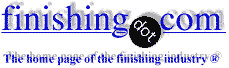
-----
Aluminum pretreatment for powder coating
Q. Hello. What can I use as Substitute for chromium passivation of aluminium before powder coating ?
We have tried some substitutes, but the coating did not 'stick' properly to the surface.
I was thinking maybe to use electrolytical method.
Any ideas ?
Regards,
- Bergen, Norway
March 2, 2021
A. Hello Geir. The MIL-DTL-5541
[⇦ this spec on DLA] approved trivalent chromates should work. But are you sure you are doing proper pretreatment before application? Please name the substitutes which you tried but didn't work; people may not want to risk suggesting something only to be told "we already tried that, and it didn't work -- like I just said" :-)
What is the alloy and what kind of components? Personally, I have never heard of electrolytic chromates or substitutes being used on aluminum, and I don't think they could work without a zincate treatment first.
Luck & Regards,
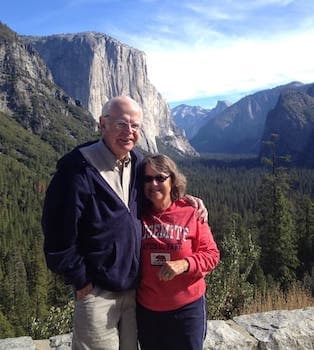
Ted Mooney, P.E. RET
Striving to live Aloha
(Ted can offer longterm or instant help)
finishing.com - Pine Beach, New Jersey
March 2021
⇩ Related postings, oldest first ⇩
Q. I'm doing research on aluminum pretreatments for parts that receive powder coating. My company usually specifies chromate conversion for aluminum. It is used on unfinished aluminum, as well as a substrate for liquid primer / paint. It is sometimes used as a substrate for powder coated parts (aluminum). I find literature that states the corrosion resistance benefits of chromate conversion coatings degrade above relatively low temperatures (150 °F?). The bake temperature of the powder coating we use is 375 °F. I am concerned that the conversion coating on parts going through the bake process is rendered useless. If this is the case, I want to eliminate the process from the manufacturing flow, as it is not adding value. Would Iron Phosphate be a better process for this application? Are there alternatives you can suggest?
Peter C. Maher- Skokie, Illinois
2002
Treatment &
Finishing of
Aluminium and
Its Alloys"
by Wernick, Pinner
& Sheasby
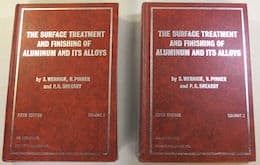
on eBay or Amazon
or AbeBooks
(affil link)
A. Hi Peter,
The temperature sensitivity of chromated aluminum is well known because of changes in the structure of the conversion coating. Although I think is is difficult to quantify how strongly temperature affects the corrosion resistance of the coating, chromating is probably your best bet. Iron phosphating is an inferior pretreatment for aluminum. If you have corrosion specs that need to be met, I imagine that a somewhat degraded chromate conversion coating will beat the best iron phosphate coating every time.
- Naperville, Illinois
2002
A. Peter,
Chromate, like other conversion layers, is only restricted temperature stable at the first initial drying (e.g. the drying done directly after the chromating process). Once dried completely the temp. resistance is much higher. Although I don't now the exact figures, chromate layers withstand the temperatures for curing powdercoating without any problem.
Nevertheless I could imagine you generally want to get rid of chromates e.g. chromium, due to the health hazards. Depending of the circumstances your parts will be in, be aware that actually other, less hazardous processes are available.
Regards,
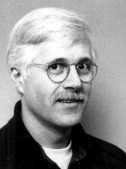
Remmelt Bosklopper
- Enschede, The Netherlands
2002
A. Aluminum Chromate under heat cured powder paint is a proven and acceptable pretreatment, HOWEVER, the chromate gel coating must be thin. The moisture left in a heavy coating will "out-gas" (sort of explode) through the powder paint and leave corrosion opportunities. Again, put the chromate on very lightly for bonding powder paint.
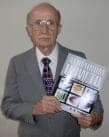
Robert H Probert
Robert H Probert Technical Services

Garner, North Carolina
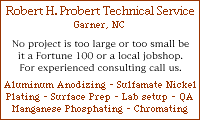
2002
Thanks to all who answered my question. I want to share information on an experiment I did using chromated aluminum test panels, which were then powder coated. 2024 test panels were processed through our standard 10 stage chromate line (Ultrasonic alkaline clean, running rinse, 2 ultrasonic DI water rinse, de-ox, rinse, chromate, rinse, rinse, DI final rinse). The panels were allowed to dry for at least 24 hours. They were then powder coated (1/2 of the plates were masked prior to coating) and cured at 375 °F for 15 minutes. The panels were unmasked, and put throughASTM B117 168 hour salt fog test. The powder-free areas of the plates corroded badly, almost as badly as the unprocessed panels placed into the salt fog chamber. They did not come close to passing the requirements of B117. The powder coated surface held up perfectly. So, the cure temp of the powder coating renders the chromate coating useless. This must be kept in mind if uncoated chromated surfaces will be used in a corrosive environment.
Thanks again for the input.
- Skokie, Illinois
2002
A. Hi Pete!
When any aluminum is cleaned using alkaline chemicals, the bath will etch the substrate. Etching gives the topcoat a surface in which to adhere to. This is particularly important when looking for salt spray performance. As you are aware, aluminum does not accept a phosphate coating. The etch really improves performance. Also, aluminum is not generally put into a salt fog chamber to be tested because properly pretreated panels will take forever to corrode (under the topcoat). You said the powder coated areas did not corrode, yet the powder free areas corroded. It would seem that they would corrode without a topcoat application. The quality of the aluminum will also make a difference upon your test outcome. I would retest using only the powder topcoat area and test panels using ones that were chromated against those that were simply alkaline etched. That will be the true test. As far as bare aluminum, I am not sure. And remember! Even if the bare aluminum corrodes in the salt fog chamber, does not necessarily mean it will corrode in the real day scenario.
![]() Bob Utech Benson, Minnesota |
![]() Ed. note: Bob is the author of: "High Performance powder Coating" on eBay or AbeBooks or Amazon [affil link] |
A. You repeated and reconfirmed what the specification writers had in mind when they wrote into the Mil specs not to dry bare chromate over 140 °F. Left bare it is common knowledge that it is destroyed (dehydrated) by heat, however, under any kind of paint it will hold up.
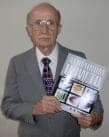
Robert H Probert
Robert H Probert Technical Services

Garner, North Carolina
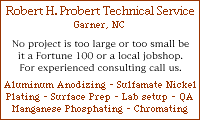
2002
A. Pete,
I performed a test very similar to yours, but with slightly different results. I masked some chromate-converted panels using standard high-temp tape [green powder coating tape]
(affil link) and applied epoxy powder coat. Removed masking carefully from some panels prior to cure. Cured 15 min @ 375 °F; finished de-masking. Subjected panels to salt spray. The panels unmasked prior to baking corroded as though they had no chromate conversion coating on them. Those which were baked with masking in place, wherever the masking had been firmly adhered the panel was fairly resistant to corrosion, but not as good as required by MIL-C-5541. But ... at gaps in the masking the corrosion was heavy.
The deteriorating effects of heat on chromate conversion coatings on aluminum is relatively easy to demonstrate. Bake chromated panels at different elevated temperatures (150 °F, 200, 250, 300, etc) for a standard time, say 15 minutes, or an hour. Then salt spray them. You'll see the progressive deterioration. The limit for continuous exposure is as stated in the spec.
- Akron, Ohio
2002
Q. Peter, et al, is it possible that I get a copy of a doc that says "chem-film degrades as temperature increases"? Our vendor is drying the pre-treated aluminum to 400 °F oven and it always is failing the salt mist test. He said he just wants to make sure all dries up and the cause of the failure is dents or scratches (which for the fact is correct), but if this temp really degrades the chem film, then I must recommend he stops his drying process with proper docs to back me up. Thanks, looking forward to your help.
Ronald Dioceratelecommunications - Philippines
2004
Multiple threads merged: please forgive chronology errors and repetition 🙂
Q. I am familiar with the process of preparing diecast aluminum for wet paint application. What I would like to know is the preparation process the same for powder coated diecast aluminum?
Karl Madcharoelectronics mfgr - Foothill Ranch, California
2006
A. Hi Karl.
A. I'd say that the pretreatment is exactly the same except that, if you go with chromate conversion coating, you make doubly sure that it is permitted to cure for 24 hours before being exposed to powder coating baking/curing temperatures. Good luck.
Regards,
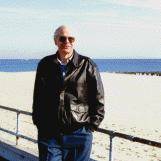
Ted Mooney, P.E.
Striving to live Aloha
(Ted can offer longterm or instant help)
finishing.com - Pine Beach, New Jersey
March 8, 2013
Q. My question pertains to which solvent should be used for prep cleaning chromated aluminum before powder coating.
One painter we were using switched from MEK to alcohol.
After this switch in solvents we started to experience a significantly higher amount of paint chipping around screw holes. The paint adhesion, specifically around these holes (where screws are torqued in) appears to be worse after the solvent switch.
Could there be a connection with this or am I looking in the wrong area?
Thanks for your thoughts,
Eric
- Woodridge, Illinois, USA
February 16, 2012
Q. Hi my name is Joff and I am having some problems with powdercoated aluminium: there are marks left on the parts after the powder has cured, these marks look like another part has been resting on it whilst in the oven. My supplier says that the chromating process is the problem. Has anyone had this problem themselves? Thanks in advance.
Joff Evans- Melbourne
May 13, 2013
A. Joff,
some pictures if you can do it, would be a big help in trying to answer this one.
Hard to see how chromate pretreatment would leave marks in the cured powder unless something was seriously wrong there. Chromate rarely leaves any significant dimensional residues.
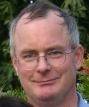
Geoff Crowley
Crithwood Ltd.
Westfield, Scotland, UK
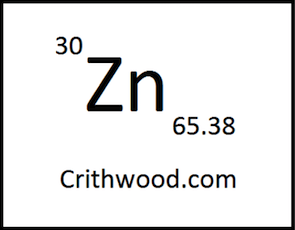
May 20, 2013
Q. I am a fabricator of equipment used on boats. My current powder coater chromates my bait boards before powder coating; I have a competitor of his vying for my business and offering to do the work for about half the price -- but he doesn't chromate before powder coating. How much does the chromate process affect/help protect my product, or do I really need it?
Rod maunderbait boards - Brisbane Australia
March 9, 2014
A. Hi Rod. I guess my question would be: if he doesn't chromate the aluminum before powder coating, what pretreatment does he do? And is he using the same brand and type of powder coating, complete with UV inhibitors, etc.?
It is relatively easy and inexpensive to have sample coupons salt spray tested to see if there is an obvious drop in quality. Cut a few small samples from your aluminum and send a couple to each of the proposed vendors, telling them to prepare and powder coat the samples exactly the way they are proposing to treat your bait boards. One salt spray test alone won't usually tell the whole story if there isn't much difference, but it will if there is a big difference. Good luck.
Regards,
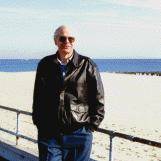
Ted Mooney, P.E.
Striving to live Aloha
(Ted can offer longterm or instant help)
finishing.com - Pine Beach, New Jersey
March 2014
![]() |
Baitmate bait boards - Brisbane Australia March 11, 2014 March 11, 2014 A. To be very brief: The Chromate gives Corrosion Protection. Trainer - Newcastle NSW Australia |
A. Hi Rod. Phosphating is sometimes done on aluminum so that the same pretreatment system can be employed on aluminum components as on steel, but phosphating of aluminum is not the equal of chromate conversion coating.
Still I caution you to proceed based more on actual results not just on theory, since anything can be done well and anything can be done poorly. William offers some sound advice which crossed in the mail with your follow-up question.
Regards,
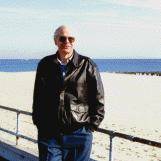
Ted Mooney, P.E.
Striving to live Aloha
(Ted can offer longterm or instant help)
finishing.com - Pine Beach, New Jersey
March 2014
March 14, 2014
A. I would like to add that I made an error in my original reply.
The conductivity reading should be <10 micro siemens not 0.
I would also add that I have had experience with a very significant and costly failure of a coating system where the applicator was advised by his Iron Phosphate pretreatment Supplier to simply add some fluoride into the initial stages; the idea being that this would provide an etchant capability to remove Aluminium Oxides.
Unfortunately this advice was followed by the Powder Applicator.
The end result was a catastrophic failure of a balustrade system on a 30 story high rise.
This ultimately led to the Bankruptcy of the fabricator who was required by law to remove, repair & replace the whole kit and caboodle.
Sage advice is to avoid risk and cheap alternatives.
Do It Once, Do It Well, Build a Better Australia.
Regards,
Bill
Trainer - Newcastle NSW Australia
----
Ed. note: Actually, the error in William's posting was ours not his. In HTML (the language of web pages), the symbol "<" is a control character which can make the characters following it disappear; we need to be on the lookout for it when posting comments, and we weren't :-)
A. I can't see if it was specified what metal was being coated.
If aluminium, then surely chromate is the best pretreatment route, but there are phosphates that are adequate (but not as good, even if Chromate has health issues).
If steel, then chromate is not very good. Iron phosphate barely adequate and zinc phosphate far better.
If galvanized steel, chromate best, zinc phosphate Ok and some other phosphates also good (eg Mn phos).
In some countries TGIC powder is not used due to its health issues, but very good performance can be obtained from TGIC free powders.
Comparing two coaters, that they use the same brand of powder isn't enough. Within any brand there are varying grades of powder, varying polymers etc. Some powders are classed as "grade 1, Grade 2 " etc Ensure that the same powder is used, not just same manufacturer of powder.
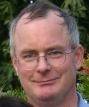
Geoff Crowley
Crithwood Ltd.
Westfield, Scotland, UK
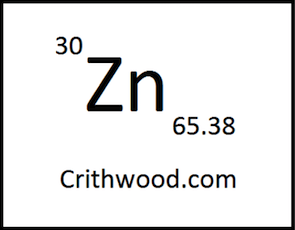
March 14, 2014
March 15, 2014
A. Hi Geoff,
Yes the TGIC issue has been raised repeatedly over the years here in OZ.
There was an extensive survey done here which concluded that the only real risk was with the raw chemical.
If you wish I can research my files and copy the report to you.
The problem with non-TGIC powders has always been that they exhibit permeability -- in other words they are porous.
Some actually create porosity during cure by the creation of water molecules.
Regards,
Bill
Trainer - Newcastle NSW Australia
Supplemental treatment after chem-film and before painting?
Q. Hello all,
Is there any post or passivation treatment on aluminium after chromate conversion coating (chromotizing) before painting or paint base ? If it is there what is the composition and parameters ?
What are the qualitative tests for chromate conversion coating or chromotizing on aluminium ?
Suggest me
Regards,
Process Engineer - Tumkur , Karnataka , India
August 4, 2014
A. Hi Surya. There are prepainting alternatives to chromate conversion coating (chem-filming) of aluminum, such as phosphatizing or phosphoric acid anodizing or proprietary passivation treatments, but chromate conversion coating is probably the most widely practiced. To my knowledge there is no supplemental chemical layer commonly added between the chromate and the priming paint.
As for the testing, I'd start by reviewing MIL-DTL-5541
[⇦ this spec on DLA]. Good luck.
Regards,
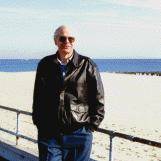
Ted Mooney, P.E.
Striving to live Aloha
(Ted can offer longterm or instant help)
finishing.com - Pine Beach, New Jersey
July 2014
Q. Please tell me what are best chemicals for aluminium pretreatment? Degreasing, De-smutting and chromotising.
Umesh Madushan- Colombo Sri Lanka
March 3, 2018
A. Hi Umesh. The typical sequence for aluminum pre-treatment is non-etch cleaner, rinse, etch, rinse, de-smut, rinse, chromate conversion coat, rinse. One good and free guideline is MIL-DTL-5541 [⇦ this spec on DLA].
There are variations in the sequence and in the chemistry depending on your needs and the specific alloy. But the formulations been proprietary chemistry, rather than generic info, since at least the early 1950's. You buy these process chemistries from suppliers like Henkel, Macdermid, Atotech, Sur-Tec, or Chemetall rather than formulating them yourself. Good luck.
Regards,
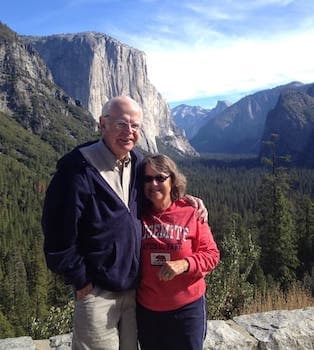
Ted Mooney, P.E. RET
Striving to live Aloha
(Ted can offer longterm or instant help)
finishing.com - Pine Beach, New Jersey
March 2018
August 27, 2018
Q. Hi, currently I'm doing aluminium powder coating and my process is as follows.
Degreasing, water rinse, De-smutting and etching, water rinse, chromating, water rinse.
Right now I don't have a pre heater and I'm doing it by sun light.
Please advice me this process is OK or not?
Also I would like to know after pre treatment giving some heat to dry the surface is giving good Quality to object?
If so what's the best suitable temperature to pre heat?
Thank you,
- Negombo Colombo Sri Lanka
A. Hi Umesh. I'm sure you realize that this is not ideal because of the chance of contamination after pretreatment and the difficulty in controlling the temperature, but necessity is the mother of invention. If you can keep the work clean, and at about 140 °F (60 °C) it sounds workable.
Etching normally precedes de-smutting. Good luck.
Regards,
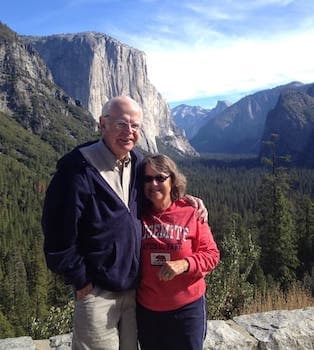
Ted Mooney, P.E. RET
Striving to live Aloha
(Ted can offer longterm or instant help)
finishing.com - Pine Beach, New Jersey
August 2018
Food-safe pretreatment of aluminum before powder coating
Q. What is an appropriate surface prep for an aluminum part which will be coated with an FDA approved powder coat for a food contact surface? This is an indoor part, and far away from salt water. Is chromate conversion necessary or even permissible considering the surface will then be powder coated?
Justin Curtis- Rochester, New Hampshire, USA
July 3, 2018
A. Hi Justin. Regardless of FDA or any other regulatory codes, I would not put hex chromate beneath the powder coating on a food surface. But the major suppliers all offer TCP (trivalent chromate products) and, maybe better yet, chromate-free conversion coatings.
Regards,
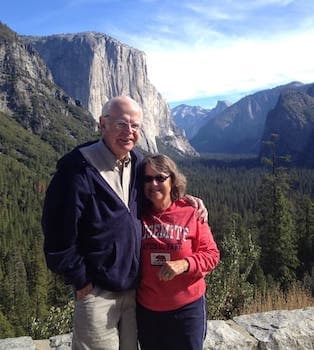
Ted Mooney, P.E. RET
Striving to live Aloha
(Ted can offer longterm or instant help)
finishing.com - Pine Beach, New Jersey
August 2018
Q. I am a hobbyist fishing lure maker and am interested in finding a cheap and economical way to etch buzzbait aluminum blades before powder painting. Any help and readily available products would be greatly appreciated.
Hobbyist - LOVELAND, Ohio USA
April 7, 2019
A. Hi James. To professional aluminum finishers, "etch" usually means the step in between alkaline cleaning and desmutting, all preceding chromate conversion coating, and it's done in fairly concentrated caustic soda ⇦liquid caustic soda in bulk on Amazon [affil link] , sometimes with additional proprietary ingredients -- but for small scale work, straight caustic soda ⇦liquid caustic soda in bulk on Amazon [affil link] will probably do. But the question would be whether that's quite what "etch" means to you.
If you're trying to apply a slight matte finish, we're probably on the same page. But you might also find that simply using a "self-etching primer" before your powder coating is sufficient. Good luck.
Regards,
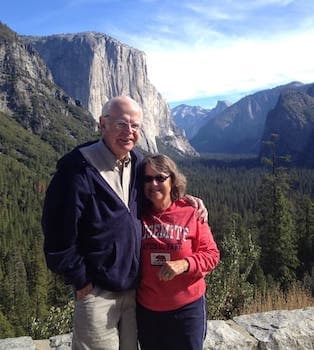
Ted Mooney, P.E. RET
Striving to live Aloha
(Ted can offer longterm or instant help)
finishing.com - Pine Beach, New Jersey
Q. What is the recommended time duration between chemical pretreatment (iron phosphate spray for steel, chem conversion dip for aluminum) and powdercoat application? Some places say a minimum of 8 hrs, others say a maximum of 8hrs, some say 48 hrs max.
What is the preferred standard if the work being done does not need to comply with any MIL/AMS specs?
- Minnesota, United States
July 15, 2019
A. Hi Nick. The real world has dust, dirt, mists, aerosolized oils, cobwebs, etc., that can re-soil a cleaned and pre-treated surface, so there may not be a "best" answer. But I'd probably go 24 hours for chemical conversion coated aluminum to allow full curing. Phosphatized steel is a subject for other threads that this one, but flash rust is not uncommon so I'd probably say as soon as practical.
Regards,
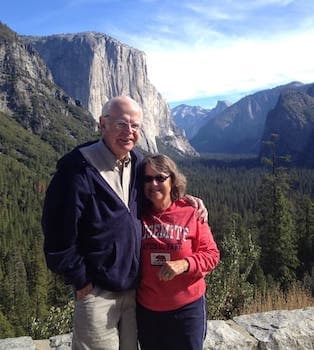
Ted Mooney, P.E. RET
Striving to live Aloha
(Ted can offer longterm or instant help)
finishing.com - Pine Beach, New Jersey
October 2019
A. In our PC plant we operate a 1 hour policy. If you can't coat the job inside an hour of pretreatment then start again.
But actually we sometimes go to 2 hours.
Certainly we do know that times like 4 hours or more just create problems. The idea of treating one day and then coating the next day is just asking for trouble.
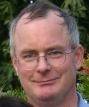
Geoff Crowley
Crithwood Ltd.
Westfield, Scotland, UK
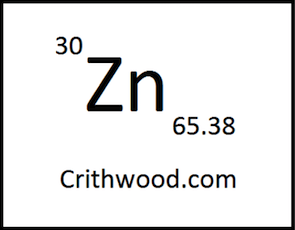
October 10, 2019
I am not on favour of using sodium hydroxide as an etch; it tends to take off layers of aluminium, as opposed to creating pits. I developed an etching system for PTFE which gave the same profile as gritblasting. I did patent it, but the patent has long run out. It involves ferric chloride
⇦ on
eBay or
Amazon [affil link] . You'll probably find the details online.
Another point: reading through the comments, I noticed that there was no mention of removing the oxide layer on the aluminium. My preference would be to use a laser to do this.
- Enniscorthy, Co. Wexford, Ireland
December 1, 2019
finishing.com is possible thanks to our supporting advertisers, including:
Q, A, or Comment on THIS thread -or- Start a NEW Thread