old friend).
Q, A, or Comment on THIS thread -or- Start a NEW Thread