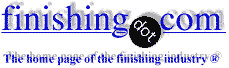
-----
Wet Abrasive Blasting Process vs. Dry
Q. I have been asked to provide advice on the advantages or disadvantages of wet blasting versus dry blasting using glass beads in machining. Has a case study been published or is information available that offers this information? Recognizing that resource recovery or pollution prevention must be the most important consideration. What would be your recommendation?
Samira NawarCanada
1996
A. THERE ARE MANY ADVANTAGES WET BLASTING HAS OVER DRY BLASTING SUCH AS NO DUST,GREASY/OILY PARTS CAN BE BLASTED WITHOUT PRIOR CLEANING,BLASTING WITHOUT SURFACE FINISH DAMAGE.
Richard GillottA. Wet Blasting Method of Surface Preparation is recommended in the areas of Fire Hazard (Eg.Live Facility- Production Area).
K.VenkatapathyOil & Gas Projects - Pondicherry, India
2005
A. We build large work boats. Because of environmental issues we always wet blast. An average of 500 Sq/Mts per vessel. I's a bit slower but much better finish … "Wet is best" … oh and size matters … use a big pot 250psi @ 1200 CFM
Walter Wright- Pembroke (Wales)
October 22, 2008
Multiple threads merged: please forgive chronology errors and repetition 🙂
Q. What are both the process and economic parameters behind the decision to do wet abrasive blasting over pneumatic blasting or even using a chemical cleaner? I currently outsource all of our "hard" cleaning requirements usually for pneumatic sand blasting. I am trying to cost justify buying a cleaning system (and leaning towards a wet blasting system based more on option that economics) but haven't been able to justify any one type of cleaning over another. Any suggestions?
Eric Lynch- Crawfordsville, Indiana
1998
A. In reply to the letter concerning wet blasting - the economics of this process are usually not viable due to the slowness of production --- what is in fact a more viable option in most cases is to build a rather large blast room with extractor fans linked to a wet down scrubber unit - the actual blasting inside the booth remains dry increasing production and complying with regulations on dust emissions.
Steven Collett- New Zealand
A. Plain wet blasting is very slow. If you are only cleaning, you can add TSP [trisodium phosphate ⇦ on eBay or Amazon [affil link] ] and a little bicarb of soda and get a very effective cleaner. for tougher soils, you can throw in a handful of very fine glass beads. For even tougher soils, you can throw in a handful of spent dry abrasive.
This is a neat system. Properly used, you can strip the chromate off of cad or zinc and not remove a measurable amount of the metal. With abrasives added, you can strip the zinc or cad while removing virtually none of the parent hardened steel and have a beautifully clean and active part.
It cannot be used for removing heat scale and such uses.
James Watts- Navarre, Florida
A. I don't pretend to know anything about blasting, we used to use a "liquid hone" using glass beads which was very nice for polishing connector shells prior to electroplating. It was labor intensive, but for valuable parts, it does a nice job. We even used to hone the shells after the glass seal process, we used to make a rubber cover for the glass seal so we did not abrade it with the beads.
The only thing I might add is on the cadmium metal blasting. In a dry blasting situation, the cadmium will get into the air and it caused elevated cadmium levels in the air around one such operation. You might be okay as long as the blasting beads stay wet, but even in our small glove-box size honer, we had dry sand all over the floor, so airborne cadmium might be a problem.


Tom Pullizzi
Falls Township, Pennsylvania
A. In answer to your questions on wet blasting, etc. Sodium Bicarbonate Blast systems work very well for a variety of purposes using both wet and dry dust free methods.
Steve Schrand- Washington
1999
A. Wet Blasting is an often misunderstood phrase.
My Grandfather (Norman Ashworth)was the holder of many patents for this wet blasting process after the war years. At that time progress was being made on both sides of the Atlantic to develop the process using a slurry of water or water based liquid and solid material.
The solid material was normally a fine blasting media - sand, novaculite, carborundum. The main focus of activity was to develop a precise surface finishing process with the ability to use extremely fine medias - The process was used extensively in the manufacture of Jet engine components which were some of the most "high tech" parts at that time. It is this type of fine finishing carried out within cabinets that characterizes what some people now term "wet blasting" -- other trade names of the past and present include Vapor-blasting , Vapour-blasting, Vapormatt process, liquid honing.
The modern process wet blasting process is far more sophisticated than the delicate process described above. Common features include: the ability to use extremely fine, or coarse, medias with densities ranging from plastic to steel; the ability to use hot water and soap to allow simultaneous degreasing and blasting; Elimination of Dust - so silicacious materials can be used without worry, hazardous material or waste can be removed without danger - e.g. removal of asbestos, radioactive, or other poisonous products from components and structures leading to effective decontamination.
The process is available in all conventional formats including hand cabinets, walk in booths, automated production machinery and total loss portable blasting units.
Process speeds can be as fast as conventional dry sand blasting when using the equivalent size and type of media. However the presence of water between the media and the substrate being processed creates a lubricating cushion that can protect both the media and the surface from excess damage. This has the dual advantage of lowering media breakdown rates and preventing impregnation of foreign materials into the surface. Hence surfaces after wet blasting are extremely clean, there is no embedded secondary contamination from the media or from previous blasting processes, and there is no static cling of dust to the blasted surface. Subsequent coating or bonding operations are always better after wet blasting than dry blasting because of the cleanliness levels achieved. The lack of surface recontamination also allows the use of single equipment for multiple blasting operations - e.g. stainless steel and carbon (mild) steel items can be processed in the same equipment with the same media without problems.
Robin Ashworth- England
2000
Q, A, or Comment on THIS thread -or- Start a NEW Thread