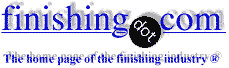
-----
Chromates in paint process
Chromates will be forbidden in the European automotive industry in
2003. What is the best way to substitute the chromatizing in the pre-treatment process and to still achieve suitable corrosion resistances, salt spray 480h?
For some reasons, the use of zinc phosphates in the process is impossible, so we have to stick to iron phosphatizing. Somebody told me to use chromic acid instead of chromate acid, but this sounds silly to me.
- Germany
2002
2002
My understanding is that there is no such thing as chromate acid. I believe that both chromic acid and chromates are identified as
(CrO3). Chromate is considered chromate tri-oxide or a Hexavalent.
All chromate conversion coatings use chromic acid in the form of its soluble salts. When aluminum and aluminum alloys are immersed in a controlled chromic acid bath with additives, a chemical conversion reaction takes place at the surface of the metal. During the process, a thin, gel-like film is produced on the aluminum surface.
This reaction produces a complex, non-crystalline, non-porous coating consisting of a thin aluminum oxide film with entrapped chromates and dichromates. The corrosion resistant properties of the coating are primarily due to the chromates, specifically the hexavalent chromium.
Chromate coating, Alodine, Chem film all refer to the thin film formed chemically on metals, which contain tiny amounts of chrome compounds that act as corrosion inhibitors. In addition to having good corrosion resistance, they are very good bases for paints or other organic coatings, and for abrasive bonding.
Various chemical activators are used to enhance the formation of the coating. Depending upon the desired performance characteristics of the chromate film, the chromating bath is often modified by changing these activators.
Chromate is an excellent treatment method for paint or adhesives since it greatly enhances the product's ability to form a bond with the aluminum. It is frequently used on electrical and electronic equipment because it provides increased corrosion resistance while remaining electrically conductive and probably the principal reason I see it used in industry today.
![]() Bob Utech Benson, Minnesota |
![]() Ed. note: Bob is the author of: "High Performance powder Coating" on eBay or AbeBooks or Amazon [affil link] |
First of three simultaneous responses --
Hi,
It is not clear whether you need to treat aluminium or whether you are referring to chromate final rinses on steel, as 500 hrs salt spray would be very low for aluminium.
1. Non chromate processes are readily available in Germany for aluminium which meet GSB/Qualicoat standards
2. Final rinse additives are also available for use with iron phosphates which will give easily the salt spray resistance required in your message.
- Croydon, UK
2002
Second of three simultaneous responses --
Seems to me, that I have not expressed myself clear enough. It is no aluminium pretreatment. It is a pretreatment, where steel is the substrate, and we are currently running the process with iron-phosphatizing combined with a chromate acid passivation as a final rinse. Since we will have to change to a non-chromate pretreatment by the middle of next year (due to legislation), I need to know what is possible to use instead. Silanes are ridiculously expensive and all the other stuff does not even come close to the corrosion resistances met with the chromate-containing solution.
Ines Kistenbrügger- Germany
2002
Third of three simultaneous responses --
We here in Europe are faced with a legislation that makes the use of CR6 almost impossible. It is considered to be hazardous for the health (causing cancer). In practice this means that when using pretreatment lines where you chromate on alu or use a Cr containing passivation one has to take a lot of (safety and health)precautions, thus making the process expensive. Secondly, in the near future any car used in Europe may contain in total a maximum of 2 gram of Cr6. Therefore all OEM's are obliged to change their processes because car-manufacturers don't allow them anymore that their products contain any Cr. This is the real reason behind the question, and that is why all the alternative processes are coming on the European market actually. When we're at the subject, I as an European am surprised and curious that I see almost no awareness of these facts in the responses of the American people visiting this site. This goes not only for the Cr subject but also for e.g. TGIC-powders. TGIC is since some years almost completely banned here and meanwhile we have the alternatives. But I still see a lot of question at this site from
-again American -people who still use TGIC powders without any hesitation.
Anybody there who could satisfy my curiosity?
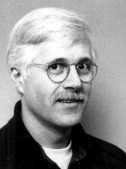
Remmelt Bosklopper
- Enschede, The Netherlands
2002
Americans are well aware of the European restrictions on hexavalent chromate on automobiles. But the replacement processes are more expensive and more complex (which means inherently less reliable despite promising tests). So people who are not in the automotive business and are not compelled to eliminate chromates have no real incentive to change at this point.
Despite the vaunted Japanese focus on quality, their automobile manufacturers somehow managed to build cars that performed miserably corrosion-wise even decades after American and European manufacturers had solved such problems permanently. So, while it will be good to be rid of chromates and TGIC, a little diversity and hesitation to move away from proven processes is not all bad.
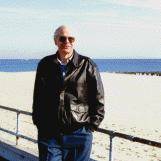
Ted Mooney, P.E.
Striving to live Aloha
(Ted can offer longterm or instant help)
finishing.com - Pine Beach, New Jersey
2002
Q, A, or Comment on THIS thread -or- Start a NEW Thread